Novarc Technologies Inc. creates robots for spool welding and other custom welding operations. To enhance the operator experience, Novarc turned to COPA-DATAs zenon to create a simple user interface for its robotic welding machines.
zenon helps Novarc Technologies optimize HMI user experience
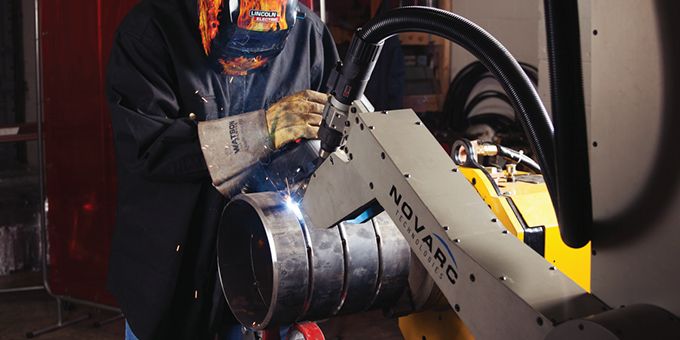
Contributed by | COPA-DATA
Novarc Technologies designs and manufactures pipe welding machines and welding automation technology. The Canadian start-up, based in North Vancouver, British Columbia, was established in 2013 and has attracted substantial investment thanks to its innovative collaborative spool welding robot (SWR).
Designed for high-mix, low-volume production, the SWR improves weld quality and shop floor productivity while providing accurate data for analysis and statistical reporting. The SWR was initially designed without a graphical user interface for its operators but, in 2015, Novarc realized that a simple user interface could improve the SWR user experience.
User-friendly interface with key capabilities
Lead controls engineer at Novarc, Ahmad Ashoori, led the search for a suitable technology to deliver a new user interface. “We did a good search for Human Machine Interface software,” remembers Ahmad, “and the zenon software from COPA-DATA stood out because of its numerous capabilities.”
Although the main driver for the project was to deliver a great-looking and intuitive interface for users, the chosen HMI software would also need to deliver on a number of other key requirements for Novarc. Not only would the software be able to easily create and adapt welding “recipes” and communicate with the PLC of the spool welding robot; it would also need a historian to store, analyze, and report on historical data. In addition, support for engineering applications such as graphing, units, etc., would be a plus.
Smart control and reporting
zenon’s application as an HMI gives SWR operators a great deal of flexibility to set welding parameters. This is an essential requirement for the environment in which SWR is designed, as almost every job requires some level of customization. Now, because zenon has enabled Novarc to preconfigure the SWR with weld recipes, operators are no longer required to have specific programming knowledge to operate the machine. Instead, they can enjoy zenon’s attractive and intuitive user interface.
In addition, zenon has also been deployed on the companion pendant that SWR operators hold during operation; thereby enabling operators to easily make minor changes during welding operations. Through zenon, all operational weld and motion data is captured and recorded. This means that, as well as being able to communicate with the robot while welding, operators can now easily review weld data after the completion of a job – ideal for accurate shop analysis.
The deployment of zenon Historian and zenon Extended Trend has also enabled longer-term statistical and trend reporting. What’s more, thanks to zenon, this data can easily be presented in easy-to-understand graphical form.
Great technical support
Since this was Novarc’s first experience of working with an HMI software, knowing it could rely on an experienced support team was important to Novarc. Ahmad Ashoori reports: “The support team at COPA-DATA USA are great. They were always very responsive and very helpful when we needed any help with the software. The learning curve for our engineers was rapid and painless. For example, tying tags and addresses between zenon and our PLC was so easy.”
This ease of use, together with the attractive graphics the team have readily been able to create, are the best capabilities of zenon, according to Ahmad. “zenon looks and performs great. The recipes were easy to incorporate and both the engineers and the welders like it,” he adds, “zenon has ticked all our boxes for us – and the cost is also very reasonable. I wouldn’t hesitate to recommend zenon to anyone else looking for an HMI, control and reporting solution.”
The content & opinions in this article are the author’s and do not necessarily represent the views of ManufacturingTomorrow
Comments (0)
This post does not have any comments. Be the first to leave a comment below.
Featured Product
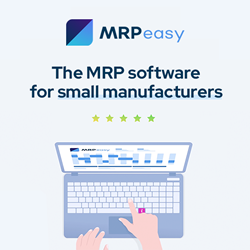