The Smart Manufacturing Report series from SME addresses the necessity and advantages of moving to a smart facility to thrive in an ever-increasingly competitive environment. Update - 2nd Report Now Available
SME Publishes Second of Three Smart Manufacturing Reports to Encourage Adoption of Emerging Technologies
Debbie Holton | SME
Update - The second Report has now been published - sme.org/smartmfg
A smart technology revolution is taking place in manufacturing. While still early, companies are recognizing that operations pain points can be alleviated through technology by embracing smart manufacturing. Smart manufacturing encompasses the tools and processes that allow manufacturers to see and react to the performance of their machines and integrated systems with analytics in real time. It enables machines to talk to one another, control operations remotely, predict challenges and even share live data throughout the supply chain. All of this makes way for improved productivity, increased energy efficiency, higher-quality products, safer plant floors and better employment opportunities.
Why now? Actionable data is changing the game. Sensors, enabled by the Industrial Internet of Things (IIoT), collect information, and cloud-hosted software analyzes it, providing operations managers with intelligence to better manage processes and grow margins. According to The Boston Consulting Group, only three percent of companies are ready for large-scale deployment. However, more than half are already in an experimentation phase.
Fifty percent of organizations are projected to lack sufficient artificial intelligence and data literacy skills to achieve business value by 2020. Adopting these technologies may seem daunting, but it is the only option for manufacturers intent on future growth and innovation. Success by early adopters demonstrates that IIoT technologies add value for facility managers, helping them move beyond data collection to smart manufacturing.
Manufacturers must consider, evaluate and execute strategies to become strong competitors as the industry shifts to integrated and flexible advanced manufacturing technology and tools. The Smart Manufacturing Report series from SME addresses the necessity and advantages of moving to a smart facility to thrive in an ever-increasingly competitive environment. The first of the three reports, “Smart Manufacturing: A Competitive Necessity,” is available now to download. The report discusses the importance and benefits of moving to a smart facility to survive in our current environment. It suggests first steps to embrace this opportunity to disrupt business as usual and drive productivity, quality and profitability. Upcoming reports provide a roadmap for manufacturers who want to adopt these practices, outlining the right technologies and solutions as well as how to recruit and train a “smart” workforce.
Global competition demands companies join this digital transformation or be left behind. Part two of this series will be released on April 30, 2018, the first day of the Smart Manufacturing Experience, an event focusing on how advanced technologies such as additive manufacturing and 3D printing, automation and robotics, advanced materials, precision machining, precision measurement and 3D scanning, digital manufacturing, and the IIoT are revolutionizing the industry.
To download the reports, visit sme.org/smartmfg.
The content & opinions in this article are the author’s and do not necessarily represent the views of ManufacturingTomorrow
Comments (0)
This post does not have any comments. Be the first to leave a comment below.
Featured Product
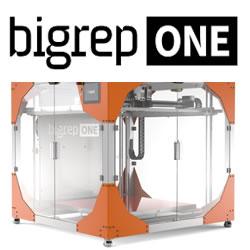