These are the four most common workplace injuries, but they aren't the only ones that can occur. The best thing supervisors and business owners can do to protect their employees from on-the-job injuries is to implement comprehensive safety training and continue it annually
How to Avoid the Top Manufacturing Safety Hazards
Emily Folk | Conservation Folks
Manufacturing is an inherently dangerous industry — in 2017, more than 115,000 reported injuries resulted in days away from work, according to the Bureau of Labor Statistics. How can business owners and supervisors avoid the top manufacturing safety hazards? We'll take a look at OSHA's "Fatal Four," as well as some easy ways to prevent them.
1. Falls
Falls, either from a height or slip-and-fall injuries on ground level, are among the most common causes of workplace injuries and fatalities. They top OSHA's list as the most-violated construction standard.
The easiest way to avoid ground-level fall hazards is to keep up with the housekeeping. Clear the clutter from aisles and walkways, repair leaks promptly and clean up spills immediately. Installing proper lighting, so workers can easily see any obstacles in their path, can reduce the risk of an on-the-job injury.
For elevated fall hazards, fall protection systems should be available to every worker. Offer safety training for each piece of equipment, so everyone who needs to use them knows how. The exact type of fall protection system will vary depending on the needs of the job site, but they should always be available for any employees who will be working off the ground.
2. Struck by Object
OSHA defines struck-by-object injuries as "any injury produced by forcible contact or impact between the injured person and an object or piece of equipment." This definition could be as extreme as a construction worker in the path of a wrecking ball, or as simple as a manufacturing employee struck by pieces of a shattered cutting wheel.
Safety training is the most critical step to take to avoid these accidents in the workplace. For facilities that use large or heavy equipment, reinforce no-go zones — places where employees must not go while the machinery is in operation.
For small equipment, like the cutting wheel we used in the example, the solution is more straightforward — provide the proper safety equipment and enforce its use. Eye protection, hard hats, gloves and other personal protective equipment (PPE) should be available to all necessary employees. You should also maintain it regularly to ensure it is providing the correct level of protection.
This step doesn't stop at struck-by-object injuries. Employees who are controlling machinery or handling hazardous chemicals should also have access to appropriate and well-maintained PPE to avoid on-the-job injuries.
3. Electrocutions
So many pieces of equipment run on electricity that we often take electrical safety for granted. Fatal electrocutions account for roughly 9 percent of workplace fatalities, and most of those deaths are avoidable with improved safety training and providing employees with the appropriate PPE for their position.
Carefully inspect any electrical equipment to ensure there are no exposed wires that could pose an electrocution hazard. If you discover any machine with damaged or fraying insulation, immediately take it off the floor for repairs or replacement.
Make sure employees are following appropriate lockout/tagout procedures when a piece of equipment needs repair, and that you shut off the power to each machine before beginning maintenance or repair work.
4. Caught In/Between
Any manufacturing facility that uses forklifts or other large equipment to move products around is at risk for caught-in or caught-between accidents. These occur when an employee gets trapped, injured or crushed by a large piece of equipment. Forklifts alone are responsible for 85 deaths and 34,900 injuries every year. OSHA states upwards of 70 percent of these accidents are preventable.
The easiest way to avoid this type of workplace hazard is to keep human employees separate from heavy machinery. Designate work zones to keep employees safe, and strictly enforce them. Forklift drivers and other equipment pilots need proper training, as well as periodic refreshers.
Maintaining a Safe Work Environment
These are the four most common workplace injuries, but they aren't the only ones that can occur. The best thing supervisors and business owners can do to protect their employees from on-the-job injuries is to implement comprehensive safety training and continue it annually to ensure it is fresh in everyone's mind.
The content & opinions in this article are the author’s and do not necessarily represent the views of ManufacturingTomorrow
Comments (0)
This post does not have any comments. Be the first to leave a comment below.
Featured Product
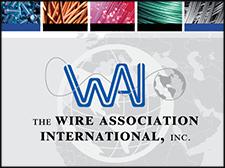