This article will explore what manufacturing-specific ERPs are, how they differ from traditional ERPs, and the multifaceted benefits they offer to manufacturing businesses.
Understanding the Power of Manufacturing-Specific ERPs: A Deep Dive into Their Unique Benefits and Differences from Traditional ERPs

Written and Researched by Charlie Green Senior Research Analyst | Comparesoft
In the fast-paced and increasingly competitive world of manufacturing, leveraging technology to streamline operations and optimise efficiency is not just a luxury – it's a necessity. Among the most transformative technological tools are Enterprise Resource Planning (ERP) systems, particularly those tailored for manufacturing. This article will explore what manufacturing-specific ERPs are, how they differ from traditional ERPs, and the multifaceted benefits they offer to manufacturing businesses.
What Are Manufacturing-Specific ERPs?
Manufacturing ERP software is a specialised program designed to plan, manage, and deliver enterprise resources in manufacturing settings. Distinctly set apart from standard ERP systems, which offer a broad-strokes approach to business operation management, manufacturing ERPs are intricately customised to address the nuanced and multifaceted needs inherent to the manufacturing sector. What sets these systems apart is their ability to seamlessly marry core business processes – such as finance, HR, and customer relationship management – with the specific operations central to manufacturing, like production planning, shop floor management, and quality control.
This integration is not merely a superficial overlay of manufacturing functionality onto a generic business platform. Instead, manufacturing ERPs are meticulously architected to ensure that every element of the manufacturing process – from the initial procurement of materials to the final stages of product delivery – is intricately woven into the overall business strategy. The result is a harmonised, central system that provides a unified view of all operations, ensuring that decision-makers have a comprehensive and real-time understanding of every facet of their business.
The Key Differences Between Manufacturing ERPs and Traditional ERPs
Traditional ERPs serve as the backbone for a variety of business functions, forming an integrated network that supports Accounting, Customer Relationship Management (CRM), Sales, Purchasing, and Human Resources. While these systems are adept at providing a comprehensive view of these general business operations, they often lack the depth and specificity required by the manufacturing sector.
In contrast, Manufacturing ERPs are not just an extension of these capabilities but a reimagined solution crafted specifically for the manufacturing landscape. These systems do more than just include the standard business functions; they extend their reach into the heart of manufacturing operations. Specialised modules such as Production Management, Warehouse Management, Quality Management, Supply Chain Management, and Material Requirement Planning (MRP) are not mere add-ons but integral components of these systems.
One of the most salient differences between the two lies in the realm of customization. Manufacturing ERPs are innately attuned to the needs of manufacturing businesses, designed from the ground up with this sector's complexities and demands in mind. This inherent design focus means that manufacturing ERPs are typically equipped with deep, industry-specific functionalities right out of the box. This includes robust inventory control mechanisms and seamless integration with shop floor machinery—features that are seldom found in their generic counterparts.
Benefits of Implementing a Manufacturing-Specific ERP
Manufacturing-specific ERPs offer several benefits that are unique to the manufacturing industry. These benefits include enhanced production efficiency, optimised resource management, and improved quality control:
Enhanced Production Efficiency
A pivotal advantage of implementing a manufacturing-specific ERP system is the substantial enhancement in production efficiency it brings to a manufacturing company. By centralising data, these systems provide a comprehensive oversight of the production process, enabling manufacturers to pinpoint areas for improvement. This streamlined approach to data management and process monitoring results in notable gains in production speed, a reduction in waste, and a corresponding increase in profitability.
Key to this efficiency is the ERP system's capacity for real-time production monitoring. This functionality marks a significant evolution from older, manual tracking methods. With an ERP system, manufacturers have a clear, real-time view of their manufacturing orders and production schedules from a centralised dashboard. This immediate visibility allows for swift identification and resolution of potential bottlenecks or delays. Such prompt responsiveness is crucial in maintaining the smooth flow of production operations.
Optimised Resource Management
Manufacturing ERPs revolutionise production planning. They equip manufacturers with the ability to accurately forecast when inventory will be required in the production process. This capability is pivotal in preventing the accumulation of obsolete stock, a common yet costly issue in the manufacturing industry. For instance, effective inventory management, as facilitated by ERP systems, can lead to significant cost savings. ERP systems track the movement of raw materials and finished goods in real-time, reducing the risks associated with overstocking or understocking. Automated reordering functions ensure that essential materials are always available, preventing production delays and ensuring a smooth production flow.
The real-time production monitoring feature of manufacturing ERPs is also instrumental in resource optimisation. It allows for instant adjustments in resource allocation, enhancing overall operational efficiency. For example, an underutilised machine can be swiftly reassigned, minimising downtime. Furthermore, the automation of work order generation, based on customer orders or sales forecasts, streamlines the production initiation process. By optimising resource allocation, these systems ensure that the necessary resources are available when needed, contributing to efficient production scheduling and timely order fulfilment.
Improved Quality Control
Manufacturing ERP systems are pivotal in enabling manufacturers to establish and maintain a robust quality control system. With the advent of automated production technology, the manufacturing landscape has evolved rapidly, necessitating more efficient and effective quality assurance measures. According to Quality Magazine, almost 60 percent of producers have recognized an increased significance in quality assurance over the past year, underscoring its growing importance in the Industry 4.0 era.
The quality of products is intrinsically linked to the continuity and efficiency of manufacturing processes. Manufacturers with well-structured shop-floor workflows are more likely to produce durable and marketable goods. Conversely, those with inefficient workflows face a higher risk of quality issues. Manufacturing specific ERP systems support data-backed process monitoring programs, leveraging real-time information and dashboard features to provide critical workflow insights. This data enables operational stakeholders to assess workflow quality and identify potential process improvements, thereby enhancing the overall quality of the products manufactured.
In addition to improving quality control directly, manufacturing ERP systems also bolster traceability and compliance capabilities. ERP technology supports key processes such as raw ingredient testing and automated alerts for shop-floor leaders about required government-mandated audits and inspections. This level of traceability is essential for meeting regulatory requirements and ensuring product safety. In the event of any suboptimal products slipping through production, ERP systems allow manufacturers to quickly access historical production data for immediate quality control action. Furthermore, ERP systems simplify the compliance review process by generating automated reports, streamlining what would otherwise be a cumbersome task for production leaders
Conclusion
The adoption of manufacturing-specific ERPs represents a strategic investment for manufacturing businesses aiming to stay ahead in a highly competitive and evolving industry. By offering tailor-made solutions that address the unique challenges of manufacturing operations, these systems not only streamline processes but also provide a platform for innovation and growth. As the manufacturing landscape continues to evolve, the role of manufacturing ERPs in driving efficiency, productivity, and competitive advantage cannot be overstated. The insights from sources like Comparesoft, ERP Cloud Blog, and Kerr Consulting underscore the transformative impact of these specialised systems in the manufacturing sector.
For manufacturing businesses looking to enhance their operational efficiency and adapt to the dynamic business environment, the integration of a manufacturing-specific ERP is not just a step but a leap towards future-proofing their operations.
The content & opinions in this article are the author’s and do not necessarily represent the views of ManufacturingTomorrow
Comments (0)
This post does not have any comments. Be the first to leave a comment below.
Featured Product
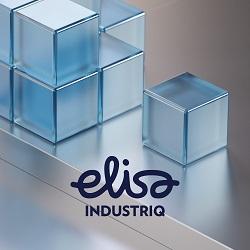