For small-batch series and customized parts, additive technologies offer a drastically faster time-to-market than conventional manufacturing as prior tool-production is not required.
Airbus Gets on Board with 3D Printing
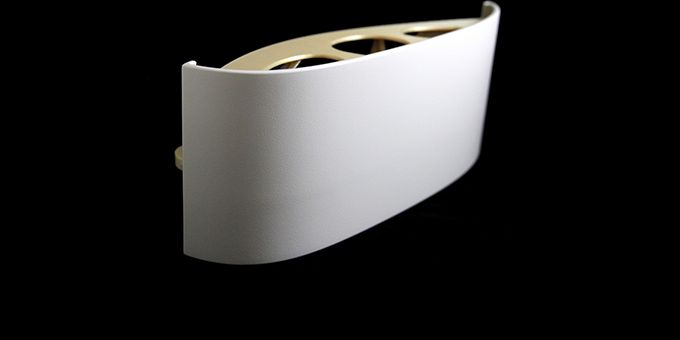
Contributed by | Materialise
When it comes to retrofitting for aircraft, time is of the essence. During cabin retrofits, the integration of newly designed elements might create a need for adapting or redesigning some panels or spacers, which are typically required in low volumes and short timeframes. With tight retrofit timescales to meet, Airbus was looking for a quick and smart solution to produce these spacer panels, and they found it in Materialise’s Certified Additive Manufacturing.
The collaboration between Materialise and Airbus first started two years ago, when Materialise announced the manufacture of 3D-printed plastic parts for Airbus’s A350 XWB. Since then, the collaboration has steadily grown and is today expanding to new programs and services. Among these, Airbus upgrades is at the forefront. Airbus upgrades can benefit from the many of the advantages of 3D Printing such as speed, customization and cost-effectiveness for small batch production while meeting the stringent quality requirements of airworthiness authorities, Airbus, and their final customers.
Today, the partnership between Materialise and Airbus is producing the first 3D-printed parts to be placed in the cabins of Airbus’s commercial aircraft, where they will be visible to passengers: spacer panels located alongside the overhead storage compartments.
3D Printing for Retrofits: Lighter, Faster, Smarter
Direct production with Additive Manufacturing had a crucial benefit for Airbus: the lead time. For small-batch series and customized parts, additive technologies offer a drastically faster time-to-market than conventional manufacturing as prior tool-production is not required.
A spacer panel in production at Materialise using FDM technology
The panels are Airbus’ first cabin parts with full bionic design certification, a successful result of Airbus’ ongoing efforts to optimize part weight. Compared with the original design, intended for conventional production methods, the 3D-printed panels are 15% lighter. In conventional manufacturing, additional complexity would mean higher cost. However, with 3D Printing, complex internal structures like lattices do not create additional cost. Airbus was therefore able to realize lightweight bionic panels and achieve the optimal mass for the component.
Certified Additive Manufacturing and Quality Management in 3D Printing
Fast lead-times, however crucial, are far from being the first requirement. As Materialise quality manager Geert Appeltans puts it, “We can handle incredibly tight lead times, but the foundations for that lie in a carefully honed quality management system. The spacer panels produced for Airbus are more than 3D prints, they’re the output of an entire quality system.”
At Materialise, the quality management system led by Geert is continuously evolving to catch potential problems before they happen, to identify any issues as soon as they do happen, and to trace those issues to their root to prevent their recurrence. The fruit of those labors is in the certifications held by the Materialise Certified Additive Manufacturing facility today — ISO 9001 for manufacturing, ISO 13485 for medical devices, ISO 14001 for environmental management, and the two critical ones for the aerospace industry: EN9100 and EASA 21.G.
“Our goal at Materialise is to be a trusted and reliable supplier in additive manufacturing to Airbus. We do this by innovating together in design and production processes with our software and know-how of AM, but also by seamlessly integrating Airbus’s own way of working,” shares Edouard de Mahieu, Project Manager at Materialise.
Painting and Finishing
The spacer panels are produced by additive manufacturing and then painted to Airbus cabin requirements, all using flame-retardant Airbus-approved materials. Because the panels are visible in the aircraft’s cabin, it is critical for them to meet strict aesthetic requirements as well. In a successful result for Certified Additive Manufacturing and post-production processes, the 3D-printed panels passed all Airbus Cabin Trim and Finish checks.
As Edouard explains it, “We think of this project as a great example of Certified Additive Manufacturing. It demonstrates how Materialise provides an end-to-end process that goes beyond the 3D print. It’s about the strict quality process and incorporating every detail of the requirements from design to finishing.”
For Airbus upgrades, the project showcases the flexibility and lead-time that they can offer to airlines with the support of Additive Manufacturing.
With this project, Additive Manufacturing in the aeronautics sector is taking its next step: into the cabin interior.
Painting the spacer panel
The finished, 3D-printed spacer panel, interior view
The content & opinions in this article are the author’s and do not necessarily represent the views of ManufacturingTomorrow
Comments (0)
This post does not have any comments. Be the first to leave a comment below.
Featured Product
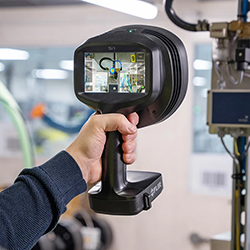