With the robotic board handling system, the company increased production an average of 20-30 percent and as high as 60 percent on some products.
Contributed by | Motion Controls Robotics
Challenge
An international building products company that provides support to general contractors, architects, engineers and governmental agencies needed an automated way to stack flat and tapered boards to both increase speed and alleviate large turnover in manpower.
Before working with Motion Controls Robotics, the company had no automation. Employees manually lifted and stacked the boards, often leading to injuries. The company also had a high employee turnover rate and used some temporary staff. In addition, the stacks created manually were often uneven, making it difficult to keep the products from leaning.
Solution
Motion Controls Robotics recommended a system using a robot with a vacuum-powered end-of-arm tool to position, square and pick up the boards from the existing equipment. The robot lifts the board and sets it onto a chain conveyor, rotating every other board. At a pre-determined count, the stacks are sent out to handling conveyors that move them to down-line equipment.
Motion Controls Robotics installed, tested and provided training and support during the startup to familiarize the associates on how to operate the equipment. Motion Controls Robotics technicians directly supervised start-up, eventually turning over operation to the newly trained employees.
Details
The robotic board handling system used two Fanuc M-410iB robots, HandlingTool software and custom written software to handle the robot motion. Peripheral equipment included an Allen Bradley 505 plc, and Panel View Plus1000 HMI.
Result
According to the company, this system allowed for three fewer employees per shift. By decreasing the number of employees, the company reduced manpower turnover and injuries. Straighter and neater stacks could not be achieved using the original manual system. With the automated system the robots can stack precisely and also rotate tapered boards every other part which allows for more even and straighter stacks.
With the robotic board handling system, the company increased production an average of 20-30 percent and as high as 60 percent on some products.
This robotic stacking system has run for nearly six years in one plant and more than a year in the latest plant to install the system. The robotic stacking system has been installed in six plants, with orders placed for three additional systems.
The key to Motion Controls Robotics’ long term success is simple. We provide well-engineered robotic solutions, pay attention to our customers’ needs and deliver excellent service for our systems. Our customers enjoy a high level of customer service and support and keep coming back for new systems. Motion Controls Robotics continues to develop technology and add new specialized applications that help keep our customers, American manufacturers, competitive.
The content & opinions in this article are the author’s and do not necessarily represent the views of ManufacturingTomorrow
Comments (0)
This post does not have any comments. Be the first to leave a comment below.
Featured Product
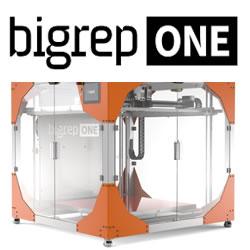