How to manage a complex network of new and legacy equipment
Legacy equipment is vital to the functioning of many manufacturing facilities. Nevertheless, with rapid advancement in automated and connected technologies, managing both new and old equipment simultaneously can be a challenging balancing act. Here Johan Jonzon, CMO and Co-Founder of pioneer in edge analytics for the industrial Internet of Things (IIoT), Crosser, shares insight into how manufacturers can successfully manage data from both new and legacy equipment.
In order to ensure an industrial facility runs efficiently and without unexpected downtime, it must be effectively managed and maintained. Management should include all physical assets, such as machines and connected devices, and non-physical assets, such as software and cloud access.
It’s common for industrial facilities to contain both new, digitalized equipment and legacy equipment that has not been defined with connectivity in mind, other than maybe to the local control room or local dashboard for the operator. Afterall, plant managers are unlikely to dedicate funds to upgrading to the latest model when a piece of legacy equipment is running with no problems.
Therefore, it’s normal for businesses to only invest in the new pieces of technology that are needed, finding ways to integrate them into the existing system. In addition, as businesses expand, it’s common for them to acquire new sites. Having a mix of old and new sites can add even more complexity into the mix, making it very difficult to streamline and unify data from all the different locations and pieces of equipment.
Retrofit IIoT devices
While legacy equipment may have been manufactured before the rise of IIoT, it can be given similar capabilities by retrofitting. This is also known as ‘wrap-and-extend’, where the device ‘wraps’ the piece of equipment with functionality and connectivity, therefore extending its reach in a number of ways. By updating the piece of equipment and increasing its functionality, the manufacturer also extends its life. This is because the machine can fulfil the company’s production requirements for a longer period of time before an upgraded replacement is needed.
The industrial apparatus, a 20-year-old CNC machine for example, can now have extended data reach, meaning more in-depth data can be collected about the machine, and extended legacy usefulness, therefore performing more valuably. The equipment is also extended in terms of machine performance and productivity through real-time insights, and through plant scalability, as operators can make more informed decisions about complex processes.
To gather data on equipment performance, sensors that measure vibration, temperature, or other parameters can be installed. Devices that are retrofitted onto legacy equipment can include Open Platform Communication (OPC) servers, IoT platforms and IoT gateways, which enable communication between new and legacy equipment.
There are several versions of OPC servers ― data access (DA), historical data access (HDA) and unified architecture (UA). OPC DA is the oldest version, which has less advanced data modelling and its transfer of information is only based on value, quantity and time. Furthermore, OPC DA only allows access to current data, and is incapable of creating alarms and historical events. OPC HDA is used to retrieve and analyze historical process data for purposes such as optimization, regulatory compliance and inventory control.
OPC UA has the same ability to deal with historical events but is more advanced, supporting other features such as multiple hierarchies and information modelling. In addition, OPC UA provides methods and programs called commands, and has better security than OPC DA. Manufacturers that are using OPC DA can find advancing into Industry 4.0 difficult due to security issues, challenging connectivity and slow communication speed. In fact, OPC UA is often viewed as a necessity for Industry 4.0.
Embrace the edge
Giving legacy equipment the ability to collect data offers one solution, but managing that data and attaching meaning is where the next challenge lies. We must first consider that a network comprised of many pieces of new and legacy equipment creates a massive amount of data. The bandwidth necessary to transmit that data to the cloud for storage and analysis can be expensive. This can be mitigated by edge analytics, which can act as a bridge between devices and the cloud, providing a local source of processing and storage.
Edge analytics can collect and filter data, storing or sending it to the correct location based on business rules. This means only the necessary data is sent from the edge to on-premise systems, such as a manufacturing execution system (MES) or enterprise resource planning (ERP). Data-reduction offloads the on-premise systems and reduces the amount of data that is transferred to the Cloud, saving Cloud and bandwidth costs.
Edge analytics is also capable of conducting down-sampling and summary analytics, which can further reduce the size of the data that must be sent to other areas on-premise. Machine data can be transformed by edge technologies into a common language that is understood by all equipment and devices in the facility, ensuring smooth communication.
However, handling a number of devices, a large amount of data, and a variety of different software and systems can soon become incredibly complex. For example, a 2021 report by software company Ubisense found that 40 per cent of manufacturing companies don’t know how to get started with IIoT. In an area that can cause a cloud of confusion, it’s important to work with a solution provider that can simplify implementation and management of IIoT devices.
Strive for simplicity
The Crosser low-code platform for streaming analytics, automation and integration for the IIoT was designed with simplicity in mind. Crosser’s Flow Studio, which is part of the platform, makes system programming easy for employees. The Flow Studio consists of a number of pre-built modules that can be dragged and dropped to easily construct data flows without any formal training or coding knowledge required.
The combination of modules created can be tested in a ‘sandbox node’ or on a live edge node before widespread distribution. Once satisfied with the data flow, it can be deployed across an unlimited number of edge nodes in one single operation. The Flow Studio is designed to empower collaboration between users, such as automation engineers, IT teams and data scientists, and is developed to be simple and intuitive to use.
IIoT devices are on the rise, but that doesn’t mean old equipment is being left behind. Many facilities rely on a mix of new and legacy equipment, and these systems must be managed effectively to ensure seamless communication and complementary operation. Companies can make the most of a diverse system by retrofitting IIoT devices onto legacy equipment, and using a simple edge analytics platform to process and store all of the data collected.
To learn more about Crosser and its edge solutions, visit https://crosser.io/
About Crosser Technologies
Crosser designs and develops Streaming Analytics, Automation and Integration software for any Edge, On-premise or Cloud. The Crosser Platform enables real-time processing of streaming, event-driven or batch data for Industrial IoT and Intelligent Workflows. It is the only platform of its kind that is purpose-built for Industrial and Asset Rich organizations.
The solution is built to fight complexity with simplicity through the Crosser Flow Studio, the visual design tool that enables teams to innovate faster than ever without developers. The software is ideally suited for Enterprise customers of various industries and applications, including Edge Analytics, Industrial Connectivity, Industry 4.0, Streaming Analytics, Hybrid Integration and Intelligent Workflows.
Industrial customers include, SCA AB, Valmet Corporation, Gebhardt, Clarebout Potatoes and RubbleMaster.
Crosser was included in the “Cool Vendors in IoT Edge Computing, 2018” report by Gartner, Inc. and was named among the Top 10 Smart Factory Solutions in Europe 2020 by the industry magazine Manufacturing Technology Insights.
Comments (0)
This post does not have any comments. Be the first to leave a comment below.
Featured Product
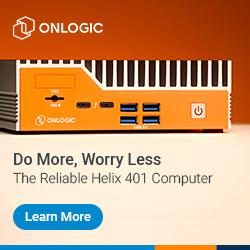