Understanding Air Filtration Systems for Your Manufacturing Facility
Using the correct air filtration systems in your manufacturing facility is essential for avoiding air pollution and keeping workers healthy. Here are some actionable tips for ensuring company leaders make the best decisions about their air filtration systems.
Understand the Manufacturing Processes That Cause or Need Protection From Air Pollution
Begin by taking a closer look at the activities in a manufacturing plant that cause the most air quality problems. From there, it’s easier to ensure the installation of the right types of air filters in the best places.
For example, if a manufacturing facility deals with welding, it generates fumes that can cause health problems. Estimates suggest that 10 to 20 pounds of fumes get generated with every 1,000 pounds of weld wire used.
Similarly, the products made in a manufacturing facility may dictate which filtration systems to use and where to install them. Food and beverage companies, as well as entities that manufacture pharmaceuticals, must take extra precautions to keep air free from contaminants.
Effective filtration in a manufacturing plant starts by understanding a company’s specific needs and concerns.
Learn About the Applicable Filter Standards
The global implementation of ISO 16890 in 2018 brought a new standard for air filter performance testing. One stipulation is that a filter achieves at least 50% particle removal efficiency to meet the criteria associated with the three most stringent categories.
They most often apply to manufacturing facilities with cleanroom facilities. However, they provide clear definitions for the expected performance of a filter that meets a certain standard. Other standards exist for high-efficiency filters as well.
Confirming which standards apply to particular manufacturing processes or locations is an excellent way for floor managers to ensure they meet all the related air filtration requirements.
See the Link Between Air Cleanliness and Maintenance
Carbon monoxide poisoning is a severe consequence of poor air filtration and malfunctioning equipment.
Fossil fuel-burning products, like gas and oil furnaces, produce carbon monoxide during operation. More than 20,000 Americans visit the emergency room each year with accidental poisoning from the gas. Routine equipment maintenance is an excellent way to prevent dangerous consequences, as is changing air filters frequently enough.
The Occupational Safety and Health Administration (OSHA) mentions effective air filtration systems and appropriate equipment maintenance as crucial for keeping employees safe from excessive carbon monoxide exposure while at work.
Moreover, OSHA prohibits worker exposure levels of more than 50 parts of carbon monoxide per 1 million parts of air during an eight-hour shift. Testing equipment can help verify compliance, especially in manufacturing areas known to produce the gas.
Know How an Air Filtration System Functions
People often speak of air filtration and air purification interchangeably. Both approaches clean the air, but they do it differently and vary in the impacts they have on indoor air quality. Air filters make climate control systems more efficient. They trap pollutants in a mesh-like component, preventing them from circulating throughout a building.
In contrast, air purifiers primarily kill bacteria and other microorganisms, typically with ultraviolet light. Whereas some filters trap bacteria, too, they’re usually the highest-quality options available.
Moreover, filters will not destroy what they catch. Knowing these distinctions is especially important if manufacturers want to buy products made to reduce the spread of COVID-19 in large facilities, including manufacturing plants.
Follow the Manufacturer’s Specifications
Besides following the suggestions here, the people responsible for selecting and installing air filtration systems in a manufacturing plant should refer to the applicable product information. It will discuss the appropriate settings for a certain type of air filter or system, plus how and when to perform maintenance.
Moreover, a facility’s air filtration needs may change depending on the type and volume of produced items, as well as the equipment used to make those goods. Thus, the responsible parties should verify that existing air filtration systems remain sufficient after any substantial changes occur in a manufacturing plant.
Comments (0)
This post does not have any comments. Be the first to leave a comment below.
Featured Product
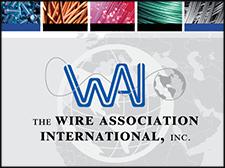