Connected Manufacturing is the ability to drive data that is meaningful to the cloud for big data analysis. The current trend in Industry 4.0 is to be able to sense specific points in end equipment to enable advanced analytics to be run on distributed edge computing devices to determine whether machines are operating within tolerances and predict a potential failure before it happens.
Talking Industry 4.0 with Mark Kojak, HARTING, Inc.
Mark Kojak | HARTING, Inc.
Are you familiar with the term Industry 4.0 and if so what does it mean to you and your company?
Yes, we are familiar with the term Industry 4.0. Industry 4.0 is the next phase of digitization of the manufacturing sector that is driven by the need for advanced analytics to give way for predictive and preventative maintenance, higher end equipment efficiencies as well as lower power consumption. HARTING is leading the charge to Industry 4.0 by giving our customers the ability to connect both legacy and newly designed equipment, utilizing an advanced industrial gateway called the MICA, which stands for Modular Industry Computing Architecture. We are also enabling our customers to use advanced sensing modules as well as protection and ethernet switches within the connector itself for ease of design and deployment.
How is your company set to benefit from the buzz about the factory of the future?
As stated above, HARTING is at the forefront in anticipating what our customers will need in order to move their products into the digital age. We are reinventing what a connectivity company is and developing solutions that are easy to use, highly integrated and robust for the demanding needs of an industrial environment.
What applications of the Internet of Things (IoT) are you or do you plan to implement in the near future?
HARTING is pushing what is possible for connectivity. We are focusing on miniaturization and high performance to align with the small form factor end products that is the current trend in Industry 4.0. HARTING is also continuing to drive sensor technology, as well as cloud connected solutions to enable distributed control and computing.
How do you interpret the term “Connected Manufacturing”?
Connected Manufacturing is the ability to drive data that is meaningful to the cloud for big data analysis. The current trend in Industry 4.0 is to be able to sense specific points in end equipment to enable advanced analytics to be run on distributed edge computing devices to determine whether machines are operating within tolerances and predict a potential failure before it happens, as well as monitor power consumption and efficiencies.
Do you think Industry 4.0 will bring more (but different) jobs to the industry or will it result in a large loss of employment?
I believe that Industry 4.0 will bring about more but different jobs to the industry. End customers are starting to look at deploying services that are aimed at servicing machines that are being monitored for continuous up-time. Customers can look at new revenue streams by offering services where either their own equipment is monitored or possibly other company’s products are monitored by retrofitting a monitoring system.
Can you give us some examples or scenarios that help to convey the benefits of Industry 4.0 to others in your industry?
Industry 4.0 is enabling customers to keep their factories down time to a minimum. Customers can use the MICA to monitor current draw on a motor and run analytics to identify when a motor’s bearings may start to fail due to increased current draw from nominal. This information is sent to the cloud for inspection and quick decisions can be made to service a failing product during a scheduled down time, rather than an unexpected one.
How about scenarios to convince the general public that Industry 4.0 is a good thing for their future?
The cost of goods should go down as a result of lower cost manufacturing. Industry 4.0 will allow manufacturers to save money by using less power, driving higher efficiencies in their machines and drive their capital expenditures down due to the increased ability to detect issues before they become catastrophic, which will allow maintenance rather than replacement.
Tell us a little bit about some of your plans and projected roadblocks specifically related to the US Manufacturing market and moving towards a smarter factory.
HARTING is anticipating the market needs by offering rugged, high performing solutions for Industry 4.0. The MICA is an edge computing device that allows for equipment both legacy and latest generation to connect to the cloud. HARTING is also redefining what a connectivity company is, by actually integrating active components into the connectors themselves. Our customers can create a custom sensing or communication solution by using off the shelf modules in order for them to create a compete cloud connected solution within our industrial standardized Han connectors.
The content & opinions in this article are the author’s and do not necessarily represent the views of ManufacturingTomorrow
Comments (0)
This post does not have any comments. Be the first to leave a comment below.
Featured Product
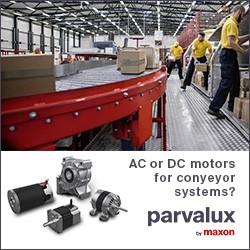