The manufacturing and process industries are reliant on heat transfer. Some ground breaking innovations in and around this sector are helping to improve manufacturing operations, harness natural energy and conserve natural resources.
The Heat Transfer Innovations That Are Changing Manufacturing And Production Processes – 5 Game Changers You Need To Know About!
Chris Wright
The manufacturing and process industries are reliant on heat transfer. Some ground breaking innovations in and around this sector are helping to improve manufacturing operations, harness natural energy and conserve natural resources. This article outlines five things that are changing manufacturing and production processes forever!
Heat transfer is what is says, the transfer of heat from one place to another. Any process where thermal (heat) energy is used will involve heat transfer and it is very commonly used in manufacturing when a constant and predictable heat is required for the production of goods. One everyday example is the processing of foods such as foods like chocolate or oven chips. On an industrial scale such processes are extremely large to achieve a high output volume and this has invariably been down to innovations in current manufacturing. Alongside this there have been some key changes in the heat transfer sector that enable the harvesting of the sun’s energy and converting this into electricity for commercial and domestic purposes. Here I discuss five of the top innovations, summarised in the Table, in the heat transfer sector.
1. Renewable or alternative thermal energy
A brief outline of the technology. This technology enables thermal energy from renewable sources such as wind, tidal, biomass and geothermal. In the case of geothermal the Sun provides a thermal energy source and this regulates the temperature of matter beneath the Earth's surface. Geothermal technology, a renewable energy source, harnesses this energy with peak outputs being achieved during the Summer season. Others technologies use the steam produced from geothermal reservoirs to generate electricity. The largest providers of geothermal energy originate from the western United States of America and produce 3.5 gigawatts of electricity and the power required to fuel 3.5 million homes. Examples include Casa Diablo in California/Nevada, Navy 1 in California, The Geysers in California, Honey Lake in California/Nevada and Imperial Valley in California. [1].
An example of this technology and its advantage. The electricity from geothermal energy has good green credentials alongside being able to provide a continuous, sustainable heat source. The International Energy Agency projects significant growth in this area and states that, “In 2016, global geothermal power generation stood at an estimated 84 TWh, while the cumulative capacity reached just over 13 GW. Global geothermal power capacity is expected to rise to almost 17 GW by 2021, with the biggest capacity additions expected in Indonesia, Turkey, the Philippines and Mexico.” [2].
How does this technology apply to manufacturing and how is it used? This technology is relevant to the current and future generation of electricity which is required in manufacturing, especially in factories that use heat to create final products. In this process electricity is used by heaters to raise the temperature of high temperature fluids and by pumps to circulate the fluid around the system.
What does this technology mean as far as change for the industry? Renewable or alternative sources of thermal energy provide an alternative energy source to fossil-based power solutions and help to reduce the carbon footprint of operations and contribute to target setting to reduce the impact of global warming. From a cost perspective, their use will also help in manufacturing (e.g. the generation of processed foods and baked goods) to decrease the costs of energy production and the cost of manufacturing operations. The International Energy Agency estimates that by 2020, all the renewable power generation technologies that are now in commercial use are expected to fall within the fossil fuel-fired cost range.
2. Harnessing solar thermal energy
A brief outline of the technology. In addition to harnessing energy indirectly from the Earth’s matter it is possible to directly collect the Sun’s energy at the Earth’s surface. Two technologies exist – concentrated solar power (CSP) and concentration photovoltaics (PV).
An example of this technology and its advantage. CSP uses mirrors or lenses to concentrate the Sun’s energy and converting this to heat which in turn drives a steam turbine and drives an electrical power generator. The Dubai Water and Electricity Authority recently announced it has commissioned the World’s largest CSP project, which is within the Mohammed Bin Rashid Al Maktoum Solar Park. The plant is being designed to generate 1,000 megawatts of power by 2020 and 5,000 megawatts by 2030. CSP has the capability to harness the Sun’s energy over a large area; it generates energy from a clean energy source; and, thermal heat can be stored easily, making it possible to produce electricity after sunset. In contrast, PV (also known as solar farms, ranches or parks) uses lenses and curved mirrors to focus sunlight onto small, but highly efficient, multi-junction solar cells (i.e. photovoltaic cells) and through the photovoltaic effect (i.e. a material that creates an electrical current when exposed to light) to convert light energy into electricity. In 2016 the World Energy Council published key findings on solar energy and concluded that there had been exponential growth and at the end of 2015 had reached around 227 GWe, representing 1% of all electricity used globally. [3]. Since 2016, Tengger Desert Solar Park, located in Zhongwei, Ningxia, China, covers an area of 43 km2 and has a peak power output (1,547 MW). The PV technology produces silent and clean electricity (i.e. no air or water pollution is released into the environment) and does not harm animals or humans or deplete natural resources.
CSP has advantages over PV that include: i) higher efficiency; ii) lower investment costs; iii) a thermal storage capacity in which energy can be generated after sunset and when there is cloud cover; and, iv) offers the potential to be combined with other fuel technologies and work as a hybrid operation that can be utilised at night.
How does this technology apply to manufacturing and how is it used? Like renewable or alternative sources of thermal energy, the electricity generated by CSP and PV technologies will be more extensively used to meet the demands of manufacturing.
What does this technology mean as far as change for the industry? All the factors for renewable or alternative source of thermal energy are applicable to CSP and PV. Furthermore, technologies driven by the Sun’s light are still in their infancy, but still their installation costs and the unit cost of this energy continue to decrease. SolarPACES, in their report on CSP projects around the World, show that the industry will see further investment with facilities operational in the USA, Chile, Spain, Morocco, South Africa, MENA, Europe, India, China, Thailand and Australia.
3. High temperature thermal energy storage
A brief outline of the technology. SolarPACES, in an article entitled ‘How CSP’s thermal energy storage works’ [4], state that energy storage is a key to the renewable energy-powered world. Indeed, in the CSP sector solar energy needs to be stored prior to being converted into electricity and this needs to be done over several hours. In the CSP sector, liquids are used for this process. One way is to use molten salts (i.e. melted salt) such as sodium nitrate and potassium nitrate. These salts can be used to store energy or as a heat transfer fluid in CSP power towers and operate to very high temperatures (>700°C). [4]. One further advantage of molten salt thermal energy storage is it has a long-life (at least 30 years), which is remarkable considering the daily demands of storing such high temperature fluids.
An example of this technology and its advantage. In another type of plant, parabolic trough CSP, heat transfer fluids are used that operate to around 400°C. These fluids are based on a eutectic mixture of biphenyl-diphenyl oxide and commercially available fluids include Dowtherm A, Therminol VP-1 and Globaltherm® Omnitech [5] and for many years have been successfully operating the majority of solar energy generating systems (e.g. SEGS VI and ANDASOL). For more information on global CSP projects by name please visit the National Renewable Energy Laboratory website. [6].
How does this technology apply to manufacturing and how is it used? High temperature fluids and salts are used to create electricity. Higher temperature fluids and salts enable more energy to be stored and converted to electricity. Given these technologies depend on the Sun’s heat they are used as an energy store during the day and this can be converted, day or night, into electricity and provides a constant supply of energy that can then be used in manufacturing.
What does this technology mean as far as change for the industry? This technology will see the fluids that can operate at higher and higher temperatures which will enable more energy to be produced at a cheaper price than fossil-fuels. This sector will therefore see investment in more efficient fluids and the energy demands of a greener manufacturing sector.
4. Predictive management of fluids in solar energy plants
A brief outline of the technology. The longevity of molten salts and heat transfer fluids is largely down to maintenance of the operating plant and the fluid itself. Plant insurers require that manufacturers sample the fluids on a routine basis. A general rule this should be conducted quarterly, although this may be less frequently in cases where the fluid is operating ≥20 Celsius below its operating temperature. [7].
An example of this technology and its advantage. Using current technology it is possible to assess the day-to-day condition of the fluid inside the plant and to also sample the fluid whilst in operation. Indeed, Global Heat Transfer offer a package (i.e. thermocare) to plant operators and this can be used to: i) assess the health of a fluid; ii) assess the health of the internal workings of the plant; and, iii) predicts the future health of the fluid and the plant. The big advantage of this approach is that it helps sustain the fluid life and through planned interventions, if needed, avoid costly interruptions to operation.
How does this technology apply to manufacturing and how is it used? This technology is very important for the current and future maintenance of fluids and plants. Heat transfer fluids are used widely across manufacturing and impacts every factory where heat is utilised to produce a final product. The thermocare package offered by Global Heat Transfer, for example, is a lifecycle management plan and is run continuously to assess the condition of a fluid. The objective of this, and other programmes, is to maintain fluids and the internal workings of the factory machinery in good working condition.
What does this technology mean as far as change for the industry? Predictive management of fluids will change the industry as they become more and more accurate in their detection of fluid ageing and breakdown. Hence, fluid maintenance programmes help to preserve heat transfer fluids for long periods of time and the day-to-day cost of doing so helps to extend the operating life of a fluid. This therefore extends the time between fluid replacement, which can be extremely costly and harmful to the environment if not managed correctly. The International Renewable Energy Agency explains that manufacturing process improvements help to reduce material and labour needs, while optimising the utilisation of capital.
5. Reducing water consumption in manufacturing plants
A brief outline of the technology. Almost every manufacturing plant requiring energy and waste heat from machinery needs to be managed effectively. This is commonly done using water as a heat transfer fluid.
An example of this technology and its advantage. Historically, and something rarely used today, water was passed through the machinery or equipment (i.e. single-pass cooling) and hot water was discarded in the sewer. Nowadays, water is recirculated via a cooling pond or cooling tower and evaporative technologies are used to cool the water and remove the waste heat. The cooled water is then available for reuse. Other innovations enable heat waste to be harnessed by using water to generate steam (i.e. heating instead of cooling). [8].
How does this technology apply to manufacturing and how is it used? This technology is used to reduce wasted water, which is a by-product in the manufacturing process.
What does this technology mean as far as change for the industry? Like renewable or alternative sources of thermal energy, this technology can be used to conserve energy usage during manufacture. It also enables manufacturers to reduce their use of clear water and decrease the environmental impact of waste water. Moreover, the recuperation of heat can be used to reduce the energy demands in manufacturing and also to reduce the operating unit cost of energy.
Uses and advantages of the heat transfer innovations.
Heat transfer sector |
Technology |
Example of use |
Advantages |
Renewable or alternative thermal energy |
Geothermal technology |
Steam produced from geothermal reservoirs to generate electricity (e.g. the geothermal power plant in the Imperial Valley, California) |
i) Renewable energy source |
Harnessing solar thermal energy |
i) CSP plants convert the Sun's energy to create steam which is converted to electricity. |
i) CSP: the Mohammed Bin Rashid Al Maktoum Solar Park in Dubai |
CSP |
High temperature thermal energy storage |
CSP thermal energy storage |
i) Molten salts are used as an energy store and for later conversion to steam and then to electricity |
i) Molten salts can be up to very high temperatures (>700 degrees Celsius) |
Predictive management of fluids in solar energy plants |
Fluid maintenance programmes |
Day-to-day assessments of fluid condition |
i) Helps sustain the life-time of a HTF |
Reducing water consumption in manufacturing plants |
Recirculated water and water evaporating technologies |
Removal of waste heat and energy generation from the conversion of water-to-steam-to-electricity |
i) Recycled energy |
Further reading materials
[1] ‘Electricity energy’ published by Office of Energy Efficiency and Renewable Energy. Source: https://www.energy.gov/eere/geothermal/electricity-generation
[2] ‘Geothermal energy’ published by the International Energy Agency. Source: https://www.iea.org/topics/renewables/geothermal/)
[3] ‘World energy resources 2016’ published by the World Energy Council. Source: https://www.worldenergy.org/wp-content/uploads/2017/03/WEResources_Solar_2016.pdf
[4] ‘What are molten salts?’ published on the Molten Salt Energy Technologies web site. Source: http://moltensalt.org/whatIsMoltenSalt.html
[5] Wright CI. Comparing the thermal stability and oxidative state of mineral and biphenyl diphenyl oxide based heat transfer fluids. Journal of Applied Mechanical Engineering 2015: 4; 187. https://doi.org/10.4172/2168-9873.1000187
[6]. ‘Concentrating solar power projects by project name’ published by the National Renewable Energy Laboratory website. Source: https://www.nrel.gov/csp/solarpaces/by_project.cfm
[7]. Wright CI, Picot E, Bembridge T. The relationship between the condition of a mineral-based heat transfer fluid and the frequency that it is sampled and chemically analysed. Applied Thermal Engineering 2015: 75; 918-922. Source: https://doi.org/10.1016/j.applthermaleng.2014.10.024
[8]. ‘Manufacturing Introduction’ published by the Alliance for water efficiency. Source: http://www.allianceforwaterefficiency.org/Manufacturing_Introduction.aspx
About Christopher Wright
Christopher Wright is a research scientist, graduating from the University of Leeds in the UK with a BSc and PhD. His research focuses on the use and maintenance of heat transfer fluids in manufacturing and processing, which includes food, pharmaceutical, specialist chemicals and solar sectors.
The content & opinions in this article are the author’s and do not necessarily represent the views of ManufacturingTomorrow
Comments (0)
This post does not have any comments. Be the first to leave a comment below.
Featured Product
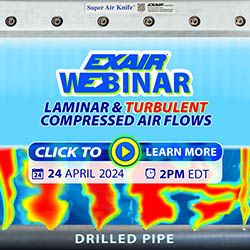