Brian Neff wants to leave nothing to chance. To ensure the quality of the high-value additively manufactured metal parts his company provides for the demanding aerospace and defense sectors, he believes it is imperative to have end-to-end control of the production process
Sintavia Scales End-to-end Applied Additive Technology

Case Study from | GE Additive
So, in 2012 Neff founded Sintavia to do just that. This past May the company upped the ante, when it opened a purpose-built additive manufacturing facility dedicated to Tier 1 aerospace production in Hollywood, Florida.
Powder, Quality & Process
The impressive 55,000-square-foot facility is a showcase of modern manufacturing. It currently houses a variety of additive manufacturing machines, with room to accommodate up to 60. Sintavia’s fleet of machines includes a pair of GE Additive Arcam EBM machines – an A2X and a Q20plus, as well as a GE Additive Concept Laser M2 DMLM machine.
“I would say the Concept Laser M2 is best in class for laser alignment - under the proper engineer. Also, the downskin surfaces are very nice – the best I have seen,” according to Doug Hedges, Sintavia’s president and chief technology officer.
On its eighteen high-speed machines, Sintavia is currently manufacturing with titanium, nickel, aluminum and stainless-steel alloys, as well as other proprietary powders. With three additive manufacturing printing rooms, the facility is able to separate production lines by powder type to avoid cross contamination; which is particularly important for reactive powders such as titanium and aluminum.
The facility is also equipped with laboratories, furnaces, an elaborate quality management system and, to avoid power surges or interruptions, a fully redundant power management system with a state-of-the-art flywheel UPS and 280 kW backup generator.
Sintavia continues to invest in developing surface finishing techniques for the parts it manufactures, and this summer acquired QC Laboratories Inc., a non-destructive testing services company, that already had several accreditations in place from leading aerospace OEMs. Adding QC’s expertise enhances Sintavia’s NDT capabilities for commercial aerospace applications, particularly with respect to surface finish conformance testing.
Sintavia’s new plant is close to its first facility in Davie, Florida which houses a certified, ISO17025 accredited mechanical laboratory. Together, the facilities employ about 75 people, with the company expecting the Hollywood plant alone to scale to 130 people over the next few years.
Vertically-Integrated Additive Manufacturer
Neff suggests that Sintavia “is right at the tipping point, of making not 20 or 30 part numbers, but hundreds if not thousands of part numbers. To meet that demand, we have to have the facilities in place.”
The company describes itself as a “vertically integrated additive manufacturer” and remains laser-focused on producing such components as valves, ducts, heat exchangers and chassis.
Compared with conventional manufacturing processes, additive technology enables part consolidation and the production of insanely complex geometries, while vastly reducing material waste and compressing time-to-market for components. But each technology has its place, and Sintavia sees additive as a tool that complements, rather than replaces, conventional processes.
Powder as a Differentiator
Even with its many advantages, additive also comes with its own set of challenges, such as ensuring the integrity of the raw materials –– in this case, powder.
Sintavia’s Davie lab plays a big role in this part of the process, with its CT scanner and two machines devoted to material development and heat treatment. The company always tests its incoming powders from every source.
“Powder is a differentiator,” continues Doug Hedges. “We are the only additive manufacturer that I know of who can completely conform powder. We control our own destiny for powder, because we consider powder the building block of the whole process.”
Sintavia conducts eight or nine tests on the raw materials to various standards.
“Not only do we conform powder when we buy it, we conform it when we use it. We build one build, and then pull a sample out, and conform it to those eight or nine tests again,” he adds.
But with a process that has so many variables, that is still just one part of the overall process. Not only does the powder need to be certified, so do the parts, the machines, and the production facilities themselves.
It’s a complicated journey, requiring knowledge, skills, expertise and discipline. The whole process is “very detail-oriented and unbelievably unforgiving,” Hedges notes.
Applying Best Practice from Aerospace
Sintavia remains focused on the aerospace and defense industries. Its leaders mostly come from that background, but the sector continues to demonstrate an openness to additive technologies that have not yet been seen in many other sectors.
Hedges also believes that additive offers significant potential for the oil and gas industry. When it comes to adopting metal additive manufacturing, Hedges says the oil and gas sector is lagging a little bit behind, compared with aerospace, but he terms it “an emerging field,” with many potential applications, from pipe connectors and downhole caps to parts for robotic structures used for underwater exploration. As the acceptance and use of additive technologies across Sintavia’s customer base continues to grow, the company plans to open satellite facilities across the U.S.
Hedges says that Sintavia is making the necessary investments to meet its longer-term goal of making serial production parts for additive. The firm already is self-sufficient with respect to design, fabrication, quality testing, and post-processing of additively manufactured metal components, and it is excited to take vertical integration of this technology to the next level.
If you like this article you may like "Quick Guide to Metal Additive Manufacturing for Industrial Components"
The content & opinions in this article are the author’s and do not necessarily represent the views of ManufacturingTomorrow
Comments (0)
This post does not have any comments. Be the first to leave a comment below.
Featured Product
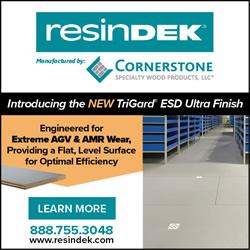