As automated production kicks in and increases the quantity of finished products, has the manufacturer considered the just in time inventory requirement changes necessary to meet production deadlines?
Modernize Your Supply Chain
Len Calderone for | ManufacturingTomorrow
Many manufacturers are upgrading their manufacturing equipment, such as robots and intelligent software. These changes hopefully will increase production, but how will such changes effect sourcing and distribution? Can the manufacturer get sufficient raw materials in time and can the finished product get out of the door and to the customer as promised?
As automated production kicks in and increases the quantity of finished products, has the manufacturer considered the just in time inventory requirement changes necessary to meet production deadlines? What about the other end of the cycle? Can freight and distribution resources keep up with outgoing shipments?
Manufacturers need to have flexible sourcing and a sophisticated logistics network to support those channels effectively. One of the major inhibitors to supply flexibility is the IT systems that support the supply chain, as unintegrated supply chain applications make it problematic to take advantage of new opportunities.
Just-in-time (JIT) is an inventory strategy manufacturers employ to increase efficiency and decrease waste by receiving parts only as they are needed in the production process, thereby reducing inventory costs. JIT requires manufacturers to forecast requirements accurately.
JIT inventory has several advantages over traditional warehousing of parts. Production runs are short, which means that manufacturers can move from one type of product to another effortlessly. JIT reduces costs by eliminating warehouse storage requirements. Less money is spent on raw materials and parts because just enough is purchased to make the ordered products and no more.
As with any supply model, there is a chance that problems could occur. If a supplier of raw materials or parts cannot deliver the goods on time, one supplier can close-down the entire production operation; or if there is a sudden order for product that surpasses expectations, delivery of finished products might be delayed.
Do it right the first time (DRIFT) is a theory that relates to JIT inventory and production management. The idea behind DRIFT is that management wants the processes that make up the JIT thinking to be done correctly and efficiently so there are no delays in the production process.
Looking at raw materials replenishment, there is an area where the IoT and access to real-time information could really help manufacturers control raw or parts inventory by better mobilizing their workforce and improving communication.
A manufacturer that notices fluctuations in product demand can adjust production, enabling the manufacturer to determine how much raw material is needed; and when utilizing IoT, this data is shared with suppliers via the cloud, enabling the supplier to start restocking proactively with the goal of keeping inventory at pre-approved levels. When the suppliers run into unexpected problems, this kind of visibility can enable their manufacturing customers to change plans quickly.
Big data is becoming more important to the entire manufacturing process. It is a term that describes the large volume of data that inundates a manufacturer on a day-to-day basis. It’s not the amount of data that’s important; but what a manufacturer does with the data that matters. Big data can be analyzed for insights that lead to better decisions and strategic business moves.
The amount of data that’s being created and stored on a global level is almost inconceivable, and it just keeps growing, allowing manufacturing management to garner key knowledge from business information in order to direct production and notify the suppliers of raw material and parts needed for changes in production.
To reduce costs and increase revenue, it is important to design and manage economical and effective supply chains. In today’s competitive environment, it is a matter of survival.
When working up a model for supply chain and logistics optimization, many logistics managers accept that there is no unpredictability or that using average values are adequate. Yet, inconsistencies occur in practically all supply chain and logistics procedures. This incorrect conjecture often leads to errors in model outcomes and results in mediocre decisions. Ignoring variability is a sure path to failure. Therefore, variability must be considered in the supply line models.
Supplier disruptions are a reality for most shippers. In fact, 75 percent of supply chain professionals responding to a recent AMR Research poll indicated that at least 10 percent of their supply partners had experienced a disruption in the past year.
Supply chain and logistics optimization requires constant effort, because there is always going to be change in logistics problems, thereby requiring regular monitoring of data, models and algorithm performance. It is important to initiate processes to support and constantly improve logistics optimization. Otherwise, the optimization technology will be poorly utilized.
Manufacturers with a digital supply chain can better move resources, assets, people and inventory to where they are needed at any given time in order to reduce costs. The payoffs of a fully executed digital supply chain include savings in every area, including resources, time, and money.
Technologies such as GPS tracking, radio frequency identification (RFID), barcodes, smart labels, location-based data and wireless sensor networks all play a part in a digital supply chain. In addition, cloud technologies integrated with Web services can unify information and processes to create trading-partner visibility and more efficient collaboration.
There are four well-defined benefits to a cloud-enabled digital supply network:
-
Connectivity provides unique visibility and the real-time ability to influence decisions, resulting in an intelligent supply network.
-
Once the supply network is connected, analytics, cognitive equipment and smart apps provide the right information for decision making at the right time.
-
Once the network is connected and intelligent, the supply network can scale. A manufacturer can manage partners and suppliers as needed, scale down its operations to hone in on specialty markets, and pursue additional markets.
-
With the first three advantages in place, a manufacturer can operate its supply chain network with speed, successfully executing in the middle of constant instability.
Cloud computing is recognized as a real game-changer, providing a path through which supply chain executives can rapidly and effectively access state-of-the-art solutions and execute them at scale.
Manufacturers can now have unprecedented efficiency by modernizing their supply lines by using the latest technology, which is changing the way raw materials and parts are sourced and moved.
Len Calderone - Contributing EditorLen contributes to this publication on a regular basis. Past articles can be found with an Article Search and his profile on our Associates Page He also writes short stores that always have a surprise ending. These can be found at http://www.smashwords.com/profile/view/Megalen.
|
![]() |
The content & opinions in this article are the author’s and do not necessarily represent the views of ManufacturingTomorrow
Comments (0)
This post does not have any comments. Be the first to leave a comment below.
Featured Product
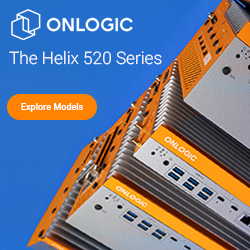