Deploying RTUs on industrial assets is an important element of capturing, interpreting and using big data from an industrial process. In this article, Jean Burton, technical sales support manager at Ovarro looks at how RTUs play a key role in accessing big data.
How to Make Sense of Big Data - RTUs and Process Control Applications
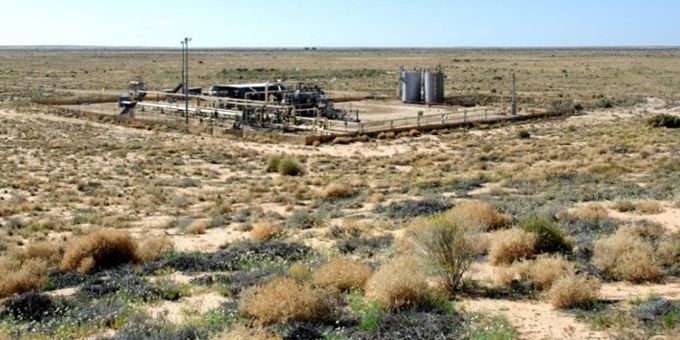
Article by | Ovarro
The principle benefit of being able to remotely monitor an asset using an RTU is that it allows operators to regularly verify from a laptop or smart device that is operating withing agreed parameters. RTUs capture big data so that operators can monitor all critical applications in a process, ranging from hours of run time, oil temperature, through to faults and load levels. They monitor the external environment, too; for example, local temperature. This can be particularly useful in harsh environments as it allows engineers to take pre-emptive actions to prevent overheating or freezing.
The alternative is to send an engineer for routine inspection which in a remote location or expansive industrial site can be hazardous and time consuming. In some cases, it will require a second visit because they will only be able to identify faults when on site and then must source a replacement part back at base. Knowing this information beforehand can save valuable time by carrying out maintenance in a single visit.
RTUs, such as our TBox, act as both the site controller and the site communications gateway. They collect data directly, or provide a secure VPN, to PLCs used to monitor the asset. The collected data is then made available to the operators who can issue commands back to the RTU to control the asset. In parallel, the RTU relays key information to the asset owner or maintenance partner. With its ability to report alarms and historical data via email, SMS and FTP, it means nominated personnel are always being updated on its status.
RTUs on the journey to the Industrial Internet of Things (IIoT)
Operating an aged or geographically remote asset can make it a challenge to access IIoT. The physical constraints of not being on the ‘net’ is the first hurdle, whilst the age of some gensets means that operators believe that they must undertake considerable investment to replace ‘old’ assets with new, ‘smart’ versions.
The best way of thinking about RTUs is that they are ‘mini-computers in the field’, so adding one to an older genset can turn it into a ‘smart’ asset. In terms of benefits, RTUs help optimise industrial assets in both near and remote applications by providing greater monitoring and control. As such, they are a powerful, cost effective method of getting on the IIoT journey.
Once fitted, an RTU allows organisations to monitor and control processes wherever they are in the world. RTUs facilitate communication to local sensors and/or to an interface at a central monitoring location. At the same time, they provide remote access to control and monitor through standard HTML pages.
Benefits of RTUs
Where maintenance of assets is factored out, knowing the status of the device before the end customer ensures better outcomes for all project partners. Where the asset could potentially develop a fault that prevents it from operating, the RTU allows maintenance teams to take preventative action.
Another useful feature is being able to control the asset from a smart device to ensure that it is fully functional. Again, without an RTU, it would require a visit to the site by an engineer. It is already possible to fit GPS modules to the RTU to provide a positioning of the system, which can be useful in terms of movement of smaller assets.
RTUs can also help companies meet their environmental commitments. With a growing focus on sustainability, ‘big data’ captured using RTUs allow accurate monitoring of emissions. In Asia, our TBox RTU technology monitors diesel generator systems 24/7, providing emissions data to a central reporting location. The centralized data can be accessed by the wider community through an Air Quality Index app on smart devices as a means of keeping their energy providers in check. In addition, for the benefit of the owner, the RTUs monitor the generator health, by tracking exhaust temperatures, heater exchange throughput and oil quality as part of proactive maintenance measures. Monitoring fuel use also benefits efficiency management and deters fuel theft.
We can see that deploying RTUs on industrial assets is an important element of capturing, interpreting and using big data from an industrial process. They give you full control of the asset, wherever it is located geographically, including remote, harsh environments. Once in place, the RTU gathers operational data and transmits it to a dashboard on a smart device or stores it in the cloud for trending and future analysis.
The content & opinions in this article are the author’s and do not necessarily represent the views of ManufacturingTomorrow
Comments (0)
This post does not have any comments. Be the first to leave a comment below.
Featured Product
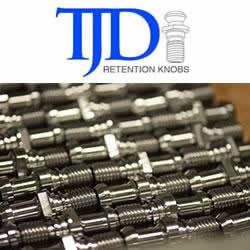