Desktop Metal Announces Highly Anticipated Release of Binder Jet 3D Printing Upgrade to Manufacture Reactive Metal Parts, including Titanium and Aluminum
First launched in 2020, the Production System P-1 metal binder jet 3D printer will now be offered with a Reactive Safety Kit that unlocks high-speed production of ultra-fine titanium and aluminum powders with critical safety features
Desktop Metal (NYSE: DM), a global leader in Additive Manufacturing 2.0 technologies for mass production, today announced the launch of a Reactive Safety Kit for the Production System P-1 — unlocking safe, high-speed binder jet 3D printing of both titanium and aluminum.
In development and testing for more than two years, the P-1 Reactive Safety Kit features ATEX-rated components, as well as critical hardware and software updates to ensure the highest level of safety. ATEX certification is given to equipment that has undergone rigorous testing outlined by European Union directives and is considered safe to use in specific environments with explosive atmospheres.
"Titanium and aluminum are two of the most frequently requested materials at Desktop Metal, and we're proud to say that we can now offer a commercial 3D printer with the necessary safety features to binder jet 3D print these materials," said Ric Fulop, Founder and CEO of Desktop Metal. "Based on our ongoing projects with major manufacturers, we know our technology is well on its way to unlocking new designs that deliver higher performance, weight reductions, and other benefits - all with our high-speed 3D printing technology that makes Additive Manufacturing more affordable for production volumes. We are diligently following our roadmap to deliver high-volume production of these materials on our largest printers in the future."
A number of DM customers are already binder jetting titanium and aluminum today. "Our team at TriTech has found binder jetting to be a good complement to our metal injection molding (MIM) business," said Robert Swenson, owner of TriTech and also the former owner of AmeriTi. Swenson is a graduate of Purdue University with a degree in Metallurgical Engineering and an MBA from Harvard Business School. "With binder jet 3D printing, titanium production of even the most complex geometries can be greatly simplified and achieved at a lower cost. We're excited to offer this cutting-edge manufacturing technology to our customers."
Additionally, Desktop Metal has several significant projects in development with major manufacturers using a variety of specialty materials developed by Kymera International, including titanium and aluminum. "Since formalizing our partnership in 2021 through a Joint Development Agreement, we have been excited to work closely with Desktop Metal to develop a range of metal powder solutions optimized for the binder jetting process," said Joe Croteau, Technology Manager - Specialty Materials with Kymera. A leading global supplier of specialty materials and surface technologies, Kymera International has contributed decades of metallurgical expertise and process knowledge to offer sintered aluminum alloys with excellent performance. "Kymera's well-established relationships with a diverse group of customers has given us the opportunity to focus on the needs of high-volume manufacturers, and we are proud to now have a commercially established solution. Over the past two years, we've successfully printed a variety of aluminum geometries and part sizes through multiple programs."
The Desktop Metal Production System P-1, as well as an array of titanium and aluminum designs, including those 3D printed by TriTech, will be on display June 25-27 at RAPID + TCT at the Los Angeles Convention Center. DM will be located in Booth No. 2139.
Binder Jetting Offers Wide Range of Benefits
Binder Jetting is widely regarded as the fastest method of metal 3D printing for high-volume output. It uses a digital file to quickly inkjet a binder into a bed of powder particles such as metal, sand, or ceramic to create a solid part, one thin layer at a time. When printing metals, the final bound metal part must be sintered in a furnace to fuse the particles together into a solid object.
Binder jet 3D printing, compared to both traditional manufacturing and other forms of 3D printing, enables manufacturers to more affordably produce complex parts with unique benefits, such as size and weight reductions, part consolidation, and performance improvements.
Because of the broad material flexibility of binder jet 3D printing, Desktop Metal employs a tiered qualification system for production of powdered materials:
Qualified Materials come with complete printing and sintering profiles with fully characterized material and mechanical properties
Customer-Qualified Materials have printing and sintering profiles developed by or in partnership with customers and/or partners with material and mechanical properties suitable for specific applications
R&D Qualified Materials have demonstrated binder and process compatibility with our printers, with final printing and sintering profiles under development by DM or our customers
In all, more than 30 metals and ceramics are qualified on DM printers. The Production System P-1 is qualified to 3D print 17 metals, including stainless steels, low-alloy steels, copper alloys, tool steels, nickel-based alloys, precious metals, and more.
With today's announcement, titanium (Ti64) is now classified as Customer-Qualified on both the P-1 and X-Series models when upgraded with an inert atmosphere and other safety features. Aluminum is now classified as Customer-Qualified on the X-Series and R&D Qualified on the P-1 when upgraded with an inert atmosphere and other safety features.
If you are a manufacturer or research lab interested in learning more about 3D printing reactive materials on the P-1 or another Desktop Metal printer, visit TeamDM.com/Reactive3DP.
About Desktop Metal
Desktop Metal (NYSE:DM) is driving Additive Manufacturing 2.0, a new era of on-demand, digital mass production of industrial, medical, and consumer products. Our innovative 3D printers, materials, and software deliver the speed, cost, and part quality required for this transformation. We're the original inventors and world leaders of the 3D printing methods we believe will empower this shift, binder jetting and digital light processing. Today, our systems print metal, polymer, sand and other ceramics, as well as foam and recycled wood. Manufacturers use our technology worldwide to save time and money, reduce waste, increase flexibility, and produce designs that solve the world's toughest problems and enable once-impossible innovations. Learn more about Desktop Metal and our #TeamDM brands at www.desktopmetal.com.
Featured Product
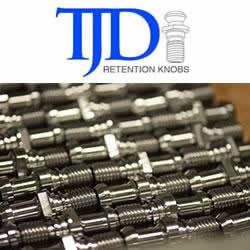
T.J. Davies' Retention Knobs
Our retention knobs are manufactured above international standards or to machine builder specifications. Retention knobs are manufactured utilizing AMS-6274/AISI-8620 alloy steel drawn in the United States. Threads are single-pointed on our lathes while manufacturing all other retention knob features to ensure high concentricity. Our process ensures that our threads are balanced (lead in/lead out at 180 degrees.) Each retention knob is carburized (hardened) to 58-62HRC, and case depth is .020-.030. Core hardness 40HRC. Each retention knob is coated utilizing a hot black oxide coating to military specifications. Our retention knobs are 100% covered in black oxide to prevent rust. All retention knob surfaces (not just mating surfaces) have a precision finish of 32 RMA micro or better: ISO grade 6N. Each retention knob is magnetic particle tested and tested at 2.5 times the pulling force of the drawbar. Certifications are maintained for each step in the manufacturing process for traceability.