Unsupervised Machine Learning is much more cost effective than Supervised Machine Learning because the algorithm does not need blueprints or understanding of the physical process to “learn” the behavior of the asset.
Machine Learning for Asset Maintenance
Eitan Vesely | Presenso
Please tell us a bit about Presenso, who you are and what you do?
My name is Eitan Vesely and I am the CEO of Presenso. I’m a Mechanical Engineer by training and worked for Applied Materials and later as an industrial automation and process control engineer. Prior to Presenso, I spent a number of years supporting and fixing machines in production lines and developing integrated industrial control systems.
Presenso is not as well known in the US as it is in Europe, so I assume that your audience may not be familiar with our solution. Presenso is a pioneer in the application of Artificial
Intelligence for predictive asset management. Advanced Deep learning and Machine Learning algorithms analyze assets sensor behavior and automatically detect abnormalities and patterns within them. Facility technicians are alerted in real time to potential breakdown, thereby giving them advance notice to remediate the problem.
Presenso continuously streams asset sensor data to the cloud where Artificial Intelligence algorithms analyze it in real time. It is sensor agnostic and monitors all signal data without the need for manually setting control limits or any other human input.
After the detection of anomalies in all the asset’s signals, correlations and pattern detections between signals are performed in order to later present the operators with the exact sequence of abnormal events detected.
Once an evolving failure has been detected, a failure alert is generated. This alert includes information on correlated sensor abnormalities. This valuable information significantly helps in tracking the failure origin.
Where did you get the initial idea to launch the company?
I was working at Applied Materials as a hardware specialist and systems support engineer. There were times where I would come to work in the morning with my passport in hand, and by afternoon I would be on a flight to Singapore, Germany or the US. It was always for the same reason: troubleshoot a hardware failure in a manufacturing plant that has led to machine shutdown.
My first task as a support engineer was to review the historic data in an effort to identify the root cause of the malfunction. As you know, machines generate terabytes of data but most of it is not used. Data is simply stored and accessed when something goes wrong. At the time, I did not realize the enormous cost and scope of unscheduled machine failure, but I felt the pain on a daily basis.
One day in early 2013, I was sitting at the site of a major manufacturing plant working through realms of data. The idea came to me that there must be a way to use all this data to predict a machine breakdown before it occurs. This was the seed of the idea.
At the same time, Deddy Lavid – co-founder and CTO - was working on predictive analytics for energy. We shared some of our initial thinking with people from the industrial domain who validated the need for a predictive solution for fixing machinery parts before they break down. So, that’s how AI Predictive Machine Maintenance germinated.
In May 2015, we participated in the three month BizTEC Accelerator which is run by the Technion University in Haifa. We were assigned David Almagor as a mentor who has built and sold a number of companies including Panoramic Power. By September we secured angel investor funding and at this point, David Almagor joined the team. We were then able to hire our first programmers.
We then applied to participate in the four- month Microsoft Accelerator Program and finished the screening process ranked 1st out of the 400 companies that applied.
Our next round of funding was in June 2016. we received 2 million dollars in investment from AfterDox, JANVEST Capital Partners , SeedIL and an R&D grant from the Office of the Chief Scientist of Israel.
The rest is history…..
What does the term Industry 4.0 mean to you and how does it relate to the vision of the company?
It’s hard to find one common definition of Industry 4.0 and all the major players have very different roadmaps. From an industry perspective, it’s fascinating to watch the competing visions for the industrial sector from GE and Siemens. With that said, we are seeing the convergence of IT and OT. There are several obvious factors such as cost of data storage, connectivity, processing, cloud-computing etc. which area enabling the Industry 4.0 revolution.
But Industry 4.0 is also a shift in mindset. We’re in discussion with some of the largest manufacturers in Europe. There is a clear realization that big data can be operationalized in a way that will permanently change how goods are produced . If we do this right – and it’s a big “if” – then higher factory production rates and a reduction in commodity prices based on improved yield can impact the quality of life and even the climate.
I am going to be bold here. Presenso was built to play a leading role in both the change we are witnessing but also in the disruption that we are yet to see.
We’ve been fortunate to hire some of the most talented data scientists and engineers from Israel’s top academic institutions. Presenso has taken the most advanced Artificial Intelligence and Machine Learning that was formerly in the realm of academia and created a commercial offering.
Where do you see the biggest opportunity in the area of Asset Maintenance?
Looking forward to the next 3 to 5 years, the biggest opportunity is in the use of big data and Machine Learning. Today, we have the traditional Predictive Maintenance, but it’s mostly based on human defined measurements and performance thresholds. Up until recently, there has been very little innovation in the areas of asset maintenance.
At most, a factory is using 3% to 5% of its sensor asset data to predict failure. Usually, this number is closer to 1%. Some companies are still struggling with accessing the data that is generated by sensors, but that is changing.
Solutions such as Presenso can access all the sensor data from a production facility and use it to predict machine degradation or asset failure for all assets. In real-time, we analyze all the sensor data and detect abnormal data patterns.
To answer your question directly, thanks to IIoT, we are likely to see improvements in asset uptime, which is really the Holy Grail of the Smart Factory.
What was unique about Presenso’s approach to Machine Learning for Asset Maintenance?
Our approach is an Unsupervised Machine Learning one and this is what sets Presenso apart. Unsupervised Machine Learning is much more cost effective than Supervised Machine Learning because the algorithm does not need blueprints or understanding of the physical process to “learn” the behavior of the asset. This may not sound significant, but it removes the human element from Machine Learning. Instead of building a virtual model (aka the Digital Twin), we are agnostic as to the asset class or sensor type. We are simply looking for abnormal patterns in data behavior.
There are quite a few companies in this space, how is Presenso different?
I speak to clients and prospects every day and most of them are in the process of evaluating the Digital Twin. Let’s put aside the price differential which is not always the driving factor. When you implement the Digital Twin, you need to bring in an army of big data scientists, consultants and CAD technicians. The virtual clone needs to be customized based on the blueprint for the physical asset.
Our approach is fundamentally different because we do not rely on customers engineers’ to learn the behavior of the machine. Therefore, deploying Presenso takes a fraction of time it takes to deploy the Digital Twin.
Asset Maintenance solutions tend to be machine-specific. In other words, they analyze the data from one specific type of machine. With Presenso, we extract sensor data for an entire production facility so one installation fits many different types of machines.
About Eitan Vesely
Eitan Vesely is the CEO of Presenso. He was previously a hardware specialist and a support engineer for Applied Materials where he specialized in software-hardware-mechanics interfaces and system overview. Eitan holds a BSc. Mechanical engineering.
The content & opinions in this article are the author’s and do not necessarily represent the views of ManufacturingTomorrow
Comments (0)
This post does not have any comments. Be the first to leave a comment below.
Featured Product
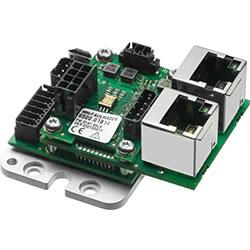