Designing Zero Defect Manufacturing Systems Post-Pandemic
Years ago, I created a simple “spot-the-difference” exercise for the firm where I worked, asking the team to compare two nearly identical images. Roughly one fourth (24%) of those who took the test got it wrong. Half found too few differences, the other half too many.
My point at the time was that if they could not successfully complete a visual inspection on a puzzle designed for children, how could they expect our supply chain partners to be perfect when inspecting our parts. That formed the foundation of a defect containment strategy focused on prevention over inspection.
I’m reminded of that exercise and strategy now as the world begins to emerge from pandemic shutdowns and ramp up production. In the time of lean manufacturing where almost no company is fully vertically integrated, companies simply cannot have defective parts show up at their doorstep or build in lag time to allow for additional inspections that could have otherwise been avoided.
Time is money. Quality must be assured. Companies must have such confidence in their supply chain that they can eliminate incoming inspections and even stockrooms.
Here are five suggestions for how to build a state-of-the-art quality program that allows you to do just that.
Definitions Matter
Quality Assurance (QA) is not the same as Quality Control (QC). QA is the work that helps prevent defects from happening, while QC is the practice that catches defects after they exist. The better you are at QA, the less effort and expense has to be spent on QC.
In my experience, traditional organizations are much more focused on executing QC by reviewing data and holding inspections, while more forward-thinking organizations deploy QA engineers to proactively collaborate with suppliers and prevent defects from arising in the first place.
Understanding that nuance between reactive and proactive as well as the implications are critical when determining your organization’s defect containment strategy.
Quality by Design, Not Inspection
Typically, QC inspection is used because an organization does not trust its suppliers or its own processes. In the case of incoming inspection, parts are purchased from suppliers earlier than needed to allow for both the inspection time and the time to replace or rework defects.
Any objective analysis of this process will tell you it’s bad design. Incoming QC inspection is cash spent too early on material and on activities non-essential to the organization’s core business activities. In lean-speak, it’s non-value-added waste.
The better option is to assess the supply chain to identify the potential for defects or liabilities, then work with suppliers to build in rigorous controls. Quality by design shifts the focus to building quality in and results in less wasted time and money.
Fewer Manufacturers Does Not Mean Fewer Quality Issues
Another common approach to QC is to limit suppliers. Organizations falsely believe that by restricting the number of suppliers, they will reduce defects. Unfortunately, this leads to two undesirable side effects.
First, parts have to be ordered in advance because suppliers want to manage their capacity and keep all their machines running. This usually extends lead time, restricting the ability to change product volumes or mix.
Second, it limits supply chain agility. The pandemic has reminded us that supply chains can be easily disrupted. Relying on a limited number of suppliers with long lead times diminishes an organization’s ability to be nimble in the face of challenges or disruptions.
Guided Expertise is a Game Changer
Product design and manufacturing is not a one-person exercise. It requires teams of people working in collaboration to realize the end goal.
Similarly, quality is a group effort. New Digital Manufacturing Ecosystems and platforms feature design for manufacturability (DfM) assessments that allow customers the opportunity to change part designs to increase the likelihood of success.
Engaging with your partners through these and other guided expertise programs can help bulletproof your zero-defect strategies while also limiting cost and effort.
Defects Happen, Have a Plan
Even an expertly designed, proactive plan with multiple suppliers and input from customers will produce a defective component once in a while. The key is to have a plan already in place to deal with it.
By having multiple qualified manufacturing partners, available capacity can be leveraged for priority or rapid replacement or reworking of issues. Organizations should engage with partners to turn problems into learning opportunities. By stepping back and taking a wider view, other potential defects can be eliminated.
These approaches can vary depending on your partners and the nature of your product. But ultimately, the goal is to allow for recovery without impact to project timelines or budget.
Looking ahead, as organizations around the world begin to restart or grow operations in the weeks and months ahead, quality will be a critical strategic consideration. Whether designing it into parts and systems or using it as an important criterion when selecting a partner, a proactive quality assurance stance will save time, money, and heartache.
David Woodward is the Director of Quality at Fictiv and brings a demonstrated history of success managing quality management systems across a diverse range of manufacturing industries. He is skilled in the areas of Environment, Health, and Safety (EHS), Employee Learning & Development, Quality Management, Knowledge Management, Manufacturing Management, and Product Safety Compliance. David holds a Master of Science (M.Sc.) focused in Advanced Manufacturing Systems from Brunel University, London.
Comments (0)
This post does not have any comments. Be the first to leave a comment below.
Featured Product
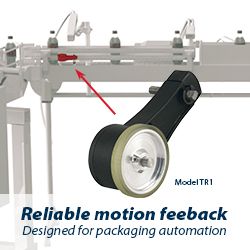