With such a wide and diverse selection of Multi-Tasking machines available today, its sometimes hard to imagine a situation when using single task machines is a better option, but there are more than most shops would think.
What to Consider When Choosing Either a Single-process or Multi-Tasking Machine
Joe Wilker | Mazak
Most shops today have some level of Multi-Tasking capabilities, one machining center that combines several cutting processes to reduce job setup time, increase capacity, improve machining accuracy and conserve valuable shop floor space. But is it always best to use a Multi-Tasking machine, or are there times when using a milling machine and/or separate turning machine is a better option? Here are five things to consider when making the choice:
1. NUMBER OF PARTS
Part volume is a critical factor when choosing between using a single operation machine and a Multi-Tasking machine. With the exception of automotive part production, most lot sizes today are smaller because no one wants to hold a lot of inventory. Multi-Tasking was originally developed for low lot sizes, although the addition of a second turret that enables simultaneous operations has taken modern machines to another level. This makes Multi-Tasking a great choice for most small to medium production runs, especially since there are so many configurations that provide differing capabilities.
High volume runs, however, may be a different story. If you’re processing 10,000 parts, it may be better to go to stand alone machines. The best way to make the decision is to conduct a time study that will provide critical information that can help determine which method would be best.
2. OPERATIONS
Perhaps the most obvious consideration is which operations are required to produce a particular part. Most jobs require more than one operation to complete the parts. Using single task machines to produce these jobs means the parts must be moved from one machine to another for each operation.
There are two main concerns anytime you are moving a job from one machine to another. The first is the additional setup time. Because setup consumes such a large percentage of the overall production time on a job, eliminating multiple setups can have a significant impact on productivity and part cost. Saving five minutes on cycle time is nice, but saving hours of setup time can make a real impact on profitability. This is especially true on repeated or small lot size jobs.
The second main concern when moving a job from machine to machine is loading the part the exact same way to maintain accuracy. Using a Multi-Tasking machine ensures that the geometry points are consistent between operations as long as the machine is in tolerance and in spec. In the rare situation that a job requires only one operation to complete, however, a single task machine is likely the way to go.
3. TOOLING LIMITATIONS
What type and how many tools will it take to produce the part? Some modern Multi-Tasking machines offer new tooling possibilities that enable gear cutting, additive manufacturing and even a flash tool that makes O.D. machining possible as well as turning, facing, grooving and threading. In some cases, however, your Multi-Tasking machine may not have enough tool capacity to complete all the operations a part requires. In this situation, you may need to split the operations between two or more single operation machines that can accommodate enough tools.
4. PART SIZE
Although Multi-Tasking machines are now available in larger sizes, there are still more platform options with vertical or horizontal machines. Processing of some extremely long and/or heavy workpieces is best suited for vertical machines with full traveling column designs or super high-torque horizontal machines with extra wide machining areas.
5. COST
How much is the part going to cost you to produce using a Multi-Tasking machine versus two single operation machines? In addition to material and labor costs, make sure to factor in workholding and tooling needs, power consumption, floor space, process in-cue time, work-in-progress time and even machine costs when figuring your total part production cost. Only then will you get a true picture and be able to compare your profit potential for each method.
With such a wide and diverse selection of Multi-Tasking machines available today, it’s sometimes hard to imagine a situation when using single task machines is a better option, but there are more than most shops would think. The best plan is to look critically at every aspect of each job while keeping in mind exactly what machines you have on your shop floor before deciding the best method for producing the most accurate parts in the fastest manner possible.
About Mazak
Mazak Corporation is a leader in the design and manufacture of productive machine tool solutions. Committed to being a partner to customers with innovative technology, its world-class facility in Florence, Kentucky, produces over 100 models of turning centers, Multi-Tasking machines and vertical machining centers, including 5- axis models. Continuously investing in manufacturing technology allows the Kentucky Mazak iSMART Factory to be the most advanced and efficient in the industry, providing high-quality and reliable products through its “Production-On-Demand” practice. Mazak maintains eight Technology Centers across North America to provide local hands-on applications, service and sales support to customers. For more information on Mazak's products and solutions, visit www.mazakusa.com or follow us on Twitter and Facebook.
The content & opinions in this article are the author’s and do not necessarily represent the views of ManufacturingTomorrow
Comments (0)
This post does not have any comments. Be the first to leave a comment below.
Featured Product
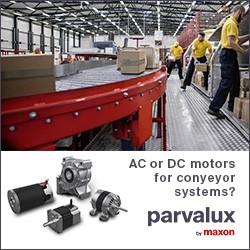