Logistics kitting organizes and even assembles parts used in the manufacturing of a product so they can be delivered to the point of use, saving time on the line. It is often the best example of Lean Manufacturing in practice, eliminating wasted time in production.
Kitting Improves Productivity and Reduces Labor Costs
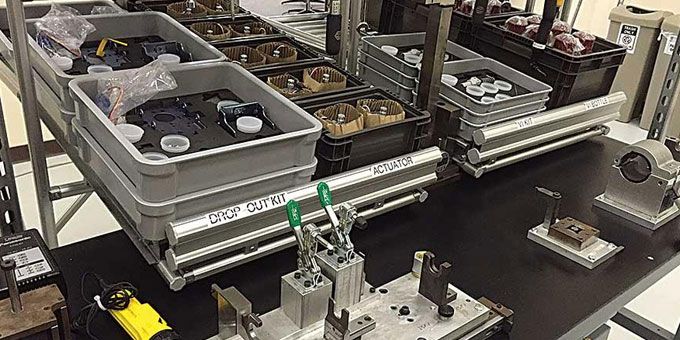
Travis Smith | WithoutWire Inventory Sciences
Kitting in the manufacturing environment represents a kind of intake process. Logistics kitting organizes and even assembles parts used in the manufacturing of a product so they can be delivered to the point of use, saving time on the line. It is often the best example of Lean Manufacturing in practice, eliminating wasted time in production. These two types of kitting are not mutually exclusive as they combine both manufacturing and logistics. The latter is performed in a lower-cost warehouse, such as a third-party logistics providers (3PLs) who manage suppliers’ material, prepare it, and deliver it just-in-time (JIT).
The benefits of kitting are well known because assembly workers immediately become more efficient. Manufacturers who do not utilize some form of kitting are bottle-necked in material flow. Kitting starts with the production team defining the kit of combined parts. 3PLs can be involved in this process and often can provide good advice on how to package kits in the most logical and effective way.
Space unitization maximized
Freeing up space is one of the key benefits of kitting services for Lean Manufacturing environments. By moving component inventory, kitting services allow manufacturers to devote more floor space to production. Costly manufacturing space to store parts, packaging, and trash is antithetical to Lean Manufacturing principles. Growing manufacturers need to expand production, often moving the component materials off site, allowing for the additional space needed while avoiding capital-intensive expansion projects.
On-site or off-site, kitting improves productivity and reduces labor costs
Pre-sorted kits save time and labor by ensuring necessary components are available at the point of use. Kits can also be created by work cell or routing. As a Work in Progress (WIP) moves from cell 1 to cell 2, the creation or assignment of the next pick can be triggered.
If parts are not kitted, it is time-consuming for assemblers to search inventory, pull parts, and log usage. Because of this strategic material flow, manufacturers reduce inventory and improve cash flow with kitting. Combined with managed inventory, materials arrive in the plant and on the line, as needed. Suppliers ensure appropriate stocks are available to support daily production and retain ownership of inventory until consumed. It is important to automate the exceptions to this kitting process. Manufacturers who deliver components to a manufacturing cell may discover that they really do not need “X” component; they now need “Y.” Kitting combined with real-time inventory requests is most valuable.
Maintaining increased volume AND profitability
Labor resources, especially with historically low unemployment, are in short supply. Optimizing the labor force starts with picking, the most important process in inventory processing science. For most inventory-centric companies, the outbound side of the inventory is where most companies generate profit, yet the most labor intensive.
There are specific techniques and sequences which ensure that profitability is not consumed by poor planning. First, pick each, case, and pallet in separate zones by separate individuals for fast parallel picks. Second, combine a set of picks into one wave set with options to auto-ship or move to packing with secondary QA (quality assurance) checks. Third, license plates (LPs) are automatically assigned during picks for optimal staging, packing, shipping, and site transfer receipts. Another facet of operational labor reduction impacts cross site moves. While they do not reduce a lot of scans, they do simplify accounting data entry processes. Fourth, institute a short pick, unpick cancelled orders, or partially staged picks with a hold status. Fifth, auto-assign or manually assign orders in round-robin fashion. Sixth, order picks with routes are automatically distributed in reverse stop order. Seventh, review FEFO (First Expired, First Out), FIFO (First In, First Out) primary pick, or hybrid models.
© 2019 WithoutWire
A collection of inventory items or “License Plates” reduce scans for any operation
Picking settings must allow a plant manager to enable wave set orders. A wave set is the ability to combine multiple orders into a single work set; implementing a QA process or pick and pack scenario in the warehouse.
A two-step pick process identifies when the wave set is complete; it will be staged and then each order will have to be picked individually. Movement within a manufacturing facility can be within the building and cross-site moves within transit locations. An agile system is a requirement to support growing manufacturing companies.
Component replenishment
The timing of movements for raw materials to manufacturing staging is a big part of high performance, best-practice, Lean Manufacturing. There are tools to assist in creating exceptional material flow.
From plant managers to operations directors, it is critical to have the ability to view raw material needs directly from the kitting and manufacturing screen so action can be taken as required. Without this immediate, real-time data, the line stops, overall equipment effectiveness (OEE) decreases, productivity and throughput suffer, and profits are lost.
Technology solutions, like WithoutWire, create picks that direct staging to the appropriate manufacturing location. Manual bin moves can be used at any time to handle more complex needs. Setup replenishment is quickly established with MIN/MAX levels ensuring the stream of constant inventory throughout the manufacturing process.
About Travis Smith
Travis Smith is the CTO and Founder of WithoutWire Inventory Sciences. He is a graduate of NDSU school of Electrical Engineering and resides in Maple Grove, MN with his wife and 8 children. In 1998, he co-founded Inetium, a software development consulting firm and branched off to form Appolis in 2001. He provides supply chain-based consulting and product strategy for a variety of industries with a unique combination of software architecture and business process experience.
The content & opinions in this article are the author’s and do not necessarily represent the views of ManufacturingTomorrow
Comments (0)
This post does not have any comments. Be the first to leave a comment below.
Featured Product
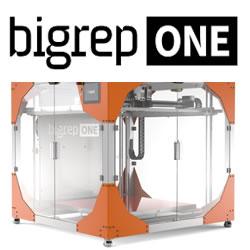