Laser Metal Sintering is a material processing technique which considers binding (sintering) pulverized particles (powder) together due to a diffusion of its micro-melted outer layers into each other produced by a pulsed laser source.
3D Laser Metal Sintering: Q&A with Laser Photonics Corporation
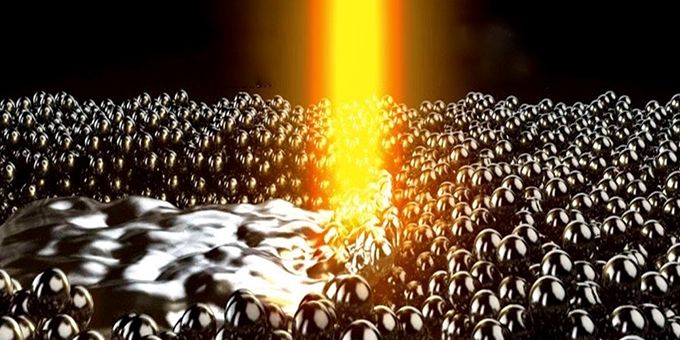
Contributed by | Laser Photonics Corporation (LPC)
Tell us a little bit about Laser Metal Sintering
Laser Metal Sintering is a material processing technique which considers binding (sintering) pulverized particles (powder) together due to a diffusion of its micro-melted outer layers into each other produced by a pulsed laser source. A similar approach is derived, by mean of using laser source, in selective laser melting (SLM), aka direct metal laser sintering (DMLS) by bonding metal powder particles that, now, undergo complete phase of melting. The idea of implementing SLM in 3D metal printing revolution originates back in 1980s when Japanese researcher Hideo Kodama discovered polymerization of some photosensitive polymers under UV light. The invention is known as stereo-lithography and fond its use in many areas for more than 25 years. The procedure of printing a metal product is similar to the one implemented for stereo-lithography, and consisted of slicing a 3D model onto layers (cross-sections of the geometrically defined part), and then sinter metal particles by scanning a cross-section of the powder layer with the laser beam. Next, the building bed lowers down by the distance of predefined 3D slice width followed by spreading over with the new powder amount. Thus, a 3D part is build up layer by layer from the fused powder particles while unprocessed powder could be recycled.
Are there any physical limitations on achieving surface integrity parameters?
DMLS technique theoretically has no limitations on achieving 3D products with complex geometries because during the building process there is no need to provide support structures (such as in FDM) – the powder itself serve as a support resulting in product designs that cannot be manufactured using conventional methods like machining where material cannot be physically removed. The only drawback in DMLS technique is that it is practically impossible to build a 3D closed hollow sphere since there is no way to remove non-sintered powder from it.
Are there any physical limitations on achieving material density using 3d laser sintering?
Theoretically speaking, it should not have any limitations on achieving the final product with properties as an initial raw material. However, the process born on the edge of the new millennia is still yet to be totally understood. The major problems discovered states that oxygen should be avoided during sintering process, powder beds should be preheated to prevent micro-cracking due to thermal stress, and other technical factors. DLMS still undergoes theoretical studies that examine and control a numerous amount of parameters of this technique such as laser power, scanning speed, powder bed temperature, oxygen concentration in a build chamber, and much more. Every step in this exploration is bringing DLMS theory to the perfection. Laser Photonics is constantly researching and investing into perfecting the DLMS theory with their own research facility.
Are there known laser sintering throughput limitations when you are trying to achieve the finest surface quality of the printed part?
The quality of the surface (referred also as roughness and surface finish) is directly related to height of the powder layer and a laser beam spot size. The tinier the powder layers, the finer the final product. However, with this course, the buildup time is raised drastically without post-processing. Laser Photonics manufactures an industrial grade CleanTech products devoted to surface treatment and surface preparation. This technology is used in depainting, degreasing, oxides/rust removal, and surface pre/post welding treatment. Recently the application of this technology was broadened by using it for surface smoothening/reshaping of laser sintered products.
How would one overcome brittleness of printed parts made of aluminum or titanium powder?
A number of DLMS unit parameters influence the brittleness of final product such as laser power, scanning speed, powder particles size and composition, bed temperature, and so on. All of those parameters are tied up to the main one – the build chamber size, and could be adjusted consequently during the test procedure.
What are some of the applications you are seeing 3D Laser sintering in now?
Medical Applications:
Early 3D adopters of Laser Metal Printing for medical orthopedics benefit significantly from the ability of 3D Laser Metal Printing to manufacture complex geometries and structures with high grade powders such as titanium. From patient-specific implants to ultimately, volume production of orthopedic implants featuring hybrid structures and textures; 3D Laser Metal Printing has the potential to unlock manufacturing capabilities that combine free-form shapes and intricate lattice structures that improve Osseo integration, leading too much improved patient outcomes and reduced operating time-tables.
Industrial Applications:
From tooling inserts featuring conformal cooling channels to lightweight structures for challenging and critical high technology applications, 3D Laser Metal Printing significantly reduces the constraints on designers. This design freedom results in optimized structures and shapes that would otherwise be constrained by conventional processes or the tooling requirements of large volume production. 3D Laser Metal Printing helps to reduce lead times, reduce tooling costs & permits the creation of designs not previously possible.
Aerospace Applications:
From aero foils to lightweight devices with comprehensive and intricate internal structures, 3D Laser Metal Printing significantly reduces the constraints on designers in the aerospace industry. 3D Laser Metal Printing helps to open the horizons in design, lead times, and tooling costs allowing the creation of structures not previously imaginable.
Military Applications:
From warheads and special purpose bullets to quick response spare parts for military equipment, 3D Printing opens the way into a new generation of warfare and detonation devices manufacturing for both military and civil purposes. 3D Printing allows replacing 100’s of warhead components with just a few, achieving intricate designs to control explosion patterns, blast directions, and other specifications of the warheads for specific applications.
What do you think is needed to move 3D printing into large scale use in Manufacturing? How do you see Laser Photonics being a part of this evolution?
Today’s DMLS systems have fulfilled the role of fast track prototyping, however, these systems have been confirmed across all market sectors failing to provide the level of parts quality that requires regulatory approval (FDA/FAA) with regards to patient and/or passenger safety prohibiting metal printing companies from moving applications into a production environment. 3D metal AM systems today meet the classical definition of an unstable process based on metal printed parts data that exhibit unit-to-unit variations that do not behave consistently over time or within normal distribution control limits. As a result, these systems are marketed for prototype or proof of concept programs. Metal printed parts are required to achieve MRL10 to meet conditions to move the application into production. The most experienced metal printing companies average MRL4. The main challenges to address in achieving MRL10 relate to Process Reliability (Unstable Process), Inconsistent Quality, Size Limitations, and Metal Printing Speeds.
Fonon Corporation teamed with Laser Photonics Corporation (LPC) in developing next-generation 3D Metal Printing System Patents/IP. Laser Photonics Corporation has successfully demonstrated a prototype system drawing tremendous interest from industry experts. Combining both FTI/LPC Intellectual Property represents the largest portfolio of technologies placing Fonon Corporation in the unique position to manufacture the next-generation of specialized 3D Metal Printing System. Fonon Corporation’s next-generation metal printing systems address common industry applications utilizing the company’s proprietary IP developed for parts quality and optimized for manufacturing purposes.
Laser Photonics’ BTS™ Transformational Technology now opens new doors for space applications onboard space ships or orbiting space stations tooling rocket engine and space craft parts in a deep vacuum environment. Today we focus on designing and manufacturing of application specific systems for Warhead manufacturing, bone structures and knee replacements systems, automotive parts AM systems, and Aerospace turbines and components manufacturing equipment.
Our platforms, laser and mechanical systems, and components are fully developed. We are at negotiation stage with a number of direct users to implement under the contract those application specific AM laser machines for the benefits of our customers. We believe our innovative BTS™ approach in metal printing systems is our best-fit technologies wrapped around the end-user's application and metal type. By using a bottom up approach, we analyze the characteristics of the desired metal powder to establish laser waveform shaping parameters coupled with specific temperature profiles that address the desired metal powder’s behavior during laser processing.
The content & opinions in this article are the author’s and do not necessarily represent the views of ManufacturingTomorrow
Comments (0)
This post does not have any comments. Be the first to leave a comment below.
Featured Product
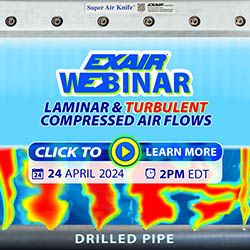