Supply chain uncertainty gives workers a chance to shine
Every day, new reports trickle in about yet another manufacturer struggling with labor shortages. A problem even before 2020, the novel coronavirus pandemic has greatly exacerbated the lack of skilled workers in factories. From the U.S. to China and everywhere in between, manufacturers are perceiving a situation where they have few options:
-
Bring in low skilled workers and try to rapidly educate them on the basics of manufacturing as well as train them on standardized work, knowing full well that turnover and absenteeism rates are both sky high;
-
Attempt to automate jobs that were previously performed by people, a proposition that requires time, money and, in many cases, skilled robots that simply don’t exist today;
-
Continue operating at a fraction of the optimal staffing level, making it nearly impossible to meet customer demand and risking product quality and staff burnout.
If you’re a manufacturer today, it’s easy to feel like you’re in a lose-lose-lose situation.
But maybe those three scenarios aren’t the only possible options. Though most manufacturers have long believed that people are maxed out, and when it comes to productivity, manual assembly lines are as optimized as possible, new technology is challenging that belief structure.
What if you could get more from the skilled workers you already have?
The reason manufacturers have held the belief that people have reached the limits of their productivity potential boils down to one thing: manufacturers lack meaningful data on manual assembly processes. Yes, there are time and motion studies, but the sparse data they produce is episodic, biased and inadequate to provide true insights into the manual assembly line’s performance.
But there’s a new way to gather data on manual assembly lines. By hanging a camera over every station on a line and processing the video stream using AI, manufacturers can finally get continuous, unbiased data that helps them uncover massive opportunities for process improvements.
The “brilliant outliers”: It’s time to give Raul a little recognition
Raul has worked on a refrigerator line for 15 years. He’s quiet, has a great work ethic and reliably shows up to work.
Jen, his supervisor, stumbled on his mastery of the work elements, his creativity and his brilliance when she was reviewing the characteristics of the line on which Raul works. She had noticed that particular line and shift was statistically doing better during certain periods, and upon digging deeper, realized that this was the case whenever Raul was at a particular station. Jen noticed that Raul’s cycle times were, on average, 2.7 seconds faster than all of his linemates. And his quality ratings were as high as anyone’s.
Jen clicked on a specific cycle that showed Raul performing well and watched video playback to learn his secret. It turned out that as Raul was slipping the refrigerant hose into the compressor, he first dipped it in a little glass of soapy water. The hose slid into the compressor with no fuss, while his linemates lost precious seconds on every cycle trying to do the same motion with a dry hose. In short order, Jen ordered little glasses of soap for every station on the line. Shaving off an average of 2.7 seconds every cycle on every station translated to major savings.
Without the video and AI technology, it’s likely that Raul’s trick would never have surfaced to the management team. His hack improved the standardized work of record to the benefit of the whole company, and Raul became a well regarded employee for the first time.
Lessons from COVID-19: People are more valuable than ever
The common misperception from the outside world is that assembly is pretty automated. As the last 18 months have demonstrated, assembly processes still hinge heavily on the work of people. Which means that when a disaster like a pandemic strikes, it can be devastating to the industry. But COVID-19 is far from the only threat to manufacturing around the globe: natural disasters, supply chain shortages, political unrest and other factors are always present.
Here’s where, again, people shine. People bring a level of adaptability of which machines simply aren’t capable. Changes in consumer demand, such as the massive increases of personal protective equipment (PPE) during the early days of the coronavirus, are much easier met by human workers than inflexible automation. Shifting production can happen quickly with humans, who can understand and apply new standardized work instructions within a single shift.
But, as we all know, humans introduce errors. They don’t run as repeatably or perfectly as machines; they get distracted or forgetful. That’s where technology comes into play again. It augments humans by giving them reminders when a step is missed, or providing a helpful, video-based training aid to transcend miscommunication or language barriers. In so doing, it ensures standardized work adherence and the minimization, or even entire elimination, of escaped defects.
It’s impossible to predict what will happen in the future, but if history is any indication, a shortage of skilled workers is the status quo in manufacturing. Using technology like AI and video analytics to augment and optimize workers benefits the entire manufacturing ecosystem: the manufacturer, the customer and, most importantly, the worker himself, who has a chance to demonstrate his skill in a recognizable way.
Dr. Prasad Akella is the founder and chairman of Drishti, an AI and video technology company that provides data, analytics and insights on manual assembly operations that drives significant operational improvements.
Comments (0)
This post does not have any comments. Be the first to leave a comment below.
Featured Product
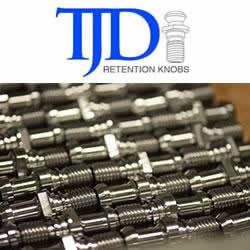