There are three areas where best practices help top-performing manufacturers concentrate their efforts: Production planning and scheduling, Production management, Quality
Top Practices for a Top-Performing Production Floor
Christine Hansen | Epicor Software Corporation
There are three areas where best practices help top-performing manufacturers concentrate their efforts:
-
Production planning and scheduling
-
Production management
-
Quality
Let’s take a closer at look at these areas.
-
Production planning and scheduling
One of the first steps in the production day is to plan what products need to be produced to satisfy existing orders, and to schedule production for them. Top-performing manufacturers concentrate on four practices to maximise production:
Define existing capacity for production. A realistic assessment of production capacity includes factors such as the availability of machine time, the flexibility of the various types of machines for different tasks, and the availability of skilled labour within the organisation.
Improve accuracy of production scheduling. The master method of manufacturing provides a way for companies to continuously refine both manufacturing processes and the time allocated to them. For example, the load time (the amount of time it takes for production) could be stored for each job operation, and recalled to improve scheduling accuracy for future quotations as well as for production.
Use technology to enhance production control. An accurate schedule should be available not only to those in production planning, but also to people on the shop floor who may be actively managing or producing product. An ERP system has these capabilities and is flexible enough to accommodate changes.
Communicate the schedule to all stakeholders in the organization. The availability of schedules online means that anyone connected to the manufacturing process has accurate, up-to-date information to make good production decisions.
A compelling case for cloud deployed Epicor ERP is the ease with which cloud deployment makes key workflows available across the enterprise—and the global supply chain. Because nothing more than an Internet connected PC, tablet, or smart phone is required, cloud deployment is the most effective way to bring accessibility and integration to most organisations.
-
Production management
Another area of focus for top manufacturers is the production management process. Hansen identifies four tasks in the process:
- Execute the production plan according to the schedule established earlier. The process should be the same whether it calls for a single day or a week’s worth of production
- Manage changes in production in a proactive way to minimise the impact of changes on the overall schedule.
- Increase the visibility of the entire production process so that the production schedule, materials management, current production operations, and quality are available to the organisation.
- Close the finished job. Many manufacturers miss this opportunity to implement continuous process improvement. The ability to compare expected costs and labour against actual results is critical to driving the organisation toward more efficient manufacturing processes.
-
Quality
A final area where top-performing manufacturers excel is in maintaining quality throughout the production process. They do this by instilling quality principles throughout the organisation:
- Tracking quality incidents in a systematic way on a regular basis, beginning with the production floor
- Identifying the root cause of a quality problem so that quality issues can be avoided in the future
- Making quality in the production cycle an organisational objective
Get these three areas right, and you will be on the right path to business growth.
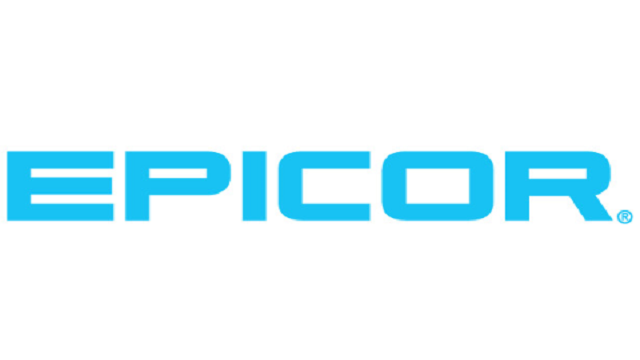
Growth of our customers' business is at the heart of what we do. The strength of Epicor business solutions lies in a simplified approach to technology, inspired by our customers and how they work. More than 40 years of experience with our customers’ unique processes and operational requirements is built into every solution. We provide flexible, industry-specific software that is designed around the precise needs of our manufacturing, distribution, retail, and service industry customers.
The content & opinions in this article are the author’s and do not necessarily represent the views of ManufacturingTomorrow
Comments (0)
This post does not have any comments. Be the first to leave a comment below.
Featured Product
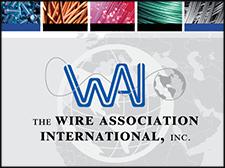