At the cutting edge of this trend are new types of human-machine interactions, such as virtual reality, next-generation design tools, 3-D printing, and collaborative robots. As these complementary technologies begin to link multiple factories with designers, supply-chain partners, distributors, and customers, the sector can form more dynamic digital networks and turn around the trend of slowing productivity growth.
Making it in America: Revitalizing US Manufacturing.
Sree Ramaswamy | McKinsey Global Institute
Please tell us about the McKinsey Global Institute
The McKinsey Global Institute is the business and economics research arm of McKinsey & Company. This latest report on the US manufacturing sector builds on a multiyear body of work MGI exploring the US economy, the future of global manufacturing, productivity, competitiveness, digital technologies, and the future of work.
Tell me a little bit about this report - Making it in America: Revitalizing US manufacturing. What are the big findings?
We combined top-down economic data with bottom-up financial data from companies and with industry-specific insights from our manufacturing experts across a range of industries. This helped us get a better perspective on the many contradictory stories that persist in the manufacturing sector. It also helped us zero in on just how much opportunity there is for growth and what the United States would need to do in order to capture it.
We found that this is really a story of two different manufacturing sectors--and their trajectories are pulling further apart. A handful of industries (notably pharma, high tech, aerospace) are driving most of the output growth. In most others (like metals and machinery, plastics and chemicals), real output is lower today than it was 10 or even 20 years ago. There is also a divergence in terms of companies. The very largest firms, with annual sales of $5-$6 billion or more, have done extremely well in sales growth, profit margin, and returns to capital. But small and mid-sized firms have seen negative growth for 2 decades. They have taken the brunt of the pain in the sector. This is a major problem since they make up most of the sector’s establishments and employment. Their struggles have left them unable to invest in new equipment and technologies that would boost productivity. And as many small firms have shut down, even the largest firms have become more exposed to global supply chain risk and more limited in their choice of domestic partners for innovation, collaboration, and speeding new products to market.
We also found the decline of the US industrial base has been the biggest factor contributing to the squeeze on the US middle class, driving two-thirds of the recent decline in labor’s share of US GDP, and hollowed out growth prospects for middle-income households. It has left large firms
This report outlines a lot of what occurred in US manufacturing to get to this point, how does the industry turn it around?
Our report finds that the United States could raise manufacturing output by nearly 20% over the next decade and add more than 2 million manufacturing jobs in the process. We get there largely by building on our strengths—and there are a lot of them to draw on. The US is still the world's 2nd-largest manufacturing nation, with an unmatched diversity of industries.
There is massive market growth to tap, especially as the middle class continues to grow in emerging markets around the world, and companies can harness a wealth of data to create new business models and new sources of revenue. But markets are fragmenting rapidly and requiring rapid response, so firms need to become much more agile and productive to compete in this new environment. That’s where Industry 4.0 technologies can come in. This new and more digital form of manufacturing is not necessarily going to generate tens of millions of old-school assembly-line jobs. But it can create some productive and hopefully higher-paying jobs.
To get there, we need to rebuild capabilities in the domestic supplier base, make serious investments in plant and equipment upgrades, help small and midsize firms access new technologies, and expand apprenticeship programs that promote new skills and labor mobility. There are lots of isolated initiatives under way to address these issues. But the United States needs scale, coordination, and long-term investment to really move the needle. We're talking $110 billion a year for capital upgrades, $40 billion a year for apprenticeships. This is beyond any individual firm or local government to manage. It will take industry-wide efforts and public-private cooperation.
Who has the most to gain? What partners are necessary to make this so?
The biggest opportunities are in advanced manufacturing industries in which the United States should have a competitive advantage but instead runs a large trade deficit.
Another big priority is the domestic supplier base. One piece of this involves the largest US manufacturers forming deeper and genuinely two-way partnerships with key suppliers. But it’s bigger than that. The United States needs to shore up small and midsize suppliers across entire industries. It’s critical to get investment, know-how, lean principles, digital readiness, and new workforce skills percolating throughout the supplier base. Policy can help through measures like capital access programs, business accelerators, or tax incentives. Just 1 percent of US firms actually export—a much smaller share than in other advanced economies—so it is also crucial to provide smaller firms with export assistance and awareness of overseas market opportunities.
How do we, from region to region, use existing infrastructure to help take advantage of the opportunities in this report?
Any effort to revitalize manufacturing in a specific region needs to start with an analysis of that region’s core industries, their future growth prospects, and where they might overlap or complement other types of related industries. It’s important to take a realistic inventory of existing assets (say, logistics, available industrial space, educational institutions, and the level of local workforce skills). Once a community decides to build a future around certain industries, the next step is considering what kind of investment it will take—and that investment doesn’t have to come from within the United States. Going after certain manufacturing industries may require developing new types of workforce skills, forming R&D and training partnerships with local educational institutions, and expanding logistics infrastructure.
How big a role will Robotics, Automation and the Industrial Internet of Things (IIoT) play in the growth of the industry?
Industry 4.0 technologies could provide the key to ramping up productivity growth and agility.
At the cutting edge of this trend are new types of human-machine interactions, such as virtual reality, next-generation design tools, 3-D printing, and collaborative robots. As these complementary technologies begin to link multiple factories with designers, supply-chain partners, distributors, and customers, the sector can form more dynamic digital networks and turn around the trend of slowing productivity growth. This last point is crucial for manufacturing firms that have already maximized what they can do with cost-cutting approaches.
When can we start to see all this—and by “this” I mean innovative manufacturing practices—come to life?
Some early adopters are already turning their factory floors into information networks and using digital systems to make instant, autonomous adjustments that maximize output and minimize downtime. But so far most of the digital leaders are the large multinationals. The key will be getting these new technologies and best practices percolating through the wider base of small and midsize firms.
US manufacturing could be back on a growth trajectory within the next few years. If the United States take full advantage of all these trends—shifts in demand, new technologies, opportunities in new parts of the value chain, and shifting factor costs—we believe that by 2025, the United States could boost manufacturing output by 20 percent.
About Sree Ramaswamy
Sree Ramaswamy is a Partner at the McKinsey Global Institute (MGI), McKinsey’s business and economics research arm. He leads research on the economics of digitization and the economics of multinational corporations. He is responsible for shaping MGI’s research initiatives, leading research on trends in competition, technology, and global forces influencing multinationals.
The content & opinions in this article are the author’s and do not necessarily represent the views of ManufacturingTomorrow
Comments (0)
This post does not have any comments. Be the first to leave a comment below.
Featured Product
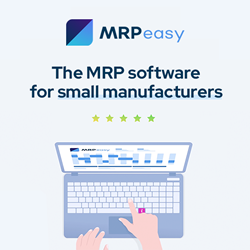