With its potential to transform the way products are designed, developed, manufactured, and distributed, 3D printing is expected to grow into an $8 billion market for the automotive industry by 2024.
3D Printing A Game-Changer For Car Makers
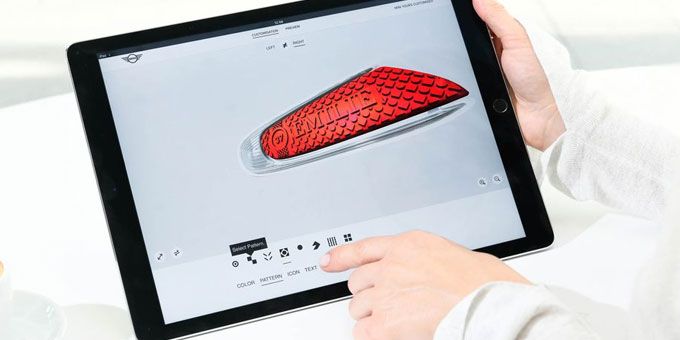
Contributed by | Zimlon
With its potential to transform the way products are designed, developed, manufactured, and distributed, 3D printing is expected to grow into an $8 billion market for the automotive industry by 2024. Many factors are driving the growth of 3D printing or additive manufacturing technology, including ease in the development of customized products, cost-effective manufacturing, government investments in 3D printing projects, and development of new industrial-grade 3D printing materials. The increasing customer demand for innovations, cleaner, lighter, and safer designs, as well as lower prices across customized products, is also encouraging the automotive 3D printing market. In addition to offering benefits such as reduced weight, energy-efficient cars, and reduced CO2 emissions of vehicles, Zimlon assesses the impact 3D printing has on the car insurance market. 3D printing is a game-changer in the spare parts industry with as many as 85% of spare parts suppliers looking at embracing 3D printing. From reduced inventory and logistics costs, with the help of 3D printing, manufacturers can store these spare-parts digitally and produce them on-demand.
Cost Savings- 3D printing can cut costs for prototyping and production. Tucci Hot Rods estimate they save about $500 per part using 3D printing methods instead of using machine-made, aftermarket solutions while car manufacturer Opel reported a tooling cost reduction of 90% for the assembly process.
Faster Prototyping- Productivity and speed have increased three-fold because 3D printing eliminates the time and effort required to create prototypes and test materials. According to BMW, 3D printed customized tools helped save 58% in overall costs and reduce project time by 92%.
Reduced Wastage- 3D printing uses material only where it’s needed, eliminating wastage by 95%. Avoiding extra costs for wasted material can revamp production processes.
Customized Cars- With 3D printing, creating multiple variants of a model can be done without much trouble. In a new service offered by MINI, customers can use 3D printing to create and order accessories to modify their MINI.
Improved Materials- Several 3D printing processes offer materials that can withstand temperatures well above the average 105 °C sustained engine compartment temperatures such as SLS nylon and photo-cured polymers.
Restoring Vintage Cars- 3D printing can also help restore vintage cars. Porsche is currently using SLM 3D printing for metal parts and SLS 3D printing for plastic parts and tooling, making a more extensive range of rare components available for collectors.
The content & opinions in this article are the author’s and do not necessarily represent the views of ManufacturingTomorrow
Comments (0)
This post does not have any comments. Be the first to leave a comment below.
Featured Product
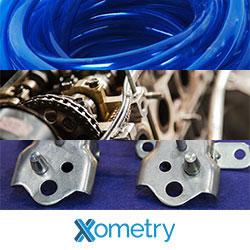