Can you accomplish the same goals with alternatives to conveyor? Possibly – but consider the opportunity cost. Lets explore some common misconceptions about conveyors, as well as some pros and cons of conveyor alternatives.
Can You Complete Your Project Without A Conveyor? The Pros and Cons
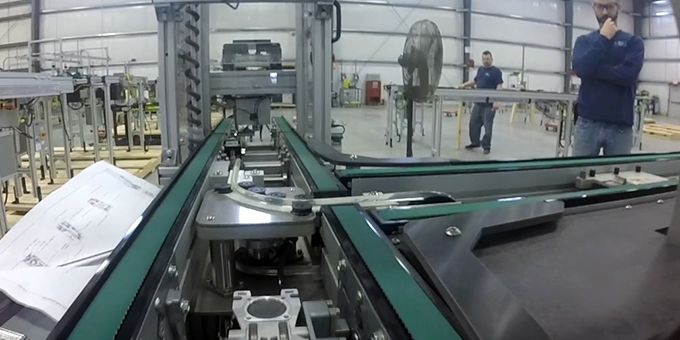
Ron Schwar | Glide-Line
Application engineers are often faced with client-based challenges around the assembly of products, space in a production facility, and lead time. Additionally, application engineers sometimes face design struggles when it comes to options available to accomplish the client’s manufacturing needs.
But can you accomplish the same goals with alternatives to conveyor? Possibly – but consider the opportunity cost. Let’s explore some common misconceptions about conveyors, as well as some pros and cons of conveyor alternatives.
Common Misconceptions about Conveyors
Conveyors are too slow.
In traditional conveyors, this may be the case – particularly if the gearbox ratio is too high. However, in a flexible conveyor design, there are lots of options to not only control the speed of the conveyor and adjust to your client’s throughput goals, but to do it without compromising on product control in the process. Read more in our blog post “Clever Ways to Increase Throughput with Your Conveyor Design.”
We can’t maintain enough control of the products.
This common challenge among precision or fragile product manufacturers is easily addressed by adjusting the belt surface material and making it grippy enough to add control to the moving products. An even more innovative approach is based upon reducing or eliminating the backpressure in a traditional belt conveyor system; this will assist in controlling the product in your client’s process.
The conveyor ride is inconsistent.
Most often, an inconsistent or bumpy ride via a conveyor is caused by built-up pressure from accumulation, also known as backpressure. Applications engineers are forced to either select a conveyor alternative, or upsize the conveyor system to deal with all of the evils of backpressure. However, these solutions use larger-than-necessary parts, cost more money, and use more energy than the right-fit conveyor system. Instead, look for a solution like Glide-Line’s ZP conveyor to solve the problem at its root by eliminating backpressure. Learn more in our white paper on this, How to Manage Backpressure from Accumulation. Download it here.
The conveyor is fairly one dimensional.
Medical supplies such as IV bags and needles, automotive parts like drive shafts, and electronic assemblies with wire bundles require specific solutions where assembled parts are not just accessible from above on a flat surface. This challenge can easily be addressed with the right conveyor solution, such as one with an open center design or an open center lift-and-locate design. Both are members of a flexible belt conveyor group known as Glide-Line 360, which allows for out-of-the-box, configurable solutions.
Alternatives to a Belt Conveyor
Dial Machine Indexer
Dial machines are frequent alternatives to conveyors when applications engineers don’t believe a conveyor can serve the high precision or highly customized needs of their clients. However, this precision solution can lack flexibility and adaptability.
Let’s say your clients wants to upgrade their product offering next year with version 2.0. You’re unable to add anything to the version 2.0 product next year without redesigning the dial machine; your client could be locked in to the current design with limited options to innovate their current product without facing steep cost increases.
Walking Beam Conveyor
A walking beam conveyor faces similar innovation challenges if your client’s product, process, or goals change over time. While a walking beam conveyor offers a high level of product control, there is limited ability to alter the process or product once the conveyor is in place; it could cost a lot of money to upgrade, or it could potentially cost them business if they’re unable to improve their product quickly enough.
Flexible Timing-Belt-Based Conveyors from Glide-Line
Flexible, configurable conveyors from Glide-Line solve the challenges laid out earlier in this post. Particularly when looking at a conveyor system as configurable, adaptable, and flexible as the Glide-Line 360 – where there are virtually limitless options to meet your clients’ needs – this conveyor becomes an alternative in itself because it stands apart from other, traditional belt conveyors.
For example, a company was using our 360 system to manufacture a product. There was a recall, so they needed to add something to the product. To do this, they needed to add a station to the middle of the line. This wouldn’t have been possible without investing a great deal of money on either a dial machine or a walking beam. But, they could do it easily with a configurable belt conveyor.
Product life cycles are not always long enough to justify the time and financial commitments of a dial machine or walking beam conveyor. Processes and products need to change much more quickly and therefore it’s challenging to see the ROI over a short period of time. With any advanced piece of capital equipment, there are a lot of upfront costs; set your client up for success and set their bottom line up for seeing the impact of returns by thinking strategically long-term about your equipment recommendation.
The content & opinions in this article are the author’s and do not necessarily represent the views of ManufacturingTomorrow
Comments (0)
This post does not have any comments. Be the first to leave a comment below.
Featured Product
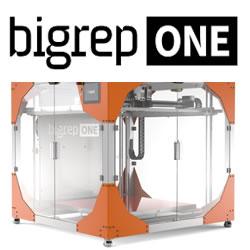