For drone manufacturers, 3D printing can improve lead times, reduce costs, and gain more control over workflows with stereolithography (SLA) and selective laser sintering (SLS) 3D printing technology.
3D Printing in Drone Manufacturing
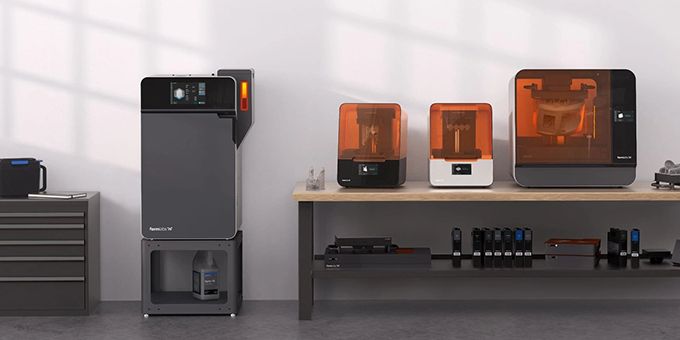
Q&A with Michael Baker, Global Head of Brand & Communications | Formlabs
Tell us about yourself and your role with Formlabs.
I am an experienced marketing leader with a background in content and communications. I utilize content strategy and SEO tactics to drive organic traffic or establish an overarching communications strategy from awareness to sales enablement. Blending my journalistic background, tech marketing expertise and team leadership & development skills to consistently push forward corporate strategies.
The Drone industry is growing rapidly, how is 3D printing being used to aid this rapid growth?
3D printing is enabling drone manufacturers to design and produce rugged and lightweight drones at a faster and more affordable rate. This is because in-house 3D printing allows for quicker production of prototypes and end-use parts at a lower cost of labor and materials, which ultimately provide clients with the best solutions via streamlined product development processes. For drone manufacturers, 3D printing can improve lead times, reduce costs, and gain more control over workflows with stereolithography (SLA) and selective laser sintering (SLS) 3D printing technology.
How are you seeing 3D printing improving output?
The use of 3D printing in drone manufacturing enables designers to create parts in-house within days rather than weeks while potentially saving millions of dollars, leading to a better product at a greater output level.
With an in-house 3D printer, drone manufacturers can work with clients on specific design projects to ensure accuracy in part production through quick design changes and part iterations. 3D printing enables drone manufacturers to easily try different versions of part designs, and as a project may change, it is simple to print a new design with minimal effort and downtime.
Cutting out the middle man of part production also enables drone manufacturers to work more efficiently and closely with clients to meet their exact design needs on a quicker timeline.
How does 3D printing lower the cost of drone part production?
3D printing can lower the cost of drone part production by reducing labor costs with streamlined, in-house workflows using affordable desktop 3D printers and affordable materials that can produce durable parts. Using an in-house 3D printer can allow manufacturers to increase the volume of part production and optimize their use of material. It can also enable them to produce plastic parts without needing to produce injection molds, which can be expensive, and significantly lengthen the timeline for completion.
How are companies using 3D printing to improve drone design?
3D printing improves drone design by enabling rapid prototyping for intricate, complex parts, with a high-quality finish for unique designs. Drone additions such as brackets can be prototyped and tested for strength, feel, weight, fit, and usability to make sure that the final solution they send to clients is high quality.
The 3D printing workflow allows manufacturers to solve unique client requirements, develop new products, and improve on designs at a much faster rate. In-house 3D printing can speed up development timelines, allowing teams to work with customers more closely to perform unique projects for clients.
Can you share some examples of drone manufacturers using 3D printing for drone production?
Drone specialist heliguy invested in the Formlabs Form 3L large-format SLA 3D printer and the Fuse 1 benchtop SLS 3D printer to design lightweight and durable parts that they wouldn't have been able to otherwise within days, rather than weeks. Read more about how heliguy uses 3D printing here.
Drone manufacturer Nextech uses the Fuse 1+ 30W SLS printer to prototype and manufacture rugged drones with one streamlined workflow to solve unique client requirements in climate science, agriculture, and more. The use of in-house 3D printing allows Nextech to develop new products, and improve on designs at a much faster rate in comparison to outsourcing. Read more about how Nextech uses 3D printing here.
Skydio is setting the standard for AI-powered drone systems by using five Form 3+ SLA printers to design advanced autonomous flight drones and new Dock products for use in energy utilities, transportation, public safety, environmental research, and more.
The content & opinions in this article are the author’s and do not necessarily represent the views of ManufacturingTomorrow
Comments (0)
This post does not have any comments. Be the first to leave a comment below.
Featured Product
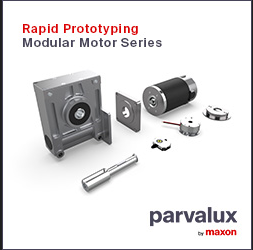