Manufacturing Resiliency and the Rise of Industrial Automation
The COVID-19 pandemic has exposed clear vulnerabilities in global supply chains and the manufacturing industry as a whole. This unprecedented health crisis showed that production lines have major issues with scaling and adapting to new products, especially when access and transportation become limited. The acceleration of smart manufacturing practices will be key to foster a more resilient manufacturing sector across the United States and around the world. As a result, there has been an increase in demand for smart industrial automation technology. New warehouses bursting with the latest industrial robotic technologies will play an important role. To better understand how manufacturing is transforming into a high-tech haven, it is important to examine the most promising technologies and applications in industrial automation.
In today’s warehouses, robotics work safely alongside and in parallel with employees to take on menial, repetitive and labor-intensive tasks, so employees can undertake more rewarding and mindful work.
By freeing up employees to focus on value-added tasks, factory productivity undoubtedly increases. After integrating robotics onto the assembly line, businesses typically reduce error rates while bringing about greater customer satisfaction. As robots are increasingly applied to in Machine Tool market, automating parts loading and unloading are solving labor scarcity challenges and increasing machine uptime – reducing the idol time of CNC machinery and protecting the capital equipment investment. The rise of robotics and mobility in automated warehouses and distribution centers make more possible when integrated with vision and artificial intelligence (AI) – increasing facility throughput even when social distancing measures are in place, and allowing for remote management or data analytics and information synthesis through the cloud.
The Future of Smart Industries
The ensuing economic crisis caused by the pandemic has uncovered hidden vulnerabilities in global supply chains – in particular, a lack of responsiveness and adaptability. Manufacturers need resiliency, flexibility, and scalability which is why they are turning to technology and automation to keep up with the times. There are a few pieces of technology that have stepped up to create the resilient manufacturing warehouses needed now.
Automated Mobile Robots
The most common that comes to mind when people think about manufacturing robots is Automated Mobile Robots, more commonly referred to as AMRs. These robots have an array of sensors that enable them to understand and interpret their environment and travel throughout a warehouse, performing their tasks in the most efficient manner possible. When looking at manufacturing, the technologies are integrated with the warehouse’s control systems, which allow AMRs increased flexibility to create their own routes between locations within a warehouse or facility. The robots can also be paired with wireless charging technology which allows the robots to guide themselves to charging docks until they are ready to be deployed again – eliminating the need for a human to manually plug the robots into a charger, thereby also reducing charger wear-and-tear.
Bionics & Wearables
Bionics and wearables technologies are geared toward enhancing the human workforce and providing workers with an extra layer of support and productivity. Warehouse workers often rely on computer tablets, scanners and other devices that can be integrated into wearable devices and heads-up visualization displays. Combined with augmented reality, these displays help direct workers to take the most efficient path from point A to point B, show checklists for easy reference and more.
Manufacturers need to work quickly and accurately to keep production costs low and quality output high. Another way workers are being augmented is through exoskeletons – external braces that protect workers and allow them to lift weights which would otherwise be deemed dangerous. These can range in sophistication from passive, which do not have motors or actuators, to powered, which do. Additionally, these exoskeletons help reduce strain on the worker and reduce the risk of injury.
SCARA & 3D Vision
Lastly, robotic arms are a critical component of modern warehouses and something we can expect to see more of in 2021. SCARAs (Selective Compliance Articulated Robot Arms) have a higher level of speed-precision-sensory control over traditional cartesian or 6-axis articulated robotic arms. As it relates to material handling, SCARA robots with 3-4 axis (or even an additional axis for tilt, which is called a 4+1 or 5th axis) can be deployed for efficient randomized bin-picking operations. The 5th axis enables assembly lines to effectively dispense onto parts a 2 or 3 dimensional pattern on passing parts without the need to upgrade to a 6-axis vertical articulated arm. Even with less axes, advanced SCARAs rival the range of motion as lower-end 6-axis articulated arm. The setup and calibration is also much faster since a SCARA mechanism is more simplistic to move – an important consideration when scaling up facility operations.
Additionally, advancements in 3D vision technologies also boost the capabilities of these robotic arms. For instance, the arm can sit above a random pile of objects, understand the angles that objects are resting and determine the best path for the SCARA when picking and placing it into a bin without collision on the sidewalls. It can also help determine depth and irregularities on an assembly production line to complete micro-precision tasks efficiently and accurately. 3D vision combined with SCARAs allow them know where they are in the space, adding a new dimension of intelligence. This combination turns menial work into quick work, and will likely be seen in more warehouses across the globe.
The ongoing pandemic has forced many industries to adapt to this new normal – this is particularly true in electronics and medical assembly, CNC machining, packaging and material handling. When production capacity increases exponentially, the rest of the business operations needs to adapt to reap the full benefit. Businesses are no longer looking for ways to just recover from this crisis. They are looking for methods to adapt and move forward, anticipating the needs of the consumer. Warehousing is one such industry, and its future will be highly intertwined with advanced industrial robotics for years to come.
Comments (0)
This post does not have any comments. Be the first to leave a comment below.
Featured Product
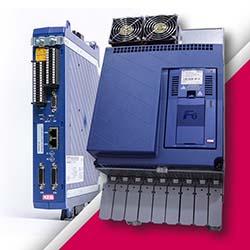