While AI and machine learning systems typically require around two years to collect enough data to reach their full potential, manufacturers can start seeing benefits almost immediately with basic analysis tools and dashboards.
The Rise of AI in Manufacturing to Collect and Use Data
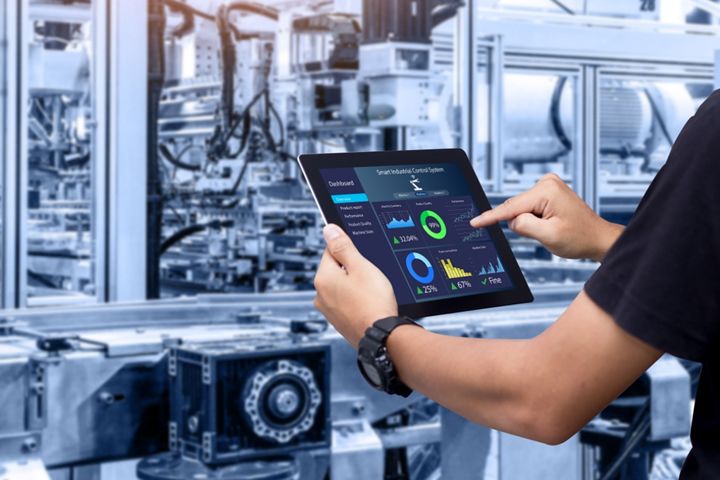
Jon Reneberg, Lead Digital Manufacturing Specialist | Purdue MEP
The manufacturing industry is in the midst of a dramatic transformation, driven by the availability of real-time data. This is the foundation of Industry 4.0. While skilled workers automation of repetitive tasks, smarter decision-making with artificial intelligence (AI) assistance, and reduced defects and downtime. This shift allows small and medium-sized manufacturers (SMMs) to compete more effectively on quality, speed, and cost.
It's important to clarify what we mean by "AI" in this context. We're not talking about generative AI to create software code or respond to questions. We’re focusing on practical applications of machine learning and predictive AI to collect and analyze data for optimizing manufacturing processes. The good news is that AI and automation tools are becoming increasingly available and affordable, leveling the playing field for SMMs by granting them access to cutting-edge technologies previously enjoyed only by larger enterprises.
While AI and machine learning systems typically require around two years to collect enough data to reach their full potential, manufacturers can start seeing benefits almost immediately with basic analysis tools and dashboards. This article will look at how manufacturing AI delivers these data-driven benefits.
How Data Collection Improves Manufacturing Performance
Ongoing data collection empowers manufacturers to make significant improvements across many areas of the operation. In fact, every area of your operation generates some type of data, whether you collect it or not. Building a foundation for collecting data can open your eyes to many possibilities for long-term success with AI.
Collecting data has helped manufacturers improve many areas of their operations. Here are some areas where it can help you:
- Reduce downtime. Predictive maintenance, powered by data analysis, allows you to anticipate equipment failures and perform maintenance proactively, which helps minimize costly downtime.
- Minimize scrap. By monitoring quality in real time, you can identify and address issues early on, reducing scrap and improving product quality.
- Improve cycle time. Data analysis helps optimize production speeds and efficiency, leading to shorter cycle times and increased output.
- Identify bottlenecks. By analyzing data across your operations, you can pinpoint bottlenecks and inefficiencies, allowing you to streamline processes and improve overall productivity.
Data collection and the subsequent improvements in your operation can indirectly help your employee satisfaction and retention. Automating processes with data-driven insights will reduce human error and fatigue, leading to increased job satisfaction and lower turnover rates.
The Rise of AI to Collect and Leverage Data
AI delivers data-driven insights that manufacturers can start benefiting from almost immediately upon launch.
Where to Start with Data Acquisition
Automation-based operations are better at collecting operational data than labor-based operations, however don't discount the intuition of an experienced machine operator who recognizes subtle noises or vibrations that indicate machine issues. Interview operators, maintenance personnel, supervisors, and quality control teams to understand their challenges and what data is valuable to them. Data can capture this "institutional knowledge" and be used for training new employees and predictive maintenance.
Conduct time studies to ensure you're focusing resources on the right areas. Ask questions like:
- What problems are we trying to solve?
- What data would you find valuable?
- What bottlenecks can we unlock?
Remember that people in your company will need different data based on their role. Some data is best suited for management decision-making while other data is crucial for real-time operations and monitoring. Consider these examples:
- Automated adjustments: If you frequently adjust a fan in a spray booth based on humidity, data can help automate this process for optimal control.
- Condition-based maintenance: Measuring multiple variables simultaneously, such as temperature and machine door cycles, enables true condition-based operation.
- Error reduction: In processes with multiple changeover options, barcode scanning can present operators with the correct data for each specific scenario, minimizing errors.
Operators use human-machine interfaces (HMIs), such as touchscreens and control panels, to monitor and adjust machine performance in real time. When adjustments are made in an HMI, they are transmitted digitally, and information about that transaction can be recorded and become part of an AI model for analyzing data, identifying trends, and making informed decisions to improve efficiency and reduce downtime. Capturing data from experienced operators’ input provides valuable data on their decision-making process in various situations.
Leveraging PLCs Through Sensors and Software
Programmable Logic Controllers (PLCs) have been mainstays for many years on the manufacturing floor, and they remain valuable assets. Retrofitting PLCs with sensors and updated software can provide cost-effective automation solutions in comparison with buying new equipment.
However, many operators lack the programming skills to fully utilize PLCs, and programmers may be hesitant to invest time in developing code for testing purposes. This is where a Supervisory Control and Data Acquisition (SCADA) system comes into play. SCADA systems use software and hardware to monitor plant-floor operations and network machines, providing a centralized platform for data acquisition and control. Look for SCADA solutions that are easy to design and implement, even without extensive programming knowledge.
An Introduction to Data Collection
Many SMMs struggle to implement digital solutions due to high costs, lack of expertise, and the complexity of existing systems, so there is a growing recognition of the need for easy to install, easy to operate, no-code PLC or PLC-like devices. Here at the Purdue MEP, part of the MEP National Network™ (MEPNN), we have worked with MxD, the U.S. digital manufacturing and cybersecurity institute, to deploy their innovative sensor kit.
MxD has developed a simple, versatile, and user-friendly sensor kit that allows manufacturers to easily collect data from their machines. We’re planning to install up to 15 of these kits. The kit includes digital inputs and analog inputs to collect data, and a stack light to display conditions. This allows manufacturers to monitor things like temperature, pressure, vibration, and other key metrics. The kit is “no code,” which means it is easy to use, even for those without programming experience, and offers a proof of concept to help SMMs see the ROI for investing in data and automation.
There are other more robust stand-alone data collection systems on the market. Some are subscription based, and others have an up-front cost.
Your Local MEP Center Has Experts Who Can Help You Leverage Data
In today's competitive manufacturing landscape, data collection is no longer just a differentiator – it's a requirement. Data is the key to operational efficiency, improved quality, reduced costs, and increased profitability.
To get started on your data-driven journey, contact your local MEP Center. Their experts can provide guidance and support tailored to your specific needs and can help you leverage data for success.
About the Author
Jon Reneberg, Purdue MEP
Lead Digital Manufacturing Specialist
Jon spearheads the Technology Acceleration practice at Purdue MEP, which is part of the MEP National Network. His expertise helps guide the integration of collaborative robotics, additive manufacturing/3D printing, manufacturing automation, reverse engineering, and CAD/CAM systems.
The content & opinions in this article are the author’s and do not necessarily represent the views of ManufacturingTomorrow
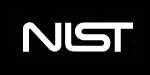
Manufacturing Extension Partnership (MEP)
The Manufacturing Extension Partnership Program (MEP) is a national network with hundreds of specialists who understand the needs of America's small manufacturers. Our national network consists of manufacturing extension partnership centers located in all 50 states and Puerto Rico. MEP provides companies with services and access to public and private resources to enhance growth, improve productivity, reduce costs, and expand capacity.
More about Manufacturing Extension Partnership (MEP)
Comments (0)
This post does not have any comments. Be the first to leave a comment below.
Featured Product
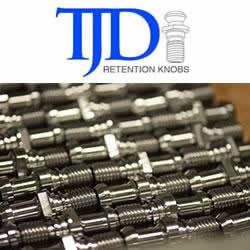