There is real momentum behind the drive towards the use of AM as an alternative to conventional manufacturing processes. However, with this drive comes a necessary focus on and scrutiny of the entire manufacturing process chain surrounding AM.
Automated AM Post Processing and Industry 4.0
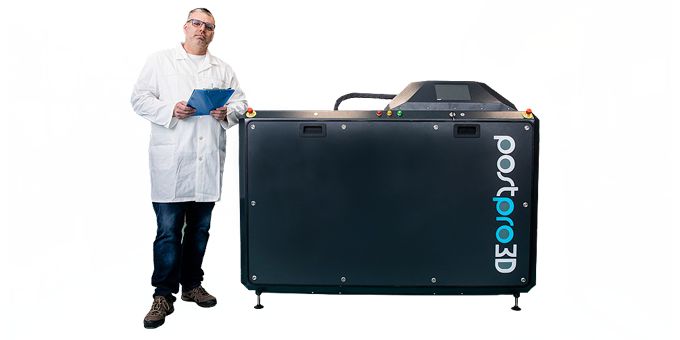
Joseph Crabtree, CEO | Additive Manufacturing Technologies Ltd
These are exciting times in the additive manufacturing (AM) sector. There is real momentum behind the drive towards the use of AM as an alternative to conventional manufacturing processes. However, with this drive comes a necessary focus on and scrutiny of the entire manufacturing process chain surrounding AM.
When used as a prototyping technology, users of AM do not need to get too bogged down in issues to do with metrology, validation, and indeed post processing.
However, when the ultimate integrity of a part for an end-use production application is of paramount importance, then AM needs to step up, and align with AM-centric support technologies that do not just work, but work cost-effectively, efficiently, and in an automated way. This is the central issue in the transition of AM from a prototyping to production technology set. Only when AM can be seamlessly incorporated into an automated production environment that qualifies fit-for-purpose, right-first-time parts, with as near zero failure rate parts as possible will it truly begin to fulfil its potential in an Industry 4.0 setting.
Work is underway to develop in-process metrology tools that can validate the design integrity of AM parts and components, notoriously tricky due to the design complexity that is possible through the use of AM. When looking at post processing, however, until recently this was not given the prominence that was necessary, and for the majority of applications; manual, time-consuming and costly interventions were necessary.
Needless to say, it does not fit the image of the smart factory of the future to see teams on the factory floor manually removing supports or powder and resin residue, and then machining critical surfaces. Beyond the fact that this is a juxtaposition of the modern with the archaic, the laborious nature of the process means that up to 60% of the cost of an additively manufactured part is generated during the post processing stage of the process chain. This is unsustainable.
AM and Industry 4.0
One key driver for manufacturers to remain competitive is to make their processes more efficient, which is why Industry 4.0 solutions (using technology to stimulate innovation and improve production processes) are gaining traction across all key industrial sectors. As these technologies are enhanced and become less expensive, as a driver, Industry 4.0 will become more and more important.
At AMT we absolutely believe that additive manufacturing has a vital role to play in the Industry 4.0 revolution.
The underpinnings of the concept of Industry 4.0 requires that OEMs interrogate their competitive model and focus on increasing capacity to deliver more cost-effective products across the supply chain through the digitization of the entire production process.
Today, this requires that these manufacturers completely re-assess their entire value chains, and apply different ways of thinking and toolsets, fusing the physical, digital, and virtual worlds together. Industry 4.0 encourages the integration of intelligent production systems and advanced information technologies.
Editors Recommendation "Rebuilding Components With Reverse Engineering"
The promotion of a digital manufacturing strategy within the context of the “Fourth Industrial Revolution” is fundamental for many manufacturing companies if they are to remain competitive in the years to come, and key to this is how OEMs incorporate new generative design tools and AM into their manufacturing regimes.
When looking at AM as a technology option with a digital manufacturing strategy, there are of course numerous and well highlighted opportunities that exist from its implementation. In a way, as a part of the Industry 4.0 ecosystem, AM is unique in that each platform is a piece of disruptive hardware technology that replaces existing production methods rather than improving them, and this requires that OEMs overcome barriers to adoption, and also re-evaluate preconceptions when it comes to design and production.
Post processing
One area that needs renewed and vigorous attention is the area or post processing. Today, many OEMS that have invested in AM are struggling with the implications of post processing. Considering the “promotion of a digital revolution manufacturing strategy within the context of the Fourth Industrial Revolution “ mentioned above, it stands out as a huge anomaly.
For some companies, considerable areas of factory floor space are devoted to the equipment and personnel needed to tackle post processing operations, often considerably more than is devoted to the actual additive manufacturing platforms. By its very nature, the AM build part of the process is relatively simple, once the parameters for the build are locked in. Upload the file, prepare the machine / materials and then it is very much a case of just push the button. It is the post processing stage once the part comes off the machine that is a burden, variously requiring de-powdering, cleaning, blasting and sanding by humans! This is before the parts are subjected to full validation and quality control procedures.
One good thing is that post processing operations are much the same for AM and conventionally produced parts, so the requisite skill sets already reside in most manufacturing facilities (OEMs and throughout the supply chain) as they bring AM in-house. But this is not the issue. The issue is that manual intervention is not in keeping with Industry 4.0, and what is vital when truly using AM as a production technology is the ability to scale up and automate processes in order to promote real, high volume manufacturing.
Scaling up at speed is only one part of the equation, however, and an equal emphasis needs to be given to accuracy and repeatability. Manual intervention is not just slow, but it is also notoriously difficult to predict consistency.
Automated Post Processing
With the above in mind, it is not surprising that a number of companies have focused on automated solutions to confront the AM post processing problem. It is important to realise, however, that not all automated post processing solutions are the same, and there are some important questions that you must ask a supplier in order to ensure best ROI.
In general terms, an automated post processing solution is provided by a combination of proprietary software, hardware, and chemistries. But beyond that, the playing field is anything but even.
Some companies are busy adapting automated post processing solutions for conventional manufacturing to make them applicable to AM parts and components. This is one way to go, but fraught with problems too numerous to mention.
At AMT we begin with a premise that informs all the solutions we advocate. Any solution needs to be designed specifically for AM, and be sensitive to the vagaries of a truly automated AM production process and must also be sustainable. The company’s goal is to develop a portfolio of innovative digital and automated post processing solutions that increase efficiency and reduce the overall time and costs of production with AM, specifically with polymer AM processes and thermoplastic materials.
Polymer-based powder-bed processes not only require significant powder handling and removal post build, but also invariably require infiltration operations, as well as finishing processes, particularly if aesthetics are important alongside the strength advantages that laser sintering offers. If coloured parts are required, then this is also applied at the finishing stages of post processing.
With filament thermoplastic material processes, the very nature of the AM process (no matter how refined) results in a stepping effect. The traditional post processing steps required to eliminate these process-specific results are considerable, costly, and time consuming. An automated post processing solution like the one developed by AMT Ltd for smoothing high volumes of thermoplastic polymer parts to an injection moulded surface quality removes one of the biggest hurdles to the serial production process chain.
AMT’s solution is the PostPro3D® range of hardware solutions, which integrates new systems, software and virtual services. The simplicity and speed experienced by the user belies the intelligent and complex capabilities of the system, which is built on the proprietary BLASTTM process.
Simplicity is the key. Post-build, the 3D printed parts can be removed from the machine, loaded onto a rack, and placed into the PostPro3D® post processing chamber. The user then selects the appropriate program and the process starts and runs for 90-120 minutes, after which the parts can be removed, inspected, and are fit-for-purpose.
Parts processed in the PostPro3D are subject to a physiochemical process that involves converting a proprietary but wholly safe solvent into vapour under precisely controlled vacuum and temperature conditions. In turn, this precisely refines the surface of each part to ensure a perfectly smooth finish, equivalent to that of an injection moulded part. Moreover, the process also seals and strengthens parts, essentially improving their mechanical properties— such as elongation at break — compared with how parts were when they came out of the 3D printer.
The intelligence of the PostPro3D systems goes beyond their physical process capabilities however, as they have been designed to be connected through an IIoT network, where vital data is analysed in real-time. This allows for new insights on process performance, which can subsequently be shared amongst the global fleet of PostPro3D machines, and made available via software updates to continually upgrade performance, all while protecting individual IP. Moreover, this connectivity capability also allows for integration with other intelligent devices and workflow automation software across the manufacturing process chain.
Questions to Ask
So, when selecting an automated AM solution ask your supplier the following questions.
-
Is your system environmentally friendly and sustainable?
-
Can your system provide injection moulded surface characteristics?
-
How simply can your system be integrated into a digital production system?
-
How long does a standard post processing operation take?
-
Can your process seal and strengthen AM parts?
-
How upgradeable is your system?
The ways in which your shortlisted supplier is able to answer your questions should give you the insight you need to select the most efficient and cost-effective AM automated post processing solution, which will assist in your success using AM as a true mass production technology.
If you like this article you may like "Quick Guide to Metal Additive Manufacturing for Industrial Components"
The content & opinions in this article are the author’s and do not necessarily represent the views of ManufacturingTomorrow
Comments (0)
This post does not have any comments. Be the first to leave a comment below.
Featured Product
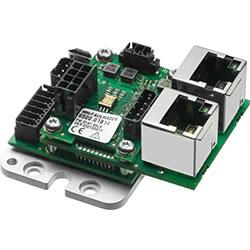