We’ve been in a phase of connecting machines through IIoT and the next step is expanding that connection to reduce reliance on workers. Right now, there are 2.1 million manufacturing jobs unfilled.
How Digital Manufacturing Technology Can Fill the Talent Shortage
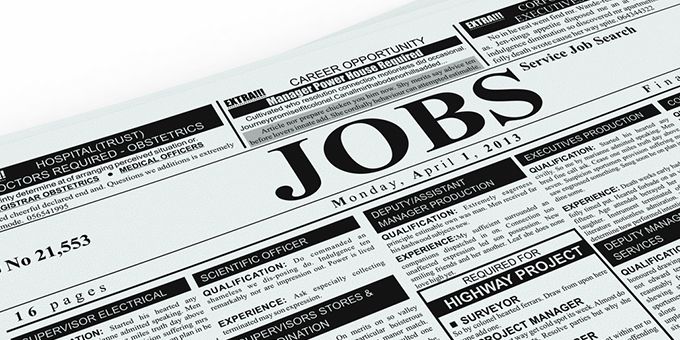
Q&A with Wes Turner, Senior Management Consultant | Dploy Solutions and TBM Consulting
Tell me about Dploy Solutions.
Dploy Solutions offers a suite of scalable cloud-based digital manufacturing software and IIoT platform solutions designed and priced for small to mid-sized manufacturers and distributors looking to grow their businesses. Our products bring data together from your top floor to your shop floor, including machine data, and link your organization’s strategic goals with your operational excellence activities and digital manufacturing technologies. This integration gives manufacturers the tools they need to quickly make smart, informed decisions at all levels of the organization, achieve operational and financial goals faster, and build a sustainable competitive advantage in the marketplace.
What is your role at Dploy Solutions?
I’m a senior management consultant with Dploy Solutions and TBM Consulting, and I work directly with clients to help improve their processes, implement managing for daily improvement, or MDI, systems and improve their hour-by-hour data from the manufacturing floor. We used to do all of that manually. Now we’re using Dploy to manage those systems so that the data they’re pulling from the shop floor can be managed from a cloud-based system, rolled up into digestible reporting and given to management to look at, and make changes and decisions based on that data.
How has COVID-19 impacted the talent shortage?
It was bad before COVID, and now it’s even worse. Most of our clients say they just can’t get enough people to come through the door. And there are a variety of reasons: they’re afraid for their health, they’re getting generous unemployment benefits, or they’re having to stay home and take care of children because schools are closed. Many clients are also struggling with delivery issues, keeping up with demand, and having a hard time running their lines as usual because of new COVID requirements. For example, one client had to redesign their production lines to accommodate social distance guidelines. Absenteeism is also an issue, and sometimes they have people on the line become infected and they have to shut down the entire line and sanitize before getting back to work. It’s causing a lot of productivity issues.
What are some of the top ways to increase productivity despite the talent shortage?
First, I would say to automate processes wherever it makes sense. For example, material handling is an especially big opportunity for automation, so look at ways in which you can move material more efficiently.
You can also look at rebalancing your production lines to accommodate for the shortage of resources. In fact, look at everything in the facility to see if there is perhaps a better way to design things that would improve processes and productivity.
Implementing a KPI management strategy is a great way to identify areas for improvement, and it gives you valuable data to analyze what’s working and what’s not.
Cross-training and upskilling your people is also a smart strategy. This way, if you have shortages in one area, you’ll have the flexibility to move people around to fill those roles. Of course, this means you’ll need to reskill and deploy people very quickly. Tools like digital standard work can help you do this effectively without impacting productivity. By capturing processes on video to document the standard work, you can use this to train people and measure their performance, instead of having to pull another employee off the line to train someone else, which consumes double the resources. With visual knowledge systems, you don’t have to take the best person off the line and bog them down with training.
What are critical signs for manufacturers to look for to know that it is time to invest in automation?
First is a decline in productivity. Are you missing deliveries or unable to fulfill orders? Are you having to turn down orders because you don’t have the capacity or is your reputation suffering?
Second, are there safety or ergonomic issues? Especially with the talent shortage many companies are facing, they have people working more hours, which creates a safety risk due to repetitive stress injuries, fatigue, etc.
Finally, one of the biggest issues we’re seeing with our clients right now is that many are willing to pay more to get people to come to work, including higher hourly wages, signing and retention bonuses, etc. But all of this changes your cost structure and erodes profitability. Rather than adding staff, it might be better economically to invest in automation, so you don’t incur that ongoing increase in cost.
What do manufacturers need to consider while determining if automation is right for them?
One of the biggest considerations is cost and ROI from a personnel perspective, but also consider equipment obsolescence. Are you spending a lot of money maintaining old equipment? Is it always breaking down or does it require a lot of people to run or maintain it? Rather than try to automate some part of that process, it might be better to just replace the antiquated machine.
On the other hand, if you replace it with new equipment, will that be beneficial in terms of cost efficiency? Will it cost more to perform preventative maintenance? Do you have the right skills? For example, your current equipment might require three operators. But if the new one requires two operators plus one maintenance operator, there’s no ROI. A lot of companies fail to fully account for the overall operational cost of their equipment.
Another area to consider is material handling. Aside from maintenance—the equipment itself might be fine—maybe it requires a lot of people to move material, to load and unload the equipment. This is a perfect opportunity for automation, to either reduce the need for human intervention or to assist the humans in doing their job. Automating material handling can address safety and ergonomic issues and substantially increase efficiency and productivity.
Finally, you have to consider whether you have the resources to support automation. It requires specialized skills, and if you don’t have them on staff, you either need to hire them—which isn’t easy right now—or you’ll be dependent on the vendor for service, which isn’t cost effective either. Automation isn’t always the immediate solution. Sometimes the answer to whether you should automate is “Yes, but not right now.”
What do you believe the future of manufacturing technology and machine learning will look like in the next 5 years? How about 10?
Skynet won’t be with us anytime soon, but I do see us headed quickly toward a world of connecting workers to machines and supply chains. We’ve been in a phase of connecting machines through IIoT and the next step is expanding that connection to reduce reliance on workers. Right now, there are 2.1 million manufacturing jobs unfilled. It was a problem before COVID, but COVID exacerbated the talent shortage. Companies are already looking at ways to overcome the deficit so they actually don’t need to hire back the workers they’ve lost.
For example, co-bot or robotic assist technology leverages virtual or augmented reality to help maintenance staff make a repair. With virtual step-by-step guidance, or a holographic wiring diagram overlaid on the machine, it makes troubleshooting and repair much faster and efficient. I expect we’ll soon see Google Glasses-type of equipment become commonplace in the factory of the future.
Another interesting development is the integration of video and AI with IIoT. By using cameras to capture process video, these systems can document events that triggered equipment failures—what happened right before that machine jammed, for example—to make troubleshooting much, much faster.
Next, we’ll be able to tie digital standard work to KPI management and even personnel performance reviews. We have the data, it’s just a matter of integrating it so that it populates into personnel files. Then we can use detailed analytics around all of this to get better insights into what’s really happening in the business.
These are all part of the move toward Lean 4.0, and these technologies aren’t as expensive as you might think. Today’s younger generations have raised on digital technology, gaming and controllers, so they’re used to this type of digital environment. Marketing your facility as a modern, digitized factory of the future can combat the image of manufacturing as a dirty, antiquated, manual job and aid in recruiting.
The content & opinions in this article are the author’s and do not necessarily represent the views of ManufacturingTomorrow
Comments (0)
This post does not have any comments. Be the first to leave a comment below.
Featured Product
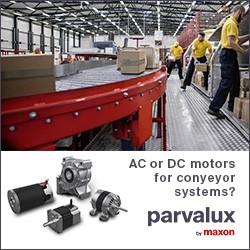