Updated Delcam FeatureCAM, PowerMill and PartMaker Software Now Part of Autodesk Manufacturing Portfolio.
Contributed by | Autodesk
Updated Delcam FeatureCAM, PowerMill and PartMaker Software Now Part of Autodesk Manufacturing Portfolio
Autodesk is ushering in its new 2017 Computer Aided Manufacturing (CAM) products for a multitude of advanced manufacturing applications ranging from CNC mill- and lathe-programming to complex mold and die manufacturing. These new products combine the heritage of industry leadership in CAM software from Delcam with Autodesk’s 3D design and manufacturing prowess, presenting Autodesk CAM customers with a powerful and unique user experience.
Autodesk’s 2017 CAM solutions include enhanced versions of FeatureCAM for automating CNC programming; PartMaker for precision part manufacturing with Swiss-type lathes; PowerMill for designing the most complex molds, dies and other components; PowerShape for the design of 3D complex parts; and PowerInspect hardware-independent inspection software. New capabilities for each of the 2017 CAM products are detailed below.
“Manufacturers need to iterate and innovate faster than ever before to stay competitive as the marketplace is redefined by a new future of making things,” said Mark Forth, manager of manufacturing industry strategy at Autodesk. “Autodesk’s new 2017 CAM products are designed to help our customers learn, improve and master advanced manufacturing techniques that ultimately lead to better designed and functional products being brought to market more quickly and efficiently.”
Next month during the IMTS 2016 conference in Chicago, IL, Autodesk will outline its broader vision and software portfolio to support manufacturers in this new competitive environment. In addition to the technologies unveiled today, the company will also spotlight solutions for additive manufacturing, CAM, composites and more.
FeatureCAM 2017 and PartMaker 2017
Autodesk FeatureCAM is an easy-to-use solution for milling machines, turning and turn/mill centers, and wire electrical discharge machines (EDMs). The automation tools within FeatureCAM help manufacturers reduce programming time, allowing parts to be made faster. They also increase programming consistency for maintaining part quality. The 2017 version of the product includes the following improvements:
- New programming capabilities for dual-path Swiss-type lathes, further improving its range of CNC machine support
- Ability to import and view product and manufacturing information directly from a model in order to help visualize design specifications
- Access to functionality that allows pre-drilling when using Vortex toolpaths, ruling out the need for helical ramp moves
In addition to the features above, PartMaker 2017, which enables complex, high-precision part manufacturing with Swiss-type lathes, is now available within the FeatureCAM 2017 Ultimate product tier. The two products in combination form a complementary bundle that effectively addresses the programming requirements of today’s manufacturing shops.
“We have a great history working with FeatureCAM, and when we were asked to evaluate the new Swiss lathe functionality, it was a no-brainer for us,” said Bill Karas of Karas Kustoms. “In the past, I had been programming the Swiss machine by hand. Using FeatureCAM for the Swiss machines saves our company a ton of time with excellent results.”
PowerMill 2017
Autodesk PowerMill 2017 takes the ability to easily and effectively manufacture the most complex molds, dies and other components to new heights. This latest version includes the following new features:
- More efficient 3D offset finishing toolpaths, greater simulation controls and constraint-based logic to optimize non-cutting link moves for safer, more efficient machining
- For the first time, PowerMill also provides strategies to create turning routines for use on 5-axis mill-turn machines
These improvements continue to make PowerMill the ideal choice for manufacturers looking to solve the most demanding of 3-axis, high-speed and complex multi-axis applications.
“PowerMill helps us to maintain a high level of consistency in our programming, which directly and positively affects time in process and customer satisfaction,” said Randy Lee Meissner, CNC Department Supervisor at Dynamic Tool and Design. “We develop processes where each engineer is using the same techniques and the same tools, so there is no variation among the work everyone is doing. In the old days, there may have been some hand-fitting, but today we can count on uniformity in the molds we create from order to order.”
PowerShape 2017
The design of 3D complex parts just became more effective with the following improvements to PowerShape 2017:
- Accessibility shading to identify areas of a part that cannot be machined with 3-axis machining alone
- A new rib capping tool allows users of EDM technology to automatically create surfaces in order to stop cutting tools from machining slots that will be produced by EDM. Hundreds of surfaces are created in a single command, saving hours of manual modeling.
- The PowerShape electrode wizard offers improved EDM hardware integration for shop-floor burning
- Finally, regular users of reverse engineering tools can benefit from improved fitting of surfaces to imported triangle meshes
PowerInspect 2017
Autodesk PowerInspect simplifies the inspection of complex shapes by providing a single solution for a wide range of measuring equipment. PowerInspect 2017 includes the following new features:
- Support for portable measuring equipment, coordinate measuring machines (CMMs) and On Machine Verification (OMV) are offered in a single package for PowerInspect Ultimate users. This improves productivity and flexibility by making it easier for operators to select the most appropriate measuring equipment for each job.
- The ViewCube feature offers specific benefits for visualizing inspection results and creating inspection reports
- A single click mechanism to recall the principal CAD viewpoints, making the creation of consistent inspection report images faster and easier than ever before
- Improvements to point-cloud performance now allows users to take advantage of the improved capabilities in the latest scanning equipment
- A dedicated point-cloud single point item provides an easy way to evaluate target points from laser scan data
Price and Availability
The 2017 products PowerMill, PowerShape, PowerInspect and FeatureCAM will be available to new and current customers starting August 1, 2016 in three levels: Standard, Premium and Ultimate. PartMaker 2017 will be included as part of FeatureCAM Ultimate.
All products will be available as perpetual and maintenance licenses and through Autodesk Subscription, a purchasing option that provides access to Autodesk desktop software with lower upfront costs on a term-based license to meet a variety of business needs and budget considerations.
New feature videos for PowerMill 2017:
FeatureCAM 2017:
PowerShape 2017:
PowerInspect 2017:
The content & opinions in this article are the author’s and do not necessarily represent the views of ManufacturingTomorrow
Comments (0)
This post does not have any comments. Be the first to leave a comment below.
Featured Product
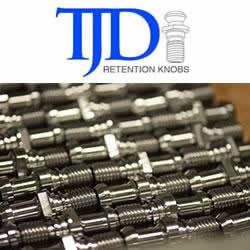