Although some manufacturing leaders and their employees are hesitant to embrace new technology and hardware on the job site, these innovations are here to stay. Those who adapt to these new standards sooner rather than later will be ready to tackle Industry 4.0 and reap all the benefits it has to offer.
4 Process Trends Changing Manufacturing
Kayla Matthews | Productivity Bytes
Manufacturing is a vital part of the United States’ economic success. Although industry numbers have dwindled since the turn of the century, our country still employs more than 12 million workers in the manufacturing sector. However, those employees might be in the midst of the next industrial revolution.
Image by Pixabay
Four major process trends are emerging in the manufacturing industry.
1. Increased Automation
Factory automation is getting a huge push from advanced technology like industrial robotics. Although some attribute the loss of manufacturing jobs to these automated systems, many of them are creating brand new opportunities for human workers in the industry. According to recent studies, there are currently 2 million open jobs in the manufacturing sector, many of which are a result of increased automation on the factory floor.
The current generation of robots might be able to perform assembly tasks and manufacture parts, but they’re unable to solve complex problems or bottlenecks. Humans will always be needed in the manufacturing industry to monitor production and assembly lines, verify quality and communicate with partners, suppliers and customers.
2. The Internet of Things
Another innovation that’s taking the manufacturing industry by storm is the Internet of Things or, in this case, the Industrial Internet of Things. Sometimes referred to as Industry 4.0, the IoT is am extensive network of interconnected machines, robots and sensors.
The benefits of IoT are too great to ignore. Real-time monitoring of parts and pieces lets you track the physical location and condition of assembly components and finished goods alike. Self-diagnosing machines can shut themselves down before suffering significant damage. In some cases, these devices can even initiate repairs without human intervention.
Like with robotics, some manufacturers believe the increased technology of the IoT will reduce the number of opportunities for human workers. But recent studies, which take into account the impact of technology ever since the 1800s, indicate that greater access to technology leads to more jobs in the long run.
3. New Factory Hardware
Factory upgrades aren’t limited to advanced robotics and machinery. We also see the proliferation of brand-new hardware within shops all across the country. Advancements like energy-efficient lighting and eco-friendly storage bins are helping manufacturers embrace sustainability in the workplace.
Conveyor belts are also receiving an upgrade. Although many shops and factories rely on conventional, plied conveyor belts, new materials provide better performance and less down time than traditional belts.
4. On-Demand Parts Printing
Breakthroughs in 3D printing have paved the way for on-demand parts printing. While many of these parts are currently used for prototyping purposes, advancements in technology could make on-demand parts printing a reality for manufacturers across the country.
The concept is simple: Instead of using regional warehouses or third-party companies to manufacture and provide small parts and components, manufacturers can create these pieces in-house via 3D printing. Not only does this eliminate any delivery time from the equation, but it also results in lower overhead costs on behalf of the manufacturer.
Some experts believe 3D printing will see an increasing use in the production and creation of finished goods. While most 3D printers are limited in size and scope, some machines are already capable of reaching this level of functionality.
Embracing the Change
Although some manufacturing leaders and their employees are hesitant to embrace new technology and hardware on the job site, these innovations are here to stay. Those who adapt to these new standards sooner rather than later will be ready to tackle Industry 4.0 and reap all the benefits it has to offer.
The content & opinions in this article are the author’s and do not necessarily represent the views of ManufacturingTomorrow
Comments (0)
This post does not have any comments. Be the first to leave a comment below.
Featured Product
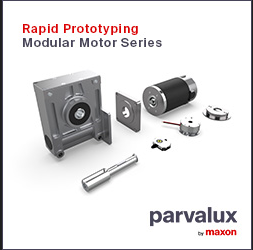