Why food packagers need to trust AI - It is time for food packagers to embrace smart technologies
A survey by McKinsey states that the adoption of automated technologies in the food and beverage industry is relatively slow compared to other sectors, with only 48 per cent of manufacturers considering themselves ready for Industry 4.0. Here, Claudia Jarrett, United States country manager of automation parts supplier EU Automation explains how and why food packages should put their trust in smart technologies and AI.
As the term suggests, packaging automation involves the use of machinery to replace one, or multiple manual, elements of packing operations. Smart technologies are also an efficient way to streamline the entire packaging process. These machines can automatically fill, cap, seal and label packages of varying sizes and shapes.
There are two types of automated packaging machines: fully-automatic and semi-automatic. While the functions of both are essentially the same, semi-automatic machines require more human labor, whereas fully-automatic equipment does not and therefore allows workers to upskill and avoid repetitive tasks.
Automated packaging systems are generally quite diverse, and can mean several things to different manufacturers. Here, we’ll focus on the food packaging process and where automated packaging is already being successfully utilized.
Tightly wrapped
Manufacturers are rapidly recognizing the benefits of automated packaging operations and are incorporating these machines into their lines.
Take for instance, PGP International, a food manufacturer that produces rice based flours, specialty flours and extruded ingredients for cereal products. The company implemented a new automated packaging line at its plant in California, US, to make its packing of flour into valve bags quicker, safer and more power-efficient.
The automated packaging equipment consists of a high-speed filling process, and in-line ultrasonic sealing capacity and automated palletization and stretch-wrapping facilities. For PGP International, its new, automated line has helped to ensure both the stability and safety of its packaged product.
The packaging also helps to guarantee safety of PGP’s produce during transit. The new line features a high-speed filling process that improves the density and de-aeration of the flour to be more compact and solid when the valve bags are full. After filling, the bags are sealed to reduce flour leakage, preventing other materials from entering the bag and minimizing the risk of infestation throughout the supply chain.
Get smart
While food packagers have been slow to uptake new technologies, today’s smart technologies are continually shifting and evolving.
Automated packaging is today supported by several advancements, including motion-control devices, 3D technology and sensors. As a result, sensors and vision technology can equip packaging machines to understand and interact with their surroundings with artificial intelligence (AI).
Previously, the aim of sensors has been to collect information and perform simple decision-making processes. Today, modern smart-sensor technology can prepare, process and interpret the data it collects. This data can be converted into valuable insights, allowing machines to perform complex tasks more efficiently.
For example, PWR Pack, a provider of robots for food packaging processes, has adopted 3D technology and sensors in its own packaging line to improve overall efficiency. The use of 3D technology in the line’s intelligent vision systems and sensors allows for precise product supervision and correct label placement, which is augmented further by PWR Pack’s quality-control process.
With robots and smart sensors proving their worth, the support of an industrial parts supplier can be vital in helping manufacturers choose the right sensor for their application. Obsolete parts supplier like EU Automation can source sensors for food packagers with quick turnaround, and even help monitor, repair and replace them after installation.
Seeing more
While smart technologies are used to automate the packaging process, they can also provide manufacturers with information that might otherwise but unobtainable. That includes improved defect detection. According to findings published by Siemens, “AI-based visual inspection is extremely effective at identifying anomalies in packaging, with some estimating that it detects 90% more defects than humans.”
In addition, this data can we shared among workers more fluidly than ever before. Human machine interfaces (HMI) are playing a more essential role packaging processes; particularly in connecting machines and the operators using them. These interfaces can be equipped with speech recognition, motion sensors, keyboard and similar peripheral devices through which data from the factory is shared.
To optimize a packaging process by digitizing and centralizing data for a viewer, HMIs allow operators to see important information in the form of graphs, charts or digital dashboards, and connect with supervisory control and data acquisition (SCADA) and manufacturing execution systems (MES) systems through one console.
Most SCADA software systems can also be integrated on portable devices. So, in theory, any portable device with a screen — whether it’s a tablet or a phone — can become an HMI, opening new opportunities for the flexible control and access of data.
Examples set by companies like PGP International and PWR Pack show that tangible advantages can be achieved by food and beverage companies that dare to be smart, and sidestep the sector’s traditional ambivalence towards Industry 4.0. Improvements to productivity, quality and safety in the factory can be achieved by food and beverage manufacturers that trust AI — it’s about daring to be smart.
Comments (0)
This post does not have any comments. Be the first to leave a comment below.
Featured Product
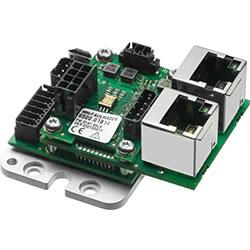