Fuel-flexible gas turbines from MAN Energy Solutions combine high efficiency with low emissions: these pioneering energy supply solutions are an ideal choice for municipal utilities and industrial applications.
Firing Up Enthusiasm for New Power Technologies
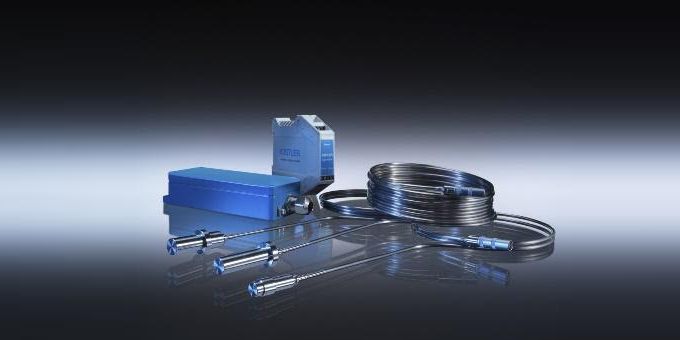
Case Study from | Kistler Group
During the development phase and also in the end product, high-temperature pressure sensors from Kistler deliver valuable real-time data to optimize the combustion process.
The changeover to energy supply solutions that deliver maximum efficiency while protecting the environment is one of the greatest challenges facing humanity in the 21st century. Resources have to be developed and emissions must be reduced against a background of continuously rising demand for energy. Gas turbines play a key part in tackling this challenge: they offer the ideal solution, especially in situations where both power and heat are required – as is often the case in municipal utilities or industrial settings. And in the future, it will become increasingly possible to operate gas turbines with hydrogen instead of natural gas, giving them a better environmental footprint and more compatibility with the desired energy mix.
More sustainable gas turbines of this sort with very low emission values are developed and manufactured at MAN Energy Solutions (MAN ES) in Oberhausen, Germany. The company's Turbomachinery Division, which is based here, traces its origins to the “Gute Hoffnungshütte” (or GHH) which at one time was Europe's largest machinery and plant construction enterprise: GHH began its iron smelting activities as long ago as 1758. Nowadays, some 1,800 employees at Oberhausen work in the competence centers for gas turbine development and production, and in the firm's extensive testing and service operations. On-site facilities include testing of complete gas turbine-compressor trains – the use of gas turbines to drive compressors (on gas pipelines, for example) is another key application area for this technology.
Integrated sensor technology monitors the combustion process
Dr. Bernhard Ćosić, who has been working at MAN Energy Solutions since 2015, leads the company's Gas Turbine Combustion Group and is a key player in the development of the MGT6000 series as well as the new MGT8000 series. Commenting on market trends, he says: “Our gas turbines, which deliver electrical power of between six and twelve megawatts, offer a far more sustainable solution for electricity and heat production than power plants that operate with diesel, coal or heavy fuel oil. Especially in situations that require not only power but also high-temperature heat – in paper production, for instance, or in the food industry – gas turbines achieve very high levels of efficiency. But they can also be used for decentralized power generation, particularly in remote areas where access is difficult, because commissioning costs for gas turbines are many times lower than for large engines.”
To monitor the combustion process and implement other advantages such as fuel flexibility and real-time monitoring, MAN ES opted for Kistler as a development partner. Piezoelectric high-temperature pressure sensors (6021A) from Kistler are connected directly to the gas turbine control; they operate in continuous mode to supply a data feed about the combustion process. “As well as being very compact, these sensors can withstand extremely high temperatures. That means we can position them close to the flame and obtain precise and highly informative data – available to us and our customers 24/7 via the MAN CEON Cloud. In this way, the requirements for condition monitoring and predictive maintenance are met.”
Thermoacoustic high-temperature measurement technology
To monitor and analyze gas turbines, Kistler offers sensors with high-temperature capability that measure pressure fluctuations and acceleration. Key characteristics:
- Reliable performance in continuous operation at up to 700°C (up to 1,000°C for brief periods)
- Maximum possibilities for evaluation thanks to precision and high measurement resolution
- Customized solutions to optimize costs
- Optional certified explosion-proof versions (ATEX, IECEx) are available for applications in environments with explosion risks
Sensors from Kistler play a major part in controlling and monitoring the combustion process. Alongside emission reduction, fuel flexibility is a key factor here. The MGT6000 series, for example, features dual fuel capability: this means that operation with liquid fuels such as diesel is also possible in the event that no natural gas is available. As Ćosić points out, it is also possible to use shale and other gases and combustion gases that often occur as waste products: these contain high proportions of inert gas such as nitrogen or carbon monoxide, but still have some residual energy. “We optimize combustion processes so that no instabilities occur even when the fuel is changed over – and live data supplied by Kistler sensors helps us here.”
Hydrogen – the fuel of the future
Kistler collaborated with MAN ES to develop a customized electronic unit (the Signal Conditioning Unit) that simplifies the entire measuring chain and contributes significantly to cost optimization. “Throughout the entire period, we received vigorous support from the team headed by Marco Gnielka – and that helped us to arrive at what we see as the optimal solution,” Ćosić adds. “The initial challenges were soon overcome, and Christian Heer – my contact partner at Kistler – is a highly proficient expert on the technology. Although we come from different engineering backgrounds, we quickly developed a working relationship based on trust.”
The next step in the ongoing development of the gas turbine is to enable the use of variable gas mixtures with up to 100 percent hydrogen: this advance holds out the prospect of even cleaner combustion, with CO2 emissions approaching zero. MAN ES has commissioned the first MGT8000 in fall 2020 – right here in Sterkrade, a district of the city of Oberhausen, where it will serve the local municipal utility (EVO). “This new, ultramodern gas turbine can already be operated with a hydrogen share of 20 percent. This could be increased to 50 percent in the short term. And in the medium term, 100 percent will even be possible,” Ćosić explains. “Hydrogen is highly reactive, so it changes the combustion characteristic – the flame burns more quickly, so to speak. That means you have to readjust and optimize the system if there is a major increase in the percentage of hydrogen in the gas mixture. But there are no changes to the basic parameters such as power output and efficiency – operators can continue to use our gas turbines as usual.”
Given that gas turbines have life expectancies of 15 years or more, customers of MAN ES view investment protection as an important criterion. If increasing quantities of hydrogen are fed into the natural gas network in the future – or indeed if new, pure hydrogen systems come into being – measurement technology from Kistler will play its part in the evolution of gas turbines from MAN ES – and that applies to optimization of the combustion processes as well as maintenance and monitoring. Summing up, Ćosić comments: “With Kistler, we have a highly reliable partner who is able to support our business across the globe – for instance, if we want to train staff in China. And Kistler also has the flexibility to offer support and development services on an individual, personal basis. That places us in an excellent position to cope with the growth we expect in the coming years and decades as the necessary phase-out of coal and oil proceeds.”
The MGT series gas turbines from MAN Energy Solutions are equipped with 6021A high temperature pressure sensors from Kistler for process monitoring and predictive maintenance.
A view of one of the test combustion chambers of the MGT6000 gas turbine from MAN Energy Solutions at HFI of TU Berlin: high-temperature pressure sensors from Kistler monitor combustion and machine condition.
The content & opinions in this article are the author’s and do not necessarily represent the views of ManufacturingTomorrow
Comments (0)
This post does not have any comments. Be the first to leave a comment below.
Featured Product
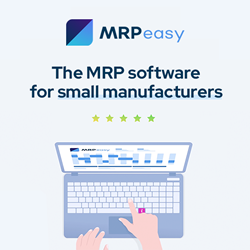