Pneumatics has had different diagnostic features for some time. For example, we can sense today whether the power is too low or too high, or whether there is a short circuit in an I/O system which caused some sort of failure.
Pneumatics and the Internet of Things: What's Holding Us Back?
Mark Densley | AVENTICS Corporation
We’ve all heard the hype about the Internet of Things (IoT) and its revolutionary impact on manufacturing. But, unfortunately, the adoption of IoT technology isn’t happening as rapidly as the concept’s supporters predicted.
What is holding us back from seeing a broader embrace of IoT, especially in pneumatics?
For end-users responsible for maintaining machines and keeping them running, the path is very clear. You can have an IoT system provide data from the machine, and ensure that the systems or the components on that machine are working within their normal range. In that regard, the end-users are the ones pushing for IoT implementation.
The disconnect is often with machine builders. They may have multiple customers pushing them for IoT solutions, so OEMs are asking, “How do you do implement that? Who has the product to do that? And what should we be monitoring?”
Pneumatics has had different diagnostic features for some time. For example, we can sense today whether the power is too low or too high, or whether there is a short circuit in an I/O system which caused some sort of failure. And now we are taking it a step further with sensors and the ability to use I/O systems to look at the things that are driving the actuators. The aspect that people are struggling with is, “I have all this data, but what does it mean? How do we turn that data into useful information?” That’s the big stumbling block today.
Now, the focus is on what you can do with that data to convert it into useful information and react to, or even predict failure. For example, the AVENTICS ST4-2P programmable sensor has been in our product line for years. It measures travel distance and velocity for pneumatic cylinders. We can sense the velocity of the piston in the cylinder. But we can also use that data coming back from the sensors to monitor the cushions and shock absorbers inside the cylinder, to ensure they are performing within a certain specification window. If you interpolate that data, you can come up with a way to ensure the cylinder is performing as expected, and quickly determine when it is not.
With a gateway like the AVENTICS Smart Pneumatics Monitor, local data collection and pre-installed analysis modules allow analysis independent of the controller.
You can see the data today in the PLC and, with a gateway like the AVENTICS Smart Pneumatics Monitor, you can analyze the data to create usable information to figure out what is going on with the machine.
Let’s look at energy consumption, for example. You can measure the air pressure going into the system. You can measure the flow and correlate that to an event and conclude that when you turn on a given valve you get a certain flow, which means if that flow deviates the next time the valve comes on, there must be something wrong with the system. Maybe the tube has come out or maybe the seals are wearing in the cylinder. You know something is off, but what you do with that information and how you use it is the differentiator as machine builders seek to implement ways to leverage IoT capabilities.
Both the OEM and the component manufacturer have the responsibility to address problems that are uncovered from the data. Our IoT approach is not “IoT in a Box.” There is some consultative nature to it. OEMs and end-users typically would like to have some additional monitoring to make sure that their machine processes are being controlled correctly. We can work with the OEM to come up with an IoT architecture to make sure that the appropriate sensors are in place and are sensing the right things to help keep that machine running full-time.
One vision for the use of IoT and pneumatics is to use the appropriate data to enable a highly autonomous maintenance process where the pneumatic circuit, or ultimately the machine, has 100 percent uptime and never fails.
The important thing is that the component manufacturers outfitting the machine need to talk to one another and understand how the pneumatics come into play, so there can be a true partnership when talking to customers about IoT. When you get down to the field level, you are going to have pneumatics, drives, controllers and I/O systems. The key is knowing how the data is passing between those items and making sure that the data gets to wherever it needs to go, whether that is locally on a web server, or out to a cloud system.
Going back to the energy consumption example: the best way to realize energy savings is to turn off the compressor. It sounds very simple. Although AVENTICS may not make compressors and we don't make control systems for compressors, with smart pneumatics we can tell the compressor control system what the demand for air is over the next 12 hours. And from that, the controls can turn off the compressor accordingly, because it may not need all that air. That is just one example of components and systems “talking” to each other to affect energy savings.
Customers are slowly starting to get familiar with the concept of a higher level of analysis and data sharing. More importantly, it depends on who you are speaking with in the machine design process. In the past, when we worked with machine designers we discussed things like power and the air connection. Now the discussion needs to involve factors such as network connections, security and VPN connections.
Component manufacturers like AVENTICS can work with OEMs to come up with an IoT architecture to make sure that appropriate sensors are in place and are sensing the right things to help keep a machine running full-time.
It is more important than ever to include the IT department in the design architecture and discuss what those connections look like and how the data is moving. The security issues are important also, especially to end-users, so you need to involve IT experts early in the design to understand what the data is, how much data, where the data is going and how it is going to connect. There wasn’t a need to do that in the past.
How will all these things work together to improve the situation for a manufacturer? One vision is to enable a highly autonomous maintenance process. To us that means the pneumatic circuit, or ultimately the machine, has 100 percent uptime and never fails. Obviously, components wear out; valves and cylinders go through their specified life cycles and need to be replaced. But, the data is there to predict failure before it happens, so that is where predictive maintenance comes in.
For example, one application is predicting the performance degradation of things like pneumatic valves. Based on a life cycle benchmark and B10 life cycle credits, we can use the data to track when a given valve will reach 75 million cycles and need to be replaced. The operator can receive a message about predictive failure and replace the valve before production is disrupted.
Using data from sensors, we can also predict when a shock absorber on the end of the actuator is deteriorating by sensing an increase in the cycle speed, even by a few milliseconds. This would trigger an alarm or even send an automatic email to the component supplier that maintenance needs to be completed or that the component is ready to be replaced. The system could even generate an order and a new component would be automatically shipped to the customer, so the installation could be scheduled to minimize any production downtime.
The end goal is to use data to provide information to ensure that machines never fail; that they are self-diagnosing; and that end-users know what is occurring and the machine just keeps on working.
The content & opinions in this article are the author’s and do not necessarily represent the views of ManufacturingTomorrow
Comments (0)
This post does not have any comments. Be the first to leave a comment below.
Featured Product
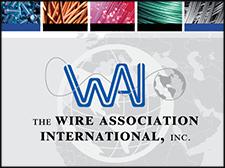