Article from BigRep. As FFF extrusion technology reaches the peak of its development cycle, it becomes less likely that the technology’s quality will meaningfully improve. Additive manufacturing must be rethought from its foundation.
What is MXT? (Metering Extruder Technology)

Article from | BigRep
At the height of additive manufacturing’s growth, a promise was made to advance 3D printing technology to enable anyone to produce anything anywhere. BigRep is proud to have developed the revolutionary Metering Extruder Technology (MXT®) to finally meet that promise and provide industrial manufacturers of any size the dependable tools they need to produce without limits.
As FFF extrusion technology reaches the peak of its development cycle, it becomes less likely that the technology’s quality will meaningfully improve. Additive manufacturing must be rethought from its foundation, the extruder, to achieve the long-sought goals of repeatable end-use parts with engineering-grade materials.
Featured on the upcoming BigRep PRO and EDGE large-format 3D printers, MXT has taken on the challenge and is setting the new additive manufacturing standard.
How Does it Work?
If FFF 3D printing is like a hot-glue gun, MXT is a syringe.
In the FFF process material is melted as it passes through an extruder’s hot end. Unlike FFF, MXT melts filament in advance and stores it in an internal reservoir. This extra step enables unprecedented speed and precision in the printing process by working with material that is stored at its ideal temperature and is uniformly viscous throughout the print.
Using a reservoir of molten filament allows MXT to print with unprecedented control due to the local force exertion. Where traditional FFF technologies push solid filament through extruders by exerting force at a distance from the hot end, thus creating a gap of time between the cease of force and actual filament extrusion. MXT has implemented a servomotor to feed the reservoir and a metering pump just above the hot end powered by a servo motor as a source of controlled, local force. With this highly accurate feeding combination, MXT pushes an incredibly measured volume of uniformly viscous filament through the hot end locally. This eliminates time gaps between the mechanical systems and drastically improves printer precision, enabling better results at a faster pace.
The process makes printing five times faster than traditional FFF printers with a throughput of up to 500 cubic centimeters per hour (cm3/h) at maximum extrusion rate with its finest 1-millimeter nozzle. Because of its level of accuracy and liquid-filament deposition, MXT extruders don’t need to take the extra steps that FFF printers do when turning corners, stopping, or rapidly starting and stopping; drastically reducing print time.
MXT also eliminates oozing by implementing a secondary force called retraction, where the extruder’s metering pump runs in reverse to eliminate pressure in the nozzle, stopping or pulling any filament already past the reservoir to halt extrusion accurately and instantly.
Why Does it Matter?
With traditional FFF extruders, speed is limited by the necessity of melting filament as it passes through the hot end. If material is pushed through too quickly it won’t melt and users risk delamination – layers of printed parts separating. MXT avoids this issue entirely by heating filament to ideal extrusion temperature in the reservoir.
Upon announcing MXT, Fabbaloo's Kerry Stevenson called it “the single most important advance in 3D printer extrusion technology I’ve yet seen.” It’s an advancement that will enable the industry to continue its exponential improvement of additive hardware – making printing faster, better quality, with more materials.
As FFF extrusion technology reaches the peak of its development cycle, changing to the base technology evolving the foundation – extruders – becomes the only way to continue advancing the technology’s capabilities and industry applications.
Repeatability, speed, precision and the problems of force and excess inherent in the FFF printing process can only be resolved by reinventing the extrusion process.
The content & opinions in this article are the author’s and do not necessarily represent the views of ManufacturingTomorrow
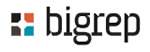
BigRep
Founded in 2014, BigRep set sail to transform the 3D printing and manufacturing business. With its 1m3 volume, the BigRep ONE opens the gateway to a new dimension of 3D printing and 3D manufacturing, while the BigRep STUDIO allows fast and precise large-scale 3D printing. From furniture to vehicles to robotics, we think everything is possible. We want you to envision everything from human scale robot parts, sculptural artworks in all their full-dimensional glory, and dream the impossible world-changing designs of tomorrow while enabling you to print them today using one of our 3D printers.
Other Articles
How 3D Printing is Paving the Way for Grading Contractor, C.J. Moyna & Sons
3D Printing Produces Engine Covers To Accelerate Aircraft Maintenance
3D Printing Powers Wind Turbine Research At TU Berlin
More about BigRep
Comments (0)
This post does not have any comments. Be the first to leave a comment below.
Featured Product
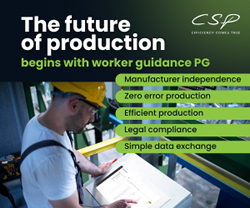