Even the highest quality industrial weighing scales are affected by several factors such as their surrounding environment, load cell accuracy, interferences etc. To prevent the negative impact of these factors, it’s important to understand them.
4 Factors Impacting Accuracy and Repeatability of Your Scales
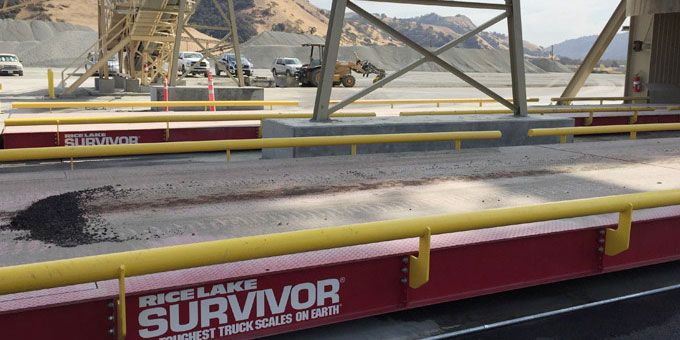
Kevin Hill | Quality Scales Unlimited
Even the highest quality industrial weighing scales are affected by several factors such as their surrounding environment, load cell accuracy, interferences etc. To prevent the negative impact of these factors, it’s important to understand them. Described below are 4 such common factors which impact the accuracy and repeatability of your scales.
Environmental Factors
The environmental factors which affect the accuracy and repeatability of your truck scales are:
-
Air Movement – Irrelevant of your scale being used indoors or outdoors, air movement including the air currents generated from air conditioning units or ducts can affect the performance of the scale.
-
Pressure - Differences in the air pressure of the environment in which the industrial weighing scales are calibrated and used can also lead to inaccurate measurements.
-
Vibration – Equipment placed near the scales can cause the load cells to misinterpret vibrations from the equipment thus resulting in incorrect readings.
-
Debris – If the scales are not cleaned regularly, dirt and debris can build up on its platform. This makes it impossible for the load cells to completely support the weight placed on the scale for measurement thus giving incorrect readings.
Load Cell Accuracy
The following elements should be factored in when determining the source of issue with respect to load cells:
-
Response times can be a reason for errors if the load cell is being used continually with little break time in between weighing sessions.
-
Nonlinearity can also be a trigger for errors. It is the maximum deviation of a load cell’s calibration curve from a straight line drawn between zero-weight and maximum rated capacity.
-
Creep is the change in the measured weight when a load is left on the cell for a long duration.
-
The difference in the scale output when the same load is measure twice is referred to as Hysteresis.
Interference
Interferences with the electrical signal of the load cell which can cause incorrect measurements are:
-
Radio Frequency Interference (RFI) and Electromechanical Interference (EMI) are referred to as electrical noise and can cause disturbances in the load cell signal sent from the cells to the weight controller. Their sources include portable two-way radios, static electricity, lightning, large power lines, electromechanical relays and solenoids. To avoid their interference, isolate the load cell low-voltage signal with a shielded cable and route it in a separate conduit. Ground this shield in a way that it doesn’t form a ground loop.
-
Moisture in junction box can reduce the capacitance between signal lines which in turn can cause load cell excitation lines to couple with signal lines to create electrical noise. The result is inaccurate measurements. To avoid this, use waterproof junction box and load cells which are hermetically sealed at both entries. The strain gauge area especially should be welded shut.
-
If the load cell cable conduit is subjected to huge temperature variations, resistance changes can be caused in the cable. This can further result in excitation changes which result in load cell’s signal variations. Hence, use six-wire load cell cable which enables the weight controller to make ratiometric readings of the load cell signal which ignore variations induced by excitation changes.
Other Factors
Some miscellaneous factors which can also impact the accuracy and repeatability of your scales are as follows:
-
With human involvement, there is always a chance for error. This cannot be eliminated entirely but can be curtailed to a great extent with appropriate training and strict work standards.
-
Proper loading and unloading of the scales also impacts their performance. Ensure that the mounting structure underneath the scale is capable of supporting the scale, its components and its loads without flexing. Improperly aligned loads can result in inaccurate readings as the load cells can interpret the force as weight. Make sure that the mounting hardware is operating correctly as the weight of load placed on the load cell is directed here. If the scales have less than ideal support legs to curtail instances where the legs will spread under stress, add cross braces.
Consider both mechanical and operational factors when it comes to the accuracy of your industrial scale calibration and its repeatability to avoid related setbacks and losses.
About Kevin Hill
Kevin Hill heads the marketing efforts at Quality Scales Unlimited in Byron, CA. Besides his day job, he loves to write about the different types of scales and their importance in various industries. He also writes about how to care for and get optimized performance from different scales in different situations. He enjoys spending time with family and going on camping trips.
The content & opinions in this article are the author’s and do not necessarily represent the views of ManufacturingTomorrow
Comments (0)
This post does not have any comments. Be the first to leave a comment below.
Featured Product
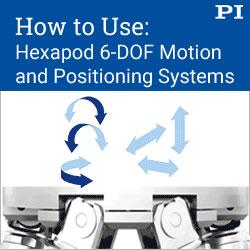