Being prepared can help prevent costly equipment or facility damage. You can't avoid every disaster, but being ready for them when they do occur can help reduce downtime and save you a lot of money on equipment repair and replacement in the long run.
Why Disaster Preparedness Is Important in the Manufacturing Industry
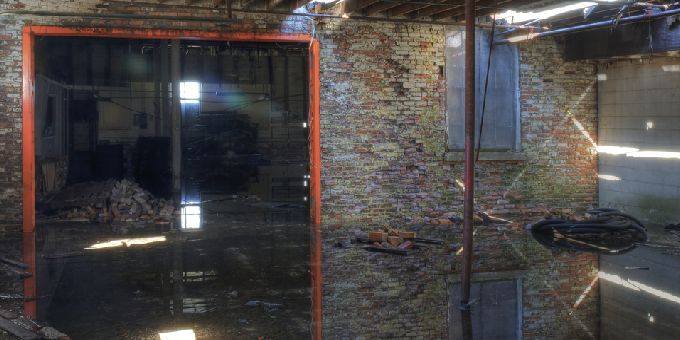
Emily Folk | Conservation Folks
Disasters can happen at any time. Being prepared can make them easier to get through and rebuild afterward, both on a personal and industrial level. Disaster preparedness is vital for manufacturers — perhaps more so than being ready to weather one in your home. Why is it so important, and what can managers and business owners do to help their companies get ready for any disasters that may occur?
Business Risk Analysis
The first step is to look at your business and perform a risk assessment. This will vary depending on where the company is located. Businesses on the West Coast need to be prepared for fires or earthquakes, while on the East Coast they might need to be ready for hurricanes or flooding.
A comprehensive risk assessment is a useful tool because it gives you an idea of the kind of disasters you might have to deal with. It also enables you to prioritize various scenarios. You should determine if you've got time to evacuate or relocate equipment or if you'll have to move quickly to stay ahead of a short-term disaster, such as a fire or a tornado.
Relocating Equipment
If your building is at risk for flooding or you're in a storm-surge area ahead of a hurricane, relocating equipment ahead of time might be your best bet. A risk assessment will come in handy here. What equipment can weather the storm where it is, and what needs to be moved to prevent damage?
If you have time to prepare for a storm, moving your equipment to higher ground is your best option. If you don't have a lot of time to prepare, sandbags or other flood-proofing tech can help protect your investment until the storm passes or the waters recede.
Water Safety
Rising floodwaters might not be your only problem during a disaster. They can cause your local water system to fail or become contaminated. If you use water in your manufacturing, having a water filtration or purification system in place can help keep things working — regardless of the condition of your local water supply.
It is important to note that this only works if the local water supply is still functioning. If it has failed, it might be a good idea to have backup water supplies on hand — both potable water for drinking and nonpotable water for manufacturing.
Backup Power
Often one of the first things to fail during a disaster is the local power grid. Depending on your facility, this could lead to costly downtime while you wait for workers to restore power to your building. Having backup power in place before a disaster could allow you to continue production through a disaster, as long as it is safe for your crew to travel to work.
If you're planning on setting up a series of backup generators, make sure you choose commercial-style generators that can generate enough power to safely run your equipment. Also, make sure you don't plug your generators into the building's main power supply — this can create dangerous feedback that can injure or kill workers who are restoring power.
Be Prepared for Downtime and Recovery
No matter how prepared you are, chances are that during a disaster you will experience some downtime — either because your preparations weren't sufficient or because it is unsafe for your crew to travel to work.
If your facility is subject to a disaster, there is one other thing you will need to consider — disaster recovery. Being prepared can help prevent costly equipment or facility damage. You can't avoid every disaster, but being ready for them when they do occur can help reduce downtime and save you a lot of money on equipment repair and replacement in the long run.
The content & opinions in this article are the author’s and do not necessarily represent the views of ManufacturingTomorrow
Comments (0)
This post does not have any comments. Be the first to leave a comment below.
Featured Product
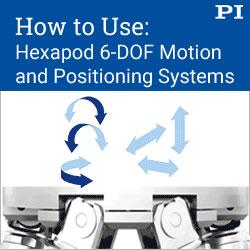