Traditionally, our manufacturers have relied on hydraulic-powered injection moulding machines in their operations. However, the industry is now at a crossroads, faced with the imperative to embrace technological advancements for sustainability and cost-effectiveness.
Investing in the UK’s injection moulding sector - The case for all-electric machines and robotic integration
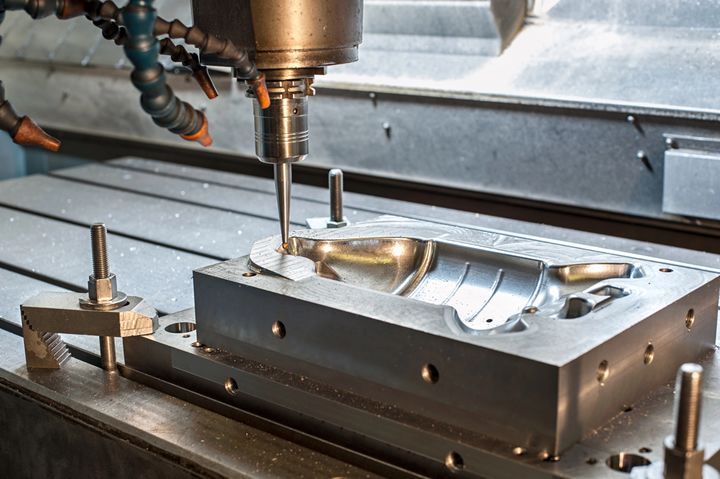
Nigel Smith, Managing Director | TM Robotics
The UK plastics industry plays an important role in the country’s economic engine, generating over £25 billion annually and employing approximately 155,000 people. In this article, Nigel Smith, managing director of TM Robotics, the international distribution partner of Shibaura Machine and the UK and Ireland distributor of its injection mould machines, explores the changing landscape of plastic's injection moulding sector and argues the case for investment in new technologies, both for better operational efficiency and improved sustainability.
Injection moulding applications have long played a key part in the UK’s manufacturing industry, producing everything from medical components, automotive parts, food containers, packaging items and much more. Traditionally, our manufacturers have relied on hydraulic-powered injection moulding machines in their operations. However, the industry is now at a crossroads, faced with the imperative to embrace technological advancements for sustainability and cost-effectiveness.
The case for all-electric
One notable observation is the prevalence of hydraulic legacy equipment that is still being used by UK manufacturers. The TM Robotics’ injection moulding servicing department has witnessed this first hand and regularly visits manufacturing sites to service and maintain Shibaura Machine’s own hydraulic injection mould machines — some of which have been in action for up to three decades. On one hand, it is a testament to the resilience of these machines, but the industry must consider the environmental downsides of this ageing equipment.
The injection moulding process is responsible for up to 90 per cent of the Global Warming Potential (GWP) in the entire mould lifecycle. Recognising this, TM Robotics has championed for investment in all-electric injection mould machines to replace older, more energy-intensive models.
The flagship all-electric range from TM Robotics is the SXIII all-electric series from Shibaura Machine. Shibaura Machine is the new name for Toshiba Machine — the Japanese manufacturer of industrial robots and injection mould machines. The SXIII range boasts faster injection speeds, enhanced sustainability and a streamlined design when compared to its hydraulic predecessors. What’s more, despite the perception of higher costs for all-electric machines, this range can improve cost efficiency by lowering the cost-per-part.
This was demonstrated by TM Robotics’ customer Lotan, a manufacturer of plastic containers based in Leicestershire, UK. Lotan’s production facility exclusively uses all-electric injection mould machines from Shibaura Machine. The SXIII provides significantly faster injection speeds than traditional moulding equipment, providing 35 per cent faster cycle times than conventional hydraulic servo IMMs.
Robotic integration
Another area of debate in the injection moulding world is robot integration. The UK seriously lags behind other developed countries for its number of robot installations. That’s not just for the world of injection moulding, but in the UK manufacturing sphere more widely. In fact, the International Federation of Robotics (IFR) reports that the UK has just 101 robots per 10,000 employees — rookie numbers compared to competitors in the US, China and Germany.
Due to this lack of uptake, UK industry is missing some of the potential benefits of industrial robots, including improved productivity, efficiency and throughput. As the premier distributor of Shibaura Machine robots in the UK, the TM Robotics team has spotted glaring opportunities for the injection moulding sector to reap the rewards of robotic automation.
The most obvious application for robots in mould machine shops is for the loading and unloading of injection mould machines. However, many end users currently have relatively low robotic ability, having traditionally chosen Cartesian X-Y gantry style robots to unload injection moulding machines.
A key goal of TM Robotics is to introduce the UK’s injection mould shops to the wider possibilities of robots in our injection moulding applications. As part of our portfolio of Shibaura Machine industrial robots, we can offer 6-axis, Cartesian and SCARA robots with a range of advanced features and benefits for injection moulding operations. This could be as simple as providing ceiling mounted SCARAs for loading and unloading in compact work areas, right through to engineering bespoke automation set-ups for both up and downstream in the production line.
A common misconception of injection mould shops is that these automation projects require hefty investment into systems integration. However, that is not always the case. By opting for an automation package from a single manufacturer, like Shibaura Machine, facilities managers can bypass complex engineering by choosing a fully integrated injection mould machine and robot package.
There are over 5,800 companies operating in the UK plastics industry, contributing £25 billion to our economy each year. As a key player in Britain’s manufacturing sector, injection mould shops must embrace technological advancements in injection moulding machinery and accompanying automation for improved profit, productivity and sustainability.
The content & opinions in this article are the author’s and do not necessarily represent the views of ManufacturingTomorrow
Comments (0)
This post does not have any comments. Be the first to leave a comment below.
Featured Product
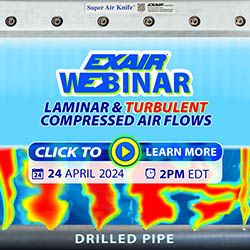