Without compromising quality, focusing on optimizing plant processes will reduce time and money spent, therefore increasing profits. Here are five optimization techniques for manufacturing facilities.
Technology to Optimize Your Manufacturing Plant
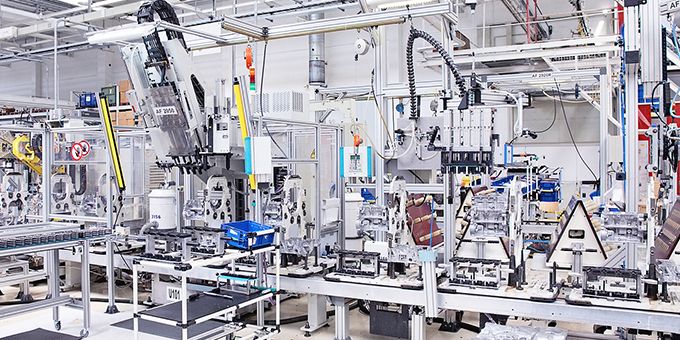
Megan Ray Nichols | Schooled by Science
Manufacturing plants of all sizes are looking to improve their bottom line. While profits can be increased by raising additional revenue, this is often done by the sales team. Sales are heavily reliant on an increase in consumer demand or actions taken by competitors.
Manufacturing companies can increase their bottom line with little influence from external circumstances by minimizing cost. If sales remain constant, operations team members are able to minimize costs and the plant will be able to increase the profit on each unit produced without raising prices or increasing sales figures.
Without compromising quality, focusing on optimizing plant processes will reduce time and money spent, therefore increasing profits. Here are five optimization techniques for manufacturing facilities.
1. Analyze Existing Workflow
"If it ain't broke, don't fix it" is fine if your plant is looking to remain stagnant when it comes to growth. But the rest of us looking to practice continual improvement must reflect on our existing workflows.
This begins with people. The people your organization employs are some of the most valuable assets your company possesses. It would be a disservice to not reflect on how you're allocating these resources. Ensure that the leader is establishing safe and clear objectives, and that the employees are in the right places to maximize their individual and team efficiency.
Once the people are in the right place, monitor the processes they are using. Are the processes running efficiently? Where are the bottlenecks and pain points? By streamlining processes, we can alleviate areas of buildup so that production runs smoothly with little idle time.
2. Production Planning
Production planning can be overwhelming. Plants have thousands of production orders for various projects. There are numerous moving parts in each order, like what equipment is needed, how long it will take, customer specifications and more. The list goes on.
Allocating time and equipment to each project is sort of like completing ten 500-piece puzzles at one time with all the pieces jumbled up. Each puzzle or project has its own intricacies, complicated by the other looming projects.
Meeting the constraints of each project is so much easier with the use of modern production planning, or APS (Advanced Planning and Scheduling) systems. Solvers within the software model optimize and automatically execute production planning decisions. This ensures that the optimal production plan is created with minimal lag time for production planners or project managers. After all, time is money.
3. Take Care of Industrial Equipment and Reduce Downtime
Utilize a process cooling system to reduce the operating temperature of equipment in order to lengthen the lifespan of these large capital investments. Process cooling uses a chiller unit to draw heat away from the equipment to improve efficiency. With lower operating temperatures, the process equipment lasts longer and becomes safer for employees. Investing in this energy-efficient system minimizes the cost of running the equipment and the lost production time spent repairing equipment.
Investing in equipment that can gather information about its condition, performance and efficiency is another way to go. Companies offer aftermarket sensors that make retrofits of existing equipment easy. When machines receive connectivity, they can report on conditions like higher-than-usual temperatures and the presence of vibrations, or detect leaks and malfunctions that might pose a risk to other equipment or merchandise. Real-time condition monitoring makes maintenance truly proactive.
Both of these techniques — process cooling systems and predictive maintenance — help prevent unexpected downtime from broken machinery.
4. Just-in-Time Production
Try to maintain optimal inventory levels. Producing too much inventory leaves the excess sitting in storage, while producing too little inventory risks your company not being able to fulfill orders.
One principle of lean manufacturing is just-in-time (JIT) production. JIT is the inventory management technique of producing only what is necessary and having little to no inventory on hand otherwise. Orders are produced as they are received, rather than being pulled from inventory.
This technique saves on storage costs, decreases waste and increases efficiency, all while delivering prompt results.
In order to prevent orders from being filled late, an inventory management system is very helpful. The software tracks inventory and notifies managers of shortages. They also facilitate the favored vendor relationships that are necessary for JIT manufacturing. Without an inventory of raw materials, we must rely on our vendors to deliver materials on time and without damage.
5. Embrace Technological Advances
In order to optimize production, we should embrace advances in manufacturing technology. As robots and software become more advanced, the manufacturing industry is shifting away from a reliance on manual labor.
Human capital is no match for robotics and software when it comes to executing at a high level for extended periods of time. However, human capital has the ability to conceptualize and analyze systems and data. While machinery may take jobs from manual laborers, we are able to empower them out of their current roles and into jobs managing and analyzing the new machinery.
These jobs will be in high demand and will liberate human capital into new and more profitable roles. Businesses will benefit from the shift in labor because we will be able to produce more items of higher quality, in a safer way and at a lower cost.
By optimizing processes in manufacturing facilities through analyzing workflows, engaging in planning production, reducing downtime, implementing JIT manufacturing and embracing advances in technology, we can increase the bottom line without reliance on sales goals or competitor actions.
The content & opinions in this article are the author’s and do not necessarily represent the views of ManufacturingTomorrow
Comments (0)
This post does not have any comments. Be the first to leave a comment below.
Featured Product
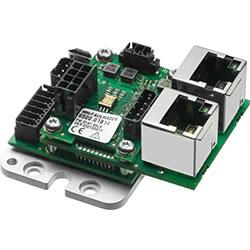