With an increasing demand for vehicle efficiency and efforts to minimize the environmental harm of the automotive industry, the introduction of nanotechnology into the car market is gaining more and more excitement and anticipation.
Applications of Nanotechnology in Car Manufacturing
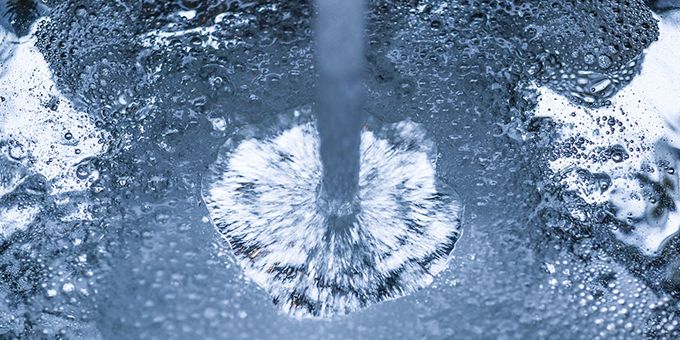
Giles Kirkland
With an increasing demand for vehicle efficiency and efforts to minimize the environmental harm of the automotive industry, the introduction of nanotechnology into the car market is gaining more and more excitement and anticipation.
The Volkswagen Nanospyder is a project of a fully recyclable vehicle created for a world where cars would only have a five year life span to keep up with safety standards. It would use billions of tiny nanomachines that could form the vehicles and then be broken apart, ready for reuse in a new vehicle.
Although this vision is still far from reality, nanotechnology has already become a very real and promising technology to improve cars in the coming years.
Lightweight Metal Replacements
Car manufacturers are constantly seeking ways to decrease the weight of vehicles as a way to increase fuel efficiency. However, they must do this whilst maintaining the overall structural integrity and levels of safety required by government standards.
Many steel elements in vehicles have already been replaced by light weight metal alternatives and plastics. Yet nanotechnology will be able to offer further weight advancements as well as increasing the strength of vehicle parts.
Practically this would be achieved by embedding nanoparticles of metallic carbon nitride into metals as a way to increase the permanent strength of steel.
Scratch and Wear Resistance
Although not yet widely adopted, nanotechnology has been applied in paints and varnishes as a way to protect vehicles from scratches and every day wear and tear.
Nanosized fillers bond with the clearcoat molecules and form a resistant coating that is usually applied over standard car paint. Such coating protects the vehicle from UV damage and offers a hard shield for scratch resistance. Newer technologies are predicted to work as a method for self-healing any damage done to the surface of the vehicle. It is also believed to become dirt resistant.
Anti-Corrosion Performance
Due to health hazards and environmental issues, the employment of electrolytes containing Chrome-VI was banned in 2007. Current alternatives to Chrome-VI offer interior, short term protection. This has created a challenge in the car industry to protect vehicles longer term from the effects of corrosion.
However, nanotechnology offers a solution which is being used successfully for some parts of car doors, chassis and brakes. The technology nullifies the short term issue of Chrome-III by applying Silica (SiO2) nanoparticles in the electrolyte.
This type of technology is likely to increase the lifespan of vehicles significantly and to limit the amount of waste produced throughout a car’s life.
Fuel Cell Technology
Vehicles need increasingly more energy, both in terms on board entertainment and other practical systems as well as the growing popularity of electric vehicles.
The consistent and long term supply of this electricity has proved a challenge in the car industry. Not just in the technological issues with generating required levels of electricity whilst keeping weight down, but also in the cost of producing large fuel cells.
This is primarily due to the need for platinum as a catalyst in the production of traditional batteries. Nanotechnology offers a solution for this, either through the use of nanoparticles of platinum or other metals, there is the possibility to drastically lower the cost of battery production. This is particularly exciting for the development of affordable electric cars through lowering the cost of EV batteries.
Various nanotechnologies also have application in creating thinner membranes in batteries, allowing for lighter and longer lasting cells.
Wear Resistant Tyres
According to the estimates by the World Business Council for Sustainable Development, there are about a billion tyres reaching the end of their life yearly. Such a number of waste tyres generates a significant issue for the environment. Increasing tyre wear resistance is, therefore, becoming crucial to remedy this problem.
One of the elements that can significantly improve the properties of natural rubber is soot. The size and structure of the soot particles as well as cross-linking these with rubber molecules plays a key role in wear resistance. A modified burning process has led to the development of nanostructures soot which can be used to increase the overall wear resistance of tyres.
It is clear that nanotechnology offers a wide range of applications in the auto manufacturing sector. The promising advancements in the lifespan and environmental friendliness of vehicles will be achievable as these new technologies become widely adopted.
The content & opinions in this article are the author’s and do not necessarily represent the views of ManufacturingTomorrow
Comments (0)
This post does not have any comments. Be the first to leave a comment below.
Featured Product
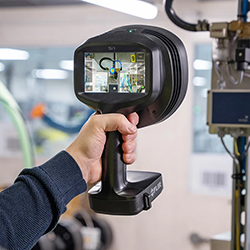