3D printing used to be considered a prototyping tool or novelty, but now that the technology has reached industrial-grade levels, design for additive manufacturing (DFAM) has become a highly-coveted capability
Five Tips to Help You Design for Additive Manufacturing
Dr. Charlie Wood | Fast Radius
Because the technology we use to make and manufacture things is always evolving, designing for manufacturing (DFM) needs to be an ever-evolving skill. A great example of this need is the advancement of additive manufacturing. 3D printing used to be considered a prototyping tool or novelty, but now that the technology has reached industrial-grade levels, design for additive manufacturing (DFAM) has become a highly-coveted capability among engineers and product developers.
You’ve spent years honing your DFM expertise for legacy technologies, so the idea of having to learn new DFAM techniques may seem overwhelming. But with a little creative thinking and a willingness to shift your perception, pivoting your designs for additive production isn’t as hard as you might imagine. Here are five tips to help you adapt your work for DFAM:
1. Start with specs, but don’t be limited by them
It goes without saying that when you’re kicking off a design, you have to start with an understanding of the product specs. Factors like size, end-use, finish, color, and chemical and mechanical properties are important to know whether you’re using DFM or DFAM. Oftentimes, engineers will let a part’s specs pigeonhole their designs into a specific manufacturing process. And while it’s important to know what additive processes are available as you’re planning your design, you should design the best possible product that meets your spec requirements with the confidence that there is enough flexibility with DFAM to meet your needs.
2. Embrace new product designs
When it comes to DFAM, the first rule is: Forget the rules. That’s because additive manufacturing allows you to make parts that were previously deemed “unmakeable.” For example, something that once needed to be made as several separate parts can now be designed as one seamless object. Or, you can design multiple components to be produced in the same build. You can even rethink your entire production schedule, since 3D printing can truncate your design-to-production time by up to 90 percent. Long story short – the sooner you can embrace “out-of-the-box” thinking about what’s possible, the sooner you’ll find success with DFAM.
3. Go farther with design optimization
Because there are so many more possibilities with DFAM, optimization is fundamentally different.
For starters, you’re no longer designing for the overall size and shape; you’re also designing for the open space that’s available when you’re able to remove material from your design. Lightweighting is one of the top benefits of DFAM and a practice you should absolutely consider when you’re looking for design efficiencies and are confident that your product’s strength won’t be compromised. A lot of spare material can be removed by designing with lattice structures – a practice that’s uniquely enabled through additive manufacturing. Not only do they reduce material usage, but lattice structures can also improve product performance.
Lattice structures are often found in nature – and nature is actually a really useful resource when you’re thinking about how to optimize for DFAM. Besides weight, you have to consider optimizing for product toughness, elongation to failure, and potentially high heat transfer. There are so many natural objects that you can draw inspiration from to meet your needs. The structure of skeletal bones or even wood, for example, make great design fodder for parts that need to be tough but also lightweight.
4. Make rapid iteration part of the process
A big bonus to DFAM is that the act of designing entails more than sitting behind a computer screen; it means actually making those designs and seeing, in real-time, whether or not your concept has legs. 3D printing enables you to create, make, test, and iterate your design in a fraction of the time it typically takes to put a concept into production at a fraction of the cost. You’re making the item using the same technology and processes that you will inevitably use to manufacture the final product – enabling you as a designer to learn and adjust quickly. So, don’t be afraid to “fail.” Failures in the additive manufacturing factory are just opportunities to validate your design and make necessary changes.
5. When in doubt – ask an expert
When making the transition from DFM to DFAM, even the very best engineers can benefit from having a sounding board – or even full-on assistance – in designing a product for additive manufacturing. There are plenty of resources you can tap into, but nothing beats a real-life person who can help problem-solve.
About Dr. Charlie Wood
Dr. Charlie Wood is the Computational Engineering Lead at Fast Radius, a leading additive manufacturing company. Fast Radius is recognized as one of the 16 best factories in the world by the World Economic Forum (WEF), implementing “technologies of the Fourth Industrial Revolution.” The companies were selected from 1,000 manufacturers worldwide, with Fast Radius selected as the only award recipient from North America.
The content & opinions in this article are the author’s and do not necessarily represent the views of ManufacturingTomorrow
Comments (0)
This post does not have any comments. Be the first to leave a comment below.
Featured Product
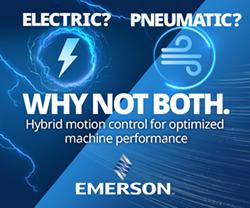