Additive manufacturing or 3D printing is generally considered to be for prototyping but there is an increasing trend towards using it for production. So when does it make sense to switch to or consider using 3D printing for production of your products or parts within them?
Making a Business Case for Switching to Additive Manufacturing
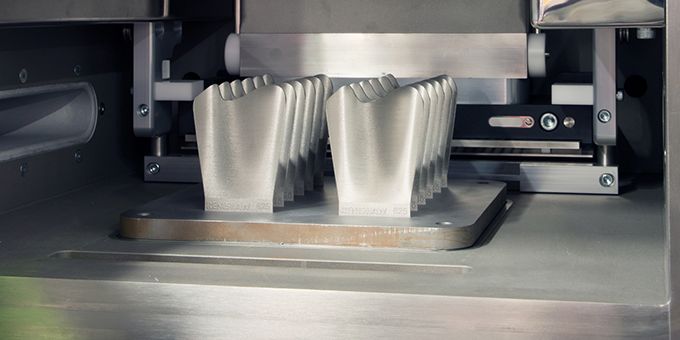
James Murphy | HLH Mold Tech Co Ltd
Additive manufacturing or 3D printing is generally considered to be for prototyping but there is an increasing trend towards using it for production.
So when does it make sense to switch to or consider using 3D printing for production of your products or parts within them?
There are several instances where using 3D printing for production may make sense from a strategic business perspective and also from an engineering one;
- Personalisation
- Low volumes or initial market testing
- Part consolidation
- Weight saving
- Improving part functionality
- Reducing inventory
Personalisation. This is becoming more popular in many fields, and in industries such as medical can actually result in lower costs and better outcomes. Additive manufacturing allows for personalisation of many products due to the lack of investment in fixed tooling. Each part is individually produced whether they are all the same or different. Offering your clients bespoke products via 3D printing could be a useful sales tool or it could be the core of your offering. There are numerous examples of companies whose business model is built around the ability to use 3D printing for manufacture such as http://www.youreyewear.com/ who sell tailor made 3D printed glasses. Recently BMW have announced a number of parts for the MINI cars which can be personalised and then 3D printed.
Low volumes or initial market testing. There are many products where annual volumes do not justify production tooling, or where the market has not been 100% proved and investing massive amounts of money in expensive production tooling may be premature. Under these circumstances it may make sense to consider additive manufacturing as an alternative production method.
Part consolidation. This is where you take a product or assembly with many different parts and use the geometrical freedom 3D printing allows you to combine and reduce the number of parts. Using traditional manufacturing processes, it was often necessary to design a product in many parts just so that it could be manufactured. Additive manufacturing, allows greater though not unbridled freedom to design parts with complex geometries injection molding for example would struggle with. This means you can take an existing design and reduce the number of parts in the assembly saving time and costs and reducing potential issues. Some famous examples include GE’s Turboprop engine redesign, the number of parts dropped from over 800 to 12, and Airbus 3D printing a hydraulic housing tank in one piece instead of its original 126.
Weight saving is another reason to look at 3D printing as a possible production alternative. Products were often constrained by the traditional manufacturing processes and designed to suit the way they were to be made rather than their function and requirements. Additive manufacturing again enables more complex or at least different geometries of parts to be explored and manufactured without problem and so allows you to reduce the weight of many parts by optomising the design for function and removing excessive materials.
Improving part functionality, this is similar to the case stated above where many parts were originally designed to suit traditional manufacturing processes rather than their intended function. Using 3D printing as the manufacturing technique for production can enable you to focus more on the parts intended use and function rather than the method of production. This design freedom can enable you to improve the part functionality.
Reduce inventory. This is a compelling reason to select 3D printing for many instances. An increasing number of manufacturers are choosing to use 3D printing to supply parts to order from old models which may have otherwise ceased production. This frees them from the need to store inventory for part numbers where demand is infrequent, low and random. It also means they do not need to maintain or produce tooling to maintain supply of these parts.
In most instances additive manufacturing is still too expensive to be considered for production but it is increasingly competitive and in the above circumstances may make commercial business sense. As the machines come down in price, the material choices grow and the processes are better used and understood the business argument for ustilising 3D printing will only become more compelling.
The content & opinions in this article are the author’s and do not necessarily represent the views of ManufacturingTomorrow
Comments (0)
This post does not have any comments. Be the first to leave a comment below.
Featured Product
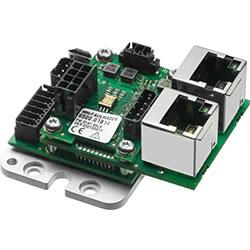