Continuous Inkjet, or CIJ, is a printing method commonly used in high-speed packaging lines to apply alphanumeric character strings like dates and batch numbers to products for the purpose of allowing humans and machines to identify products and verify product integrity.
Machine Vision Solutions for CIJ Print Inspection
Eldad Ben Shalom | Microscan Systems, Inc.
Continuous Inkjet, or CIJ, is a printing method commonly used in high-speed packaging lines to apply alphanumeric character strings like dates and batch numbers to products for the purpose of allowing humans and machines to identify products and verify product integrity. Machine vision systems are typically employed in packaging lines to ensure the quality and accuracy of printed data to comply with packaging and labeling requirements. This is made possible through Optical Character Recognition (OCR), a machine vision tool that interprets printed text on products to ensure data accuracy with high precision, enabling manufacturers to meet regulations and avoid fees and recalls with ultimate production efficiency. However, in the highest-speed packaging lines that employ CIJ printing, even minor fluctuations in product movement or equipment position may result in printing errors, causing machine vision systems to miss or misinterpret printed characters. This white paper provides guidance on using machine vision tools to account for the most critical CIJ printing errors, and discusses:
- Common challenges in high-speed CIJ printing that result in illegibility or misinterpretation of data by machine vision OCR
- How to evaluate errors to identify the key print defects that must be accounted for by vision in a given production environment
- Machine vision solutions for CIJ print accuracy inspection and tips on selecting the appropriate system for a production line
What Is CIJ?
CIJ stands for “continuous inkjet” – a non-contact printing method that expels a continuous stream of ink droplets from a printhead nozzle to the surface of a part or package. Inside the print chamber, ink is broken into drops by a pulse from a piezoelectric crystal. The ink droplets needed for printing are charged by an electrode as they form resulting in a controlled, variable electrostatic charge on each droplet. Once the droplets are charged, they pass through an electrostatic field and are deflected by electrostatic deflection plates. The speed and charge of each droplet determines the position of the droplet on the substrate. As many as 120,000 droplets are expelled every second, without direct contact of the printer to substrate, making the CIJ printing method extremely versatile and responsive to changing print requirements. This versatility makes CIJ an ideal printing method for high-speed applications, as well as variable information, such as dates, times, batch codes, product information, logos, and other text on goods and packaging.
.png)
The major advantages of the CIJ printing method are a) the high velocity of the ink droplets, which allows for a relatively long distance between the printhead and the substrate, and b) the very high drop ejection frequency, allowing for high-speed printing. Since the printer’s jet is always in use, its nozzle does not clog, allowing solvents like ketones and alcohols to be employed, giving the ink the ability to “bite” into the substrate and dry quickly. CIJ can also be used with relatively high reliability to legibly mark most materials regardless of substrate type, shape, or texture.
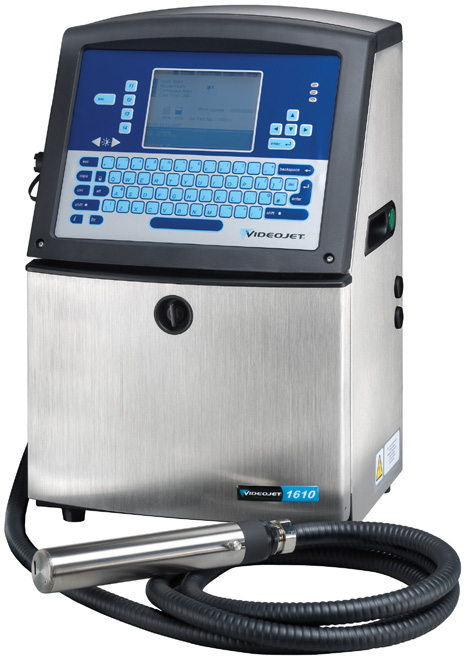
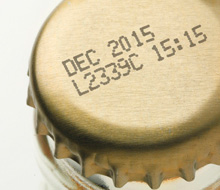
When used appropriately and well-maintained, CIJ printers are one of the most efficient means of direct printing to parts and packaging. However, there are several factors that can cause defects and illegibility in CIJ-printed content. In most cases, these include incorrect distance from printhead to substrate (causing poor print quality or gaps and overlaps of printed ink drops), dirty printhead (causing missed dots), and incorrect line speed or setup for an application (causing skewed dots).
What Is OCR?
In machine vision applications, Optical Character Recognition (OCR) is the process by which a machine vision system interprets arrangements or patterns of pixels in an image as human-readable text. The machine vision system uses OCR tools in its software to recognize letters and numbers within an image by pattern-matching against stored fonts, defining and outputting these characters as alphanumeric data (ASCII data) to a computer or control system. Commonly, machine vision systems are programmed with standardized OCR font sets, such as OCR-A, OCR-B, MICR, and SEMI, which are commonly used when printing to goods and packaging to enable optical character recognition by machines.
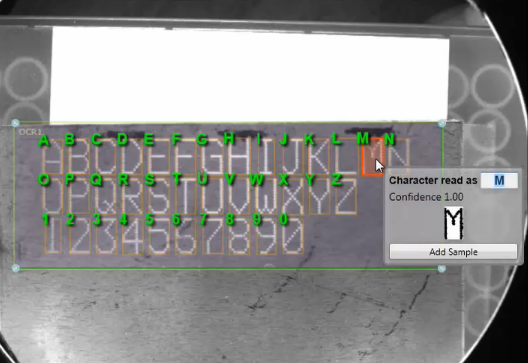
The primary advantage of printing in OCR for product identification is that OCR encodes information in a format that is both machine- and human-readable, while symbols like barcodes are only machine-readable. However, data encoded in barcodes is commonly more reliable than OCR, since OCR can have a high rate of character substitution (misinterpretation of characters by the machine used to read them). This can be due to defects in the printing method, causing imperfect characters that are undecipherable to the machine vision system. In cases where a non-standard font is used for OCR, the machine vision system may not be able to recognize characters because their pixel arrangements do not match what is stored in the machine vision system’s font library. In higher-end machine vision systems, teachable OCR tools can be trained to recognize characters in any user-defined font, not just specialized OCR fonts (OCR-A, OCR-B, MICR, SEMI) and can be taught to recognize a full character set in any font created for any language.
CIJ Printing Challenges that Impede Machine Vision OCR
Due to the technical nature of the CIJ printer combined with the high-speed movement of products in packaging applications, CIJ-printed text is susceptible to variations in character size, shape, orientation, scaling, position, and other defects that may result in illegibility by machine vision systems using OCR. These challenges are compounded by the typical variables of a machine vision system integration, such as ensuring proper illumination, optical setup, and other design considerations.
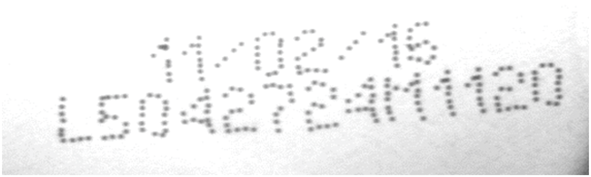
Common print defects in high-speed CIJ printing are presented below through several image examples. The text has been printed on aluminum cans by a CIJ printer at a production rate of up to 800 PPM (parts per minute), and the images have been captured by the same machine vision system in all examples.
Example 1:
The image below shows a clear difference between the positioning of the dots for the character “2” printed at two locations on the can surface.
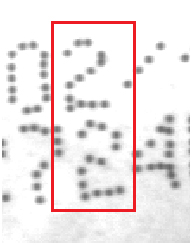
Example 2:
The range of “1” characters below have been printed by the same printer head. Clearly there are significant differences in the distance between dots from one print instance to the next.
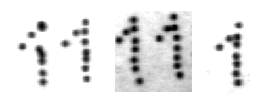
Example 3:
This pair of “5” characters below exhibits a drastic difference in appearance as a result of displacing just 2 critical dots in the bottom right, which deviate nearly 15% from the ideal character shape. Machine vision OCR may find it impossible to interpret this second character as a “5,” since even a human reader could make the mistake of interpreting this character to be a “6.”
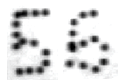
These variations may have been the result of the high conveyor speed, (which may not be consistent), the bouncing of the can from side to side on the narrow conveyor, or the inconsistent surface substrate (curves, folds, or dents) of the can. These factors can cause minor changes in distance from the can to the printhead, which is unpredictable and an inevitable possibility on any production line.
Example 4:
In the example below, compare the character “M” on the left with the character “1” on the right. If the “M” were split in the middle, it would look like two “1” characters in mirror image to one another. A machine vision system, not having human logic, could make the mistake of interpreting the right half of the "M” as a “1,” followed by a consecutive “1” to the right. The mirrored “1” on the left would then be skipped as an unidentified character.

Example 5:
Below are two consecutive, “identical” prints from the same printer. The second set of characters was printed one minute after the first set. Notice the “1” character on the far left. The displacement of just one or two dots in the character’s makeup cause quite a range of patterns, which all must be identified by the machine vision system as “1”.
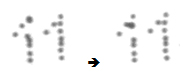
Example 6:
The image below exhibits a significant change in character size from right to left. A common cause of this is the position of the can while moving on the conveyer together with the curved surface of the can. On the right side, the printer head is closer to the object. On the left side the printer head is further away. Therefore the characters are smaller on the right side.
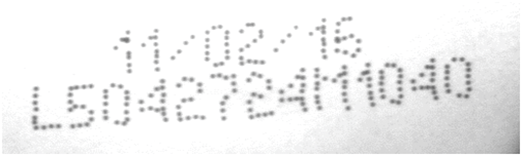
It is clear to see why applications like high-speed CIJ printing pose such a challenge for machine vision systems. Vision systems must use their OCR capability to correctly parse and classify each character they see as a known value in the accepted alphanumeric set for data interpretation (which is commonly called ASCII (American Standard Code for Information Interchange)). The more pattern variations that occur in each instance of a single character, the harder it is for the machine vision system to make a clear distinction between one character and another.
For manufacturers whose processes rely on extracting ASCII data from text printed on their products and packaging, and who face challenges like those illustrated in the above examples, a few questions should be asked:
- Do I need my machine vision system to read every character on every product in 100% detail?
- Do I need the data string that is printed on my products to be compared to an intended “match string”?
- How sensitive is my production line to false rejects?
- How sensitive is my production line to overlooked defects?
The answers to these questions will usually determine the required application of machine vision OCR with the clearest specifications for the integrator or machine vision engineer. The result is a machine vision solution for CIJ OCR that solves the core problems, and is simple to design, install, and maintain later... (full white paper available here)
The content & opinions in this article are the author’s and do not necessarily represent the views of ManufacturingTomorrow
Comments (0)
This post does not have any comments. Be the first to leave a comment below.
Featured Product
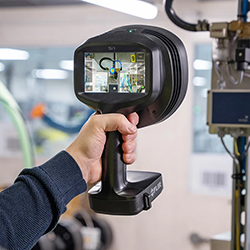
Affordable Excellence: The Go-To Tool for Finding Compressed Air Leaks
Find compressed air leaks fast with FLIR's new cutting-edge Si1-LD acoustic imaging camera. Leveraging advanced ultrasonic technology and onboard analytics, this affordable camera pinpoints leaks and quantifies incurred losses even in the nosiest environments. Upgrade your maintenance routine with the cost-effective FLIR Si1-LD - significantly reduce energy costs and increase system uptime. Get Started Today.