In this blog post, we will explore the various facets of this issue and understand why investing in effective communication is a crucial consideration for manufacturing plants.
The Cost of Bad Communication in Manufacturing Plants
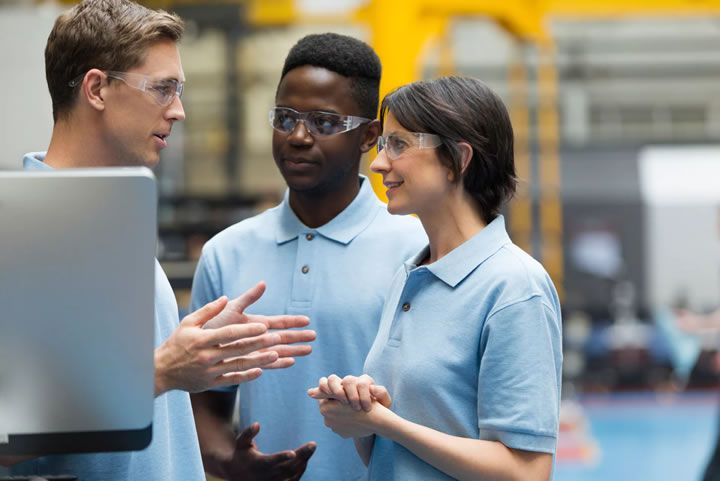
Article from | EviView
In manufacturing, efficient communication is not just a desirable attribute; it’s an absolute necessity. The seamless flow of information within a manufacturing plant can significantly impact productivity, product quality, employee morale, and the overall bottom line. Conversely, the cost of bad communication can be staggering, both in financial terms and in terms of the long-term health of the organization. In this blog post, we will explore the various facets of this issue and understand why investing in effective communication is a crucial consideration for manufacturing plants.
Production Delays
One of the most immediate and obvious consequences of bad communication in a manufacturing plant is production delays. When critical information fails to reach the right people at the right time, it can lead to bottlenecks, downtime, and missed deadlines. Delays in production not only impact customer satisfaction but also increase operational costs as resources are underutilized and overtime pay may be required to catch up.
Quality Control
Quality control is paramount in manufacturing, and bad communication can undermine it significantly. Without clear communication channels, employees may not be aware of changes in production processes, quality standards, or product specifications. This can result in defective products, increased rework, higher scrap rates, and the potential for costly recalls or customer returns.
Employee Morale and Retention
Effective communication is not just about transmitting information; it’s also about fostering a positive work environment. When employees feel that their voices are not heard or that they are not well-informed about company policies and decisions, morale can suffer. It is detrimental to employee morale when employees don’t feel heard or are unaware of company policies and decisions. Consequently, it can lead to increased turnover rates, which come with their own set of recruitment and training costs.
Safety Risks
Safety should always be a top priority in manufacturing, and bad communication can pose significant safety risks. Failure to communicate essential safety protocols, hazards, or emergency procedures can result in accidents, injuries, and even fatalities. These incidents not only have devastating human costs but also legal and financial ramifications for the organization.
Inventory Management
Manufacturing plants often rely on efficient inventory management to minimize storage costs and maintain just-in-time production. However, when communication breakdowns occur between production and supply chain teams, inventory levels can become inaccurate. Overstocked or understocked items can lead to financial losses due to carrying costs or production halts when necessary materials are unavailable.
Decision-Making
In an era of data-driven decision making, timely access to accurate information is crucial. Bad communication can lead to confusion and misinformation, making it difficult for leaders to make informed choices. This can result in poor strategic decisions, missed opportunities, and financial losses in the long run.
Reputation Damage
Lastly, the cost of bad communication extends beyond the internal operations of a manufacturing plant. Negative publicity or customer complaints stemming from communication failures can damage the company’s reputation. Rebuilding trust and credibility can be a costly and time-consuming endeavor.
Conclusion
The cost of bad communication in manufacturing plants is multifaceted and can have far-reaching consequences. From production delays and quality control issues to safety risks and damage to the company’s reputation, the impacts are significant. To mitigate these costs, manufacturing plants should invest in robust communication systems, foster a culture of open and transparent communication, and provide training and tools to enhance communication skills at all levels of the organization. In doing so, they can not only reduce costs but also position themselves for long-term success in a highly competitive industry.
The content & opinions in this article are the author’s and do not necessarily represent the views of ManufacturingTomorrow
Comments (0)
This post does not have any comments. Be the first to leave a comment below.
Featured Product
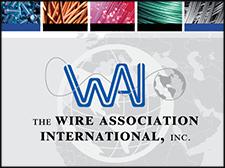