By having a local team of experts and by having local facilities, we can better service our US customers. As mentioned, our goal is to help manufacturers improve operational efficiency and profitability.
AMMEGA Group Announces Investing $100M in the Americas

Q&A with Tom Doring, President of the Americas Region | AMMEGA Group
Tell us about yourself and AMMEGA.
I’m the President of the Americas region at the AMMEGA Group and lead the core businesses of our product brands Ammeraal Beltech, Jason Industrial, and Megadyne in North America; Central and South America. AMMEGA is a global leader in industrial power transmission, lightweight process and conveyor belting, and fluid power. We aim to become the local partner of choice for sustainable belting solutions around the world, but especially here in the U.S. where manufacturing is undergoing a revival. We’re excited to draw on our legacy of innovation and global network of resources to help our customers solve some of those “who’d have thought” challenges that come along with these unique, transitional times.
You recently announced that you’ve invested $100M in the Americas; can you tell us a little bit about where this money went and how it will enhance AMMEGA’s presence in the United States?
Absolutely. The $100M investment to expand production and service capabilities is broken down between AMMEGA’s brands: Ammeraal Beltech, the only conveyor belt manufacturer with full line capabilities for both PVC and PU production in the U.S., and Megadyne, a driver of American innovation in power transmission belting. For Ammeraal Beltech, this has resulted in a new, cutting-edge conveyor manufacturing facility in Buford, Georgia which localize innovation at on-site technical solutions center and offer full production. The investment also helped fuel an expansion of our modular conveying products manufacturing facility in Reading, Pennsylvania that offers molding, assembly and more than double the previous warehouse capacity to help customers optimize inventory.
Apart from that, we’ve been proactively expanding our team of experts in the U.S. to reduce lead times, speed service pre-and post-installation. Not only does this help customers optimize their belting solutions to their application and master unusual product handling challenges for greater efficiency, but they benefit from the knock-on effect: increased uptime, achieving the highest standards of food safety and cleanliness, and reduced emissions along their supply chain.
And the investment doesn’t stop at the $100M in the American market. We’re not shying away from any incremental investments that will need to be made as we grow and learn with our U.S. customers.
Your investment comes with the “Built American Proud” slogan, could you tell us what that means to AMMEGA?
“Built American Proud” is more than a slogan. It’s an initiative. It encapsulates the ways in which AMMEGA is growing in America to help American companies grow.
We want to help fuel America’s manufacturing renaissance and accelerate the drive toward a more sustainable future. Of course, “American Proud” doesn’t mean “America alone.” We’ll never shy away from supply chain transparency. We use some imported parts and have operations worldwide—just like many of our U.S. based customers. But being a good partner means being here for our customers in every way we can. By expanding our production, warehousing, and innovation capabilities here, we can bring the benefits of our decades-old, global enterprise straight to our customers’ backyard.
How do your investments translate to American customers?
By having a local team of experts and by having local facilities, we can better service our US customers. As mentioned, our goal is to help manufacturers improve operational efficiency and profitability. That starts with hands-on partnership, ensuring shorter lead times, just-in-time service for inventory ownership, and of course, high performance belting solutions for greater reliability.
When talking about the benefits to our U.S. customers, we often tend to focus on the speed of service and the proximity of hardware. However, the software side is equally important. We noticed a scarcity in technical tradesmen which is why we are focused on localizing our personnel— engineers with skills to innovate, create custom solutions, and provide maintenance to our customers.
How does sustainability tie into your initiatives?
AMMEGA has the Ecovadis Gold Certification awarded only to top 5% of companies to affirm their commitment to eco-friendly and responsible operations. It is a testament to our practices that minimize environmental impacts with CO₂ monitoring, assess waste generation and water use, and develop increasingly sustainable belting solutions. We are not only developing products using recyclable materials, but also manufacturing and developing products where the material content is more sustainable.
With a presence in America, we have also drastically shortened shipping distances which greatly reduces CO₂ emissions associated with transportation. However, sustainability does not only relate to impacts on the environment, but also the noise pollution and overall comfort for workers in the workplace. We actively contribute to sustainability goals by making solutions that require lower maintenance and lower energy usage more accessible. AMMEGA’s initiatives align with the United Nations’ five pillars of sustainability — people, planet, prosperity, peace, and partnerships— to shape a holistic approach to sustainability.
How are belting needs changing for your U.S. customers? Can you elaborate on how these evolving needs reflect industry-wide trends and challenges across manufacturing?
Companies across the nation are re-investing in state-side operations as part of their reshoring initiatives, and they cannot afford the negative impacts of downtime. We see our clients predominantly concerned with upkeeping productivity, product supply, and sustainability. There is an industry-wide renaissance of American manufacturing with expanding efforts to meet sustainability goals, and address industry 5.0 challenges. With belting being an essential part of various industries and operations, we support our customers by helping to preserve or enhance their efficiency and productivity while they advance to the next generation of manufacturing.
Our U.S. customers are also witnessing an explosion of innovation, and thanks to our R&D mindset, we are not just a bystander but a leader of change. With significant investments made in research and technical know-how, we’re able to leverage the latest advancements in robotics and automation and improve efficiency for our customers.
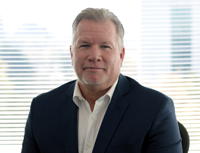
Tom Doring was appointed President of the Americas at the Ammega Group in August, 2019. He also serves on the company’s Group Executive Committee. He has direct responsibility for leading the core businesses of Ammeraal Beltech, Jason Industrial and Megadyne in North America and Central and South America.
The content & opinions in this article are the author’s and do not necessarily represent the views of ManufacturingTomorrow
Comments (0)
This post does not have any comments. Be the first to leave a comment below.
Featured Product
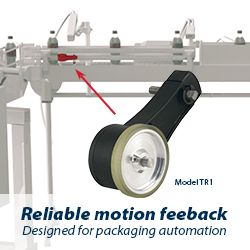