Automate 2017 is the largest culmination and collaboration of our customers and prospects in the world of industrial automation, robotics, semiconductors, surface mount technology, motion control, machine vision and so much more.
Talking Automate 2017 with Dipesh Mukerji, VP Marketing & Strategy for KINGSTAR
Dipesh Mukerji | KINGSTAR
Your company will be exhibiting at Automate 2017, what is it that makes this an important event for your company?
Automate 2017 is the largest culmination and collaboration of our customers and prospects in the world of industrial automation, robotics, semiconductors, surface mount technology, motion control, machine vision and so much more. It is important that such a community is aware of KINGSTAR’s presence and our significant contributions to this community. We intend to make attendees’ lives easier, faster, efficient, productive and cost effective with software. We use this event as a means for showcasing our software capabilities, and creating a rich dialog conversation around machine automation for motion control and machine vision, with real-time PC-based technology.
What can a visitor to your booth expect to see this year?
At booth 349, KINGSTAR will demo its software motion control platform. Visitors to booth 349 can expect live demos of KINGSTAR’s EtherCAT-enabled PLC on a servo motor and expert best-practice resources, including a cost and performance breakdown of using software vs. hardware, and 5 real-time Ethernet-based fieldbuses compared. The KINGSTAR platform allows C++ programmers and non-programmers alike to integrate their PLC with an entire platform of add-on or third-party components, like motion control and machine vision, through an intuitive, UX-driven interface.
KINGSTAR will also demonstrate each of the components of its soft motion platform, including:
- KINGSTAR Soft PLC, delivers application management and deployment that enables complete and consolidated control of assembly lines and machinery.
- KINGSTAR Soft Motion, provides an integrated environment for consolidated, inexpensive and scalable motion control. Soft Motion runs directly on the PC, uses the NIC card for I/O, and uses the powerful EtherCAT protocol for freedom from proprietary and costly hardware.
- KINGSTAR Machine Vision, powered by Matrox, allows engineers to build interactive applications and functions for image capture, processing, analysis, annotation, display, and archiving on GigE Vision® and other camera devices.
- KINGSTAR EtherCAT, exposes the real-time interface that allows engineers to integrate their own motion control algorithms or software with an EtherCAT network, providing highly customizable motion control and machine vision with precision performance at an affordable price.
- IntervalZero RTX64, the foundation of the KINGSTAR platform, replaces FPGAs and DSPs by transforming Windows into a real-time OS (RTOS), reducing development costs and significantly improving the quality of embedded systems.
Any new products you will be introducing?
At booth 349, KINGSTAR will demo the new 3.1 version of its software PLC and motion control platform. KINGSTAR 3.1 includes an ESI import tool, multi-axis coordinated motion with linear 2D and 3D circular motion; easier upgrades to supported hardware; and features like E-CAM and Shutdown Handler support. Generally available Soft PLCs only offer a real-time extension that is limited in both features and support of real-time processing. KINGSTAR provides a fully-featured EtherCAT-enabled software PLC, with an open and accessible RTOS, that is included with, and the foundation of, your PLC, and managed by a rich user interface for C++ and non-developers alike. With KINGSTAR 3.1, users can not only benefit from replacing hardware PLCs with software PLCs, but also leverage an open, integrated “plug and play” platform for future needs like motion control and machine vision
When you get a chance to walk the exhibit hall floor yourself, what is it you will be most interested to see?
We are predominantly excited by participating in the culmination of ideas and discussions with those we could potentially work with in robotics, semiconductor and industrial machine automation arena, and subsequently with those who want to work with us. We believe in the collaboration of ideas and principles that Automate 2017 is based-upon. To be offered a chance to meet with a community that can potentially help each other and facilitate organization’s initiatives of being more productive, efficient, faster and cheaper. We are looking forward to having this discussion at Automate 2017 as we stop by booths of those in industrial automation industries, PLCs, motion control, robotics, and machine vision to deliver our message and also absorb our counterparts message as well. Ultimately we hope to learn from others by walking the floor and create a dialog with partners, customers, competitors and prospects alike.
Automate 2017 has over 100 educational sessions, is your company involved in any of them this year?
KINGSTAR CTO, Daron Underwood, and Director of Field Engineering, Jerry Leitz will be sharing their expertise in two sessions. Daron will present in “Implementing IIoT and Industry 4.0 Solutions” on Monday, April 3 at 9AM eastern, and Jerry will teach in the “Advances in Motion Control Technology” session on Wednesday, April 5 at 9AM eastern.
Daron’s session will consist of the following:
Unlike traditional solutions, which require one controller per machine or Industrial PC, a real-time operating system (RTOS) for Microsoft Windows 10 can host multiple controllers on a single multicore PC. Uniquely, a proper RTOS solution not only eliminates unnecessary, redundant hardware costs, but also simplifies controller integration because all the controllers – motion and vision, for example – can access the same deterministic-enabled shared memory. Since Windows 10 and an RTOS can be co-resident, this enables a breakthrough in the way controller performance and operations data can be shared with Azure for IoT.
In this session you will
- See an RTOS running on Windows 10 for IoT
- See how an RTOS benefits the IoT industry and streamlines development of Industry 4.0 systems
- Learn how to develop tools for Windows 10 IoT Enterprise
In this session you will learn
- How to produce and IoT image that boots and configures for an RTOS
- How to get an RTSS subsystem working on Windows IoT Core
- How to develop tools for Windows IoT Core and leverage towards IoT Enterprise
and Jerry’s session will consist of the following:
Let’s face it: the standard method for configuring servo motors and drives through network control software is cumbersome and time-consuming. For each motor manufacturer, engineers must independently download and install the libraries and files into their IDE and run proprietary configuration tools to build separate ENI.XML files to define the drives. Every time there is a change or update to the network, you have to do it again, and you must repeat the process for each of your motors. Auto-configuration of an EtherCAT network for servo drives and motors is one of many ways to deliver the most open and flexible soft motion platform on the market.
This approach offers several clear benefits:
- Instant configuration of all major motors and drives
- On-the-fly updates for new, replaced, or edited servos
- No need to run and manage separate ENI.XML files
- Easily configured by on-site resources
- Open to all drives, with the ability to add new drives quickly and easily
In this session you will learn
- How to compile a single master file that holds the relevant information for all major drives
- Get the information needed to write applications ready and waiting at fingertips
- How to add new drives and automatically register and configure on-the-fly
When you book a booth for a tradeshow like this what are your expectations and what does your company hope to accomplish at the event?
The expectation is to foster and garner discussion around real-time software based motion control and machine vision via an EtherCAT-enabled software PLC, that we believe is valuable to our customer and prospects. We hope to engage and collaborate with said attendees around this extremely important and beneficial idea, by showcasing our capabilities that make their lives more productive, efficient, quicker and affordable. KINGSTAR has worked with over 600 leaders in machine automation to learn best practices for implementing EtherCAT in robots and PLCs. With KINGSTAR, users can not only benefit from replacing hardware PLCs with software PLCs, but also leverage an open, integrated “plug and play” platform for future needs like motion control and machine vision. KINGSTAR delivers a cost-effective means to meet machine automation needs today and in the future, enabling over 56% cost reduction without sacrificing performance. We believe those at Automate 2017 will absorb our mission and beliefs, and choose to work with us to make their lives easier and better, to ultimately execute on their respective objectives.
The content & opinions in this article are the author’s and do not necessarily represent the views of ManufacturingTomorrow
Comments (0)
This post does not have any comments. Be the first to leave a comment below.
Featured Product
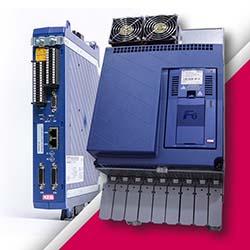