For decades, we have seen jobs in manufacturing disappearing, but now the jobs are beginning to come back, because technology is helping to produce high-quality goods in the U.S. as inexpensively as in Asia.
Len Calderone for | ManufacturingTomorrow
What is smart manufacturing? It is a combination of information, technology and originality, which will change the development of manufacturing in the way products are conceived, sold, manufactured, and shipped. Smart manufacturing will help manufacturers be competitive in the global arena.
Smart manufacturing utilizes big data analytics, in order to improve complex methods and manage supply chains. This is a process of amassing and understanding large data sets. One set is the frequency of data acquisition. Then there is variety, which defines the different types of data that may be acquired. Finally, a manufacturer must analyze the volume of data. Big data analytics lets a manufacturer use smart manufacturing to move from reactionary routines to predictive ones. All of this data helps a manufacturer to improve efficiency and the performance of their product line.
The idea of big data has existed for years. Many manufactuers recognize that if they capture all of the data that comes into their businesses, they can apply analytics and get important value from it. The new advantages of big data analytics are speed and better organization. Not long ago a manufacturer would have assembled information, run analytics and possibly discovered information that could be used in future decisions. Now, insights can be found for instantaneous decisions. This capability to work faster gives manufacturers a competitive advantage that they didn’t previously have.
There are four types of big data analytics that can help manufacturers. The first is prescriptive, which uncovers the actions that should be taken. This analysis results in recommendations for the next moves. Then, there is the predictive, which indicates what might happen. The diagnostic analytics looks at past performance to uncover what happened and why. Finally, the descriptive analytics uses incoming data to extract information, using a real-time dashboard.
Advanced robots, also known as smart machines, are a major part of smart manufacturing. These robots operate autonomously and can communicate directly with the manufacturing systems. These robots can evaluate physical input and differentiate between dissimilar product configurations. These machines can solve problems and make decisions without the assistance of people. They not only can achieve what they were initially programmed to do, but they have artificial intelligence (AI) that allows them to gain knowledge from experience.
These robots have the flexibility to be reconfigured and re-purposed, giving them the capability to react quickly to design changes and innovation, which is an advantage over traditional manufacturing processes. With the advances in robotic cognitive ability, robots can work as cobots to work collaboratively next to people.
Manufacturers can increase integration and data storage by taking advantage of the internet. By making use of cloud software, manufacturers can log on to highly configurable computing resources, allowing servers, networks and other storage applications to be created very quickly.
Open communication between manufacturing devices and networks can be achieved through internet connectivity, which encompasses everything from tablets to machine automation sensors, thus permitting the machines to change their processes based on input from external devices.
Smart manufacturing is projected to grow in the next 3 to 5 years to over $320 billion. The International Federation of Robotics estimates by 2019 the number of operational industrial robots installed in factories will grow to 2.6 million from just 1.6 million in 2015. Since smart manufacturing is not new, the near-term use of new AI technology in manufacturing is likely to look like an evolution rather than a revolution.
In the connected world, the physical world turns into a kind of information system using sensors and actuators embedded in physical objects, which are linked through wired and wireless networks via the Internet Protocol.
In the realm of manufacturing, this stage of industrialization is considered Industry 4.0; where Industry 4.0 involves the technical integration of the Cyber Physical System (CPS) into manufacturing and logistics and the use of the Internet of Things in industrial processes.
CPSs not only network machines with each other, they also create a smart network of machines, properties, ICT systems, smart products and individuals across the entire value chain and the full product lifecycle. Sensors and control elements enable machines to be linked to factories, fleets, networks, and human beings.
The future of manufacturing is flexible. Smart manufacturing allows for many smaller production sites, which will be located closer to the customers, reducing the time from factory to consumer, placing recently developed products into the customer’s hands within hours.
There are some who think that smart manufacturing will require their organization to radically transform their current operations and invest in advanced technology. While some change will be necessary, smart manufacturing actually simplifies the transition by using the existing capabilities that a manufacturer already has.
New software is allowing manufacturers to create and test situations in the virtual world, replicating the design procedure and the production line before an actual product is generated.
3-D printing is a part of Industry 4.0, as it allows for the seamless creation of tangible products using a single machine. 3-D printing gives a manufacturer many possibilities on how a part is designed. As for some products where you would normally need six pieces, 3-D printing can accomplish the same thing in one piece without additional procedures such as welding or screwing.
IoT allows manufacturers to acquire the right information at the right time to make the right decisions. Cloud computing allows companies to obtain and analyze information that affects production. Data from augmented and virtual reality will have a substantial bearing on research and development, giving customers more of what they want, faster while cutting down on costs.
So, what will a smart factory look like? It is a network of connected devices or machines. It is a paperless, ERP, MES, & IoT system that follows the progression from the creative environment down to the manufacturing floor with interconnected and automated processes. It has predictive and prescriptive analytics which drive the detection of awareness, thereby improving productivity on the manufacturing floor. Using the cloud eliminates IT overhead and a pricey infrastructure, while giving manufacturers the ability to access data from anywhere in the world.
For decades, we have seen jobs in manufacturing disappearing, but now the jobs are beginning to come back, because technology is helping to produce high-quality goods in the U.S. as inexpensively as in Asia. Plus, because U.S. manufacturers are closer to the market, goods can be delivered quicker than foreign made goods. Smart manufacturing is certainly making a difference in the return of manufacturing in the U.S.
For additional information:
The content & opinions in this article are the author’s and do not necessarily represent the views of ManufacturingTomorrow
Comments (0)
This post does not have any comments. Be the first to leave a comment below.
Featured Product
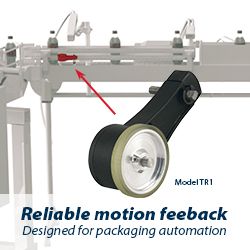