There are three primary uses for ESD safe plastics: electronics manufacturing (e.g. ESD safe jigs and fixtures for printed circuit board manufacturing), materials in a combustible/explosive environment, and nuisance static charge elimination
Electrostatic Discharge (ESD) Safe Materials for 3D Printing
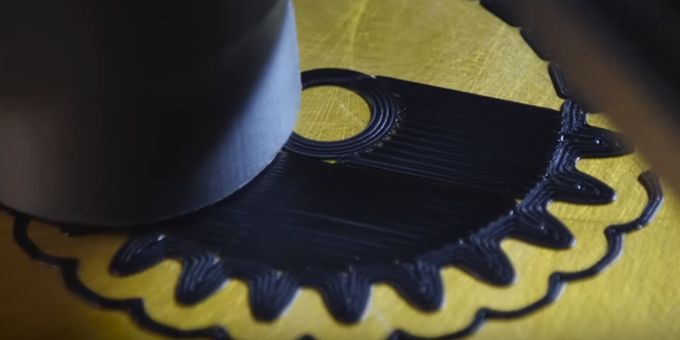
Q&A with Brandon Sweeney, Head of R&D for Materials and Co-founder | Essentium Inc.
Tell us about Essentium Inc. and your role with the company.
As head of R&D for Materials and Co-founder at Essentium Inc., I lead research and development into the ground-breaking materials Essentium is creating to revolutionize industrial additive manufacturing. My work at Essentium combines breakthroughs in thermoplastic polymer 3D printing through proprietary military grade electric field technology and carbon nanotube-coated filament, the company’s FlashFuse™ Filament technology, which together more than doubles the interlayer strength of a traditional 3D printed component.
These technologies combine to enable Essentium to provide industrial 3D printing solutions that are disrupting traditional manufacturing processes by bringing product strength and production speed together, at scale, with a no-compromise engineering material set.
Tell us about Electrostatic Discharge (ESD) Safe Materials and their increasing role in 3D Printing. Where are you seeing the biggest demand?
The best way to understand ESD safe 3D printing materials, is to understand where ESD safe plastics have been used in industry historically.There are three primary uses for ESD safe plastics: electronics manufacturing (e.g. ESD safe jigs and fixtures for printed circuit board manufacturing), materials in a combustible/explosive environment (e.g. all the plastic parts near a gas pump), and nuisance static charge elimination (e.g. powder conveying materials). We see the biggest demand in the electronics manufacturing industry where millions of new electronic devices are being developed and manufactured each day. Every one of these devices requires a multitude of custom jigs, fixtures, pallets, nests and assembly aids to produce. Traditionally these components are made in medium to low volumes with traditional subtractive manufacturing techniques (CNC milling). This results in long lead times and very expensive tooling charges that get passed on to the customer as non-reoccurring engineering expenses (NRE). Additive Manufacturing is changing all of this by allowing manufacturers to design jigs and fixtures to be 3D printed with advanced engineering-grade materials that meet ESD surface resistance requirements. Lead times can be reduced from weeks to hours, multi-component assemblies can be reduced into a single 3D printed part, and the cost savings in materials and man-hours typically exceeds 90 percent. The key to all of this is proper materials that can survive the demanding processing steps associated with electronics manufacturing.
How are traditional ESD-safe materials developed and what challenges do these present for electronic assemblies?
To make an insulating polymer electrically conductive in the range specified for ESD-safe materials, you typically add a conductive filler like carbon black, or graphite to the polymer forming a composite. Traditional ESD-safe materials are designed with injection molding or machining in mind. Most of the 3D printable ESD-safe materials on the market were simply borrowed from injection molding formulations. The problem with that is you end up with materials that are not optimized for an additive manufacturing process. Current ESD-safe materials tend to be brittle, chalky, they rub off like a pencil on sensitive devices, and they aren't formulated with high performance engineering base resins. Most of the ESD "safe" filaments available today fail to meet the demanding standards for materials used in a clean electronics manufacturing environment.
What are the tangible and useful properties of carbon nanotubes in creating ESD-safe materials?
Carbon nanotubes are a cutting-edge class of nanomaterials that solve many of the challenges associated with other conductive fillers. Carbon nanotubes can create an electrically conductive network in a polymer matrix at very low loading levels because of its incredibly high aspect ratio (ratio of length to diameter). Carbon nanotubes are also incredible conductors of electricity, which allows a very wide range of nanotube-polymer conductivity values from electrically conductive (think 3D printed circuits and electromagnetic interference (EMI) shielding properties), to ESD-safe static dissipative values, all the way down to electrically insulating (no nanotube loading). We can select the precise material properties we want by tuning the loading level of nanotubes in the polymer. Carbon nanotubes also tend to reinforce the polymer matrix making it slightly stronger and more wear resistant. The nanotubes are completely bound to the polymer matrix meaning cannot rub off onto sensitive devices or cosmetic surfaces.
How do you create a strong bond between thermoplastics and carbon to eliminate the possibility of sloughing conductive particles onto electronic assemblies during manufacturing?
We use high quality, high purity carbon nanotubes and a proprietary extrusion process to extrude a multilayer 3D printer filament that concentrates the nanotubes onto the surface of the filament rather than throughout the entire volume of the material. This creates a high quality ESD safe material where the nanotubes are used intelligently and sparingly, resulting in a higher performance material without excess conductive particles with the potential to slough off.
How are Essentium’s Z filaments solving unmet needs in the industry?
Our materials address two major pain points: ESD safe 3D printing materials that are non-marring and do not compromise its engineering properties. We've discussed the first point already. The counterpart to being chalky is brittleness. Most ESD safe materials have so much conductive filler added to the polymer that it begins to alter the mechanical properties of the base polymer resulting in lower toughness, impact resistance, and elongation at break. To counteract this, manufacturers will generally add plasticizers to restore some of the ductility to the composite. This in turn leads to more compromises in the mechanical properties of the material reducing its overall performance. Essentium “Z” ESD-safe filaments eliminate these compromises. Because the bulk majority of the filament in the core is the base polymer, you are able to retain all of the mechanical and thermal properties of the material. The conductive outer layer of the filament is on the order of a few microns after printing (fractions of the width of a human hair) and does not appreciably alter the physical properties, it simply adds an ESD-safe layer embedded throughout the entire printed part. One final benefit of this process is cost. High performance conductive fillers are typically expensive and can affect the base price of the polymer resin significantly. With our process, only a small fraction of the filament mass is composed of the nanotube compound, so we can produce our materials without a high cap on the cost of goods sold (COGS). This means that as we continue to scale our materials in the industrial market place, we will always be able to offer competitive pricing for our high performance, no-compromise materials.
The content & opinions in this article are the author’s and do not necessarily represent the views of ManufacturingTomorrow
Comments (0)
This post does not have any comments. Be the first to leave a comment below.
Featured Product
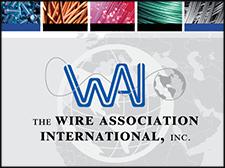